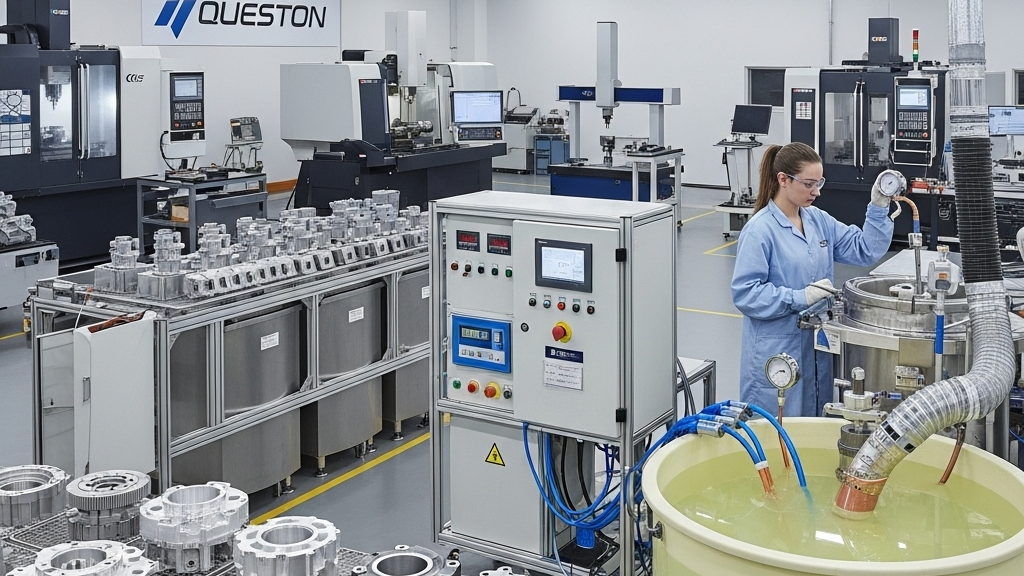
Anodizing is a common surface treatment after CNC machining, offering both corrosion resistance and visual appeal. It also helps reduce the visibility of fine machining marks. Especially in batch production of aluminum parts, high-quality surface finishes directly influence customer perception.In precision manufacturing, appearance often determines product grade.
However, not all anodizing processes can fully hide surface marks. Factors like the anodizing method, pretreatment steps, and base material properties greatly affect the final coverage result. Choosing a well-matched process is the key to true product enhancement.
Can anodizing fully conceal CNC machining marks?
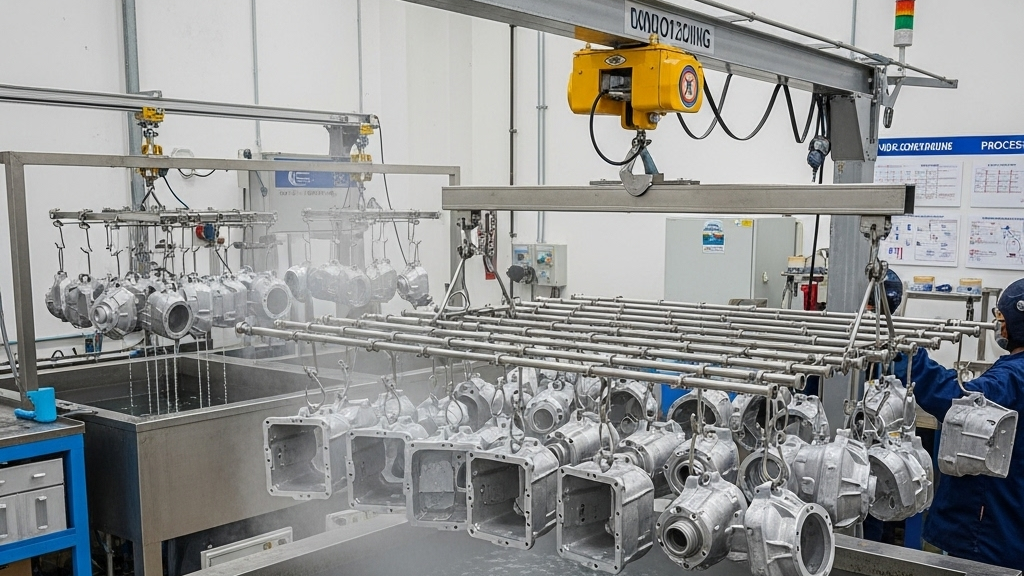
Fine grooves and tool marks from CNC cutting are often visible before treatment. While anodizing does provide some coverage, it is not a universal fix. Parts with insufficient surface roughness may still show patterns after anodizing.
