
ABS plastic sheets are widely used due to their excellent comprehensive properties. However, ABS itself is flammable, making flame retardant modification crucial. Different flame retardancy ratings are set to meet the safety requirements of different application scenarios. Understanding these ratings and their application limitations is essential to ensuring product safety.
Various flame retardancy standards have been established for ABS plastic sheets within the industry, such as UL 94. Different ratings (such as HB, V-2, V-1, V-0, etc.) represent different performances of the material in combustion tests. The technical characteristics and testing standards of these flame retardancy ratings are different. So, what are the common flame retardancy ratings for ABS plastic sheets? And what application limitations are determined by their characteristics?
How are common ABS flame retardancy ratings classified?