- Pretreatment is critical: Optimizing anodizing pretreatment — polishing and sandblasting greatly enhance coverage.
- Film thickness matters: Anodizing thickness and coverage — thicker films offer better concealment.
- Material affects finish: Different aluminum alloys result in varying surface consistency.
- Precise process control: Voltage, electrolyte temperature, and time affect the density of the film.
Does machining texture affect anodized finish uniformity?
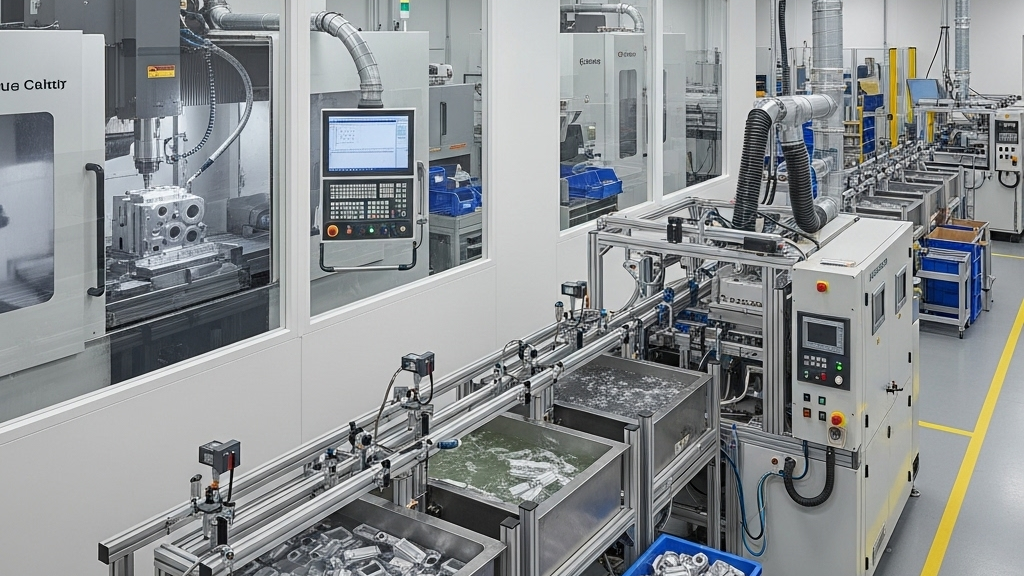
Different tool paths, speeds, and tool wear create texture variations that impact the anodized appearance. Control accuracy in toolpath is fundamental to a visually uniform result.
- Toolpath strategy matters: Toolpath effects on surface finish — finer paths favor better post-processing.
- Texture direction control: Microstructure orientation and light interaction — aligned textures reduce interference.
- Gloss adaptation: Reflectivity varies with texture, affecting uniformity.
- Heat control during machining: Heat-affected zones may cause color inconsistencies.
How well do different anodizing types hide fine imperfections?
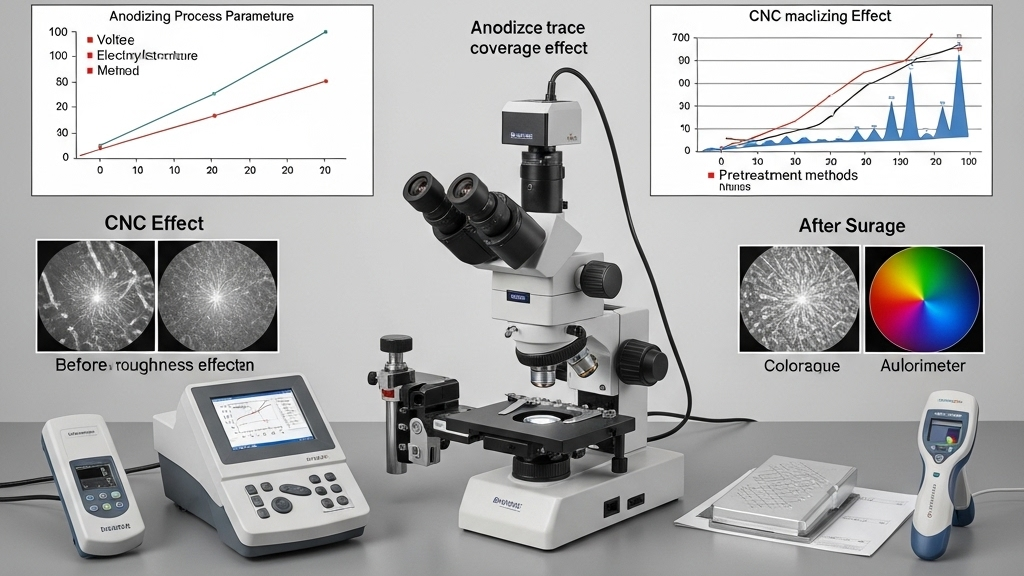
Sulfuric, hard, and colored anodizing vary in film thickness, porosity, and dyeing response, all influencing visual correction. Selecting the right combination of process and part design is key to achieving performance and aesthetics.
- Hard anodizing: Offers higher tolerance to surface imperfections.
- Standard sulfuric anodizing: Suitable for general decorative concealment.
- Plasma electrolytic oxidation: Better corrosion resistance but weaker concealment effect.
- Dye compatibility: Darker dyes mask flaws better than lighter ones.
Comparison of Four Anodizing Methods in Mark Coverage
Category |
Hard Anodizing |
Standard Anodizing |
Plasma Electrolytic |
Chemical Oxidation |
CNC Mark Coverage | High | Medium | Low | Poor |
Cost Efficiency | Medium | Low | High | Low |
Material Compatibility | Wide | Wide | Limited | Limited |
Finish Uniformity | High | Medium | High | Low |
Dye Compatibility | Average | High | Poor | Poor |
Corrosion Resistance | High | Medium | High | Low |
Surface Hardness | High | Medium | High | Low |
Process Stability | Medium | High | Low | High |
Application Scenario Analysis
CNC-anodized parts are widely used in consumer electronics, medical housings, and premium custom components. Their surface quality plays a crucial role in product value. In industries demanding both functionality and aesthetics, anodizing performance often determines market approval.
1.Consumer electronics: High demand for visual consistency and mark concealment.
2.Medical device housings: Focused on antibacterial properties and film stability.
3.Industrial component protection: Prioritizes durability and corrosion resistance over appearance.
4.Custom luxury fittings: Consistent finish directly affects perceived value.
Conclusion
Although anodizing is not a perfect masking solution, when paired with proper CNC strategies and surface pretreatments, it can significantly reduce the visual impact of minor defects. The key lies in process design that minimizes texture interference from the start.By selecting the right type of anodizing and dyeing technique, manufacturers can greatly enhance finish consistency and overall appeal.
For expert assistance in implementing anodizing strategies for your production needs, visit our resource center or contact us. Let’s help you scale up your manufacturing with precision and efficiency!
Post time: Jun-24-2025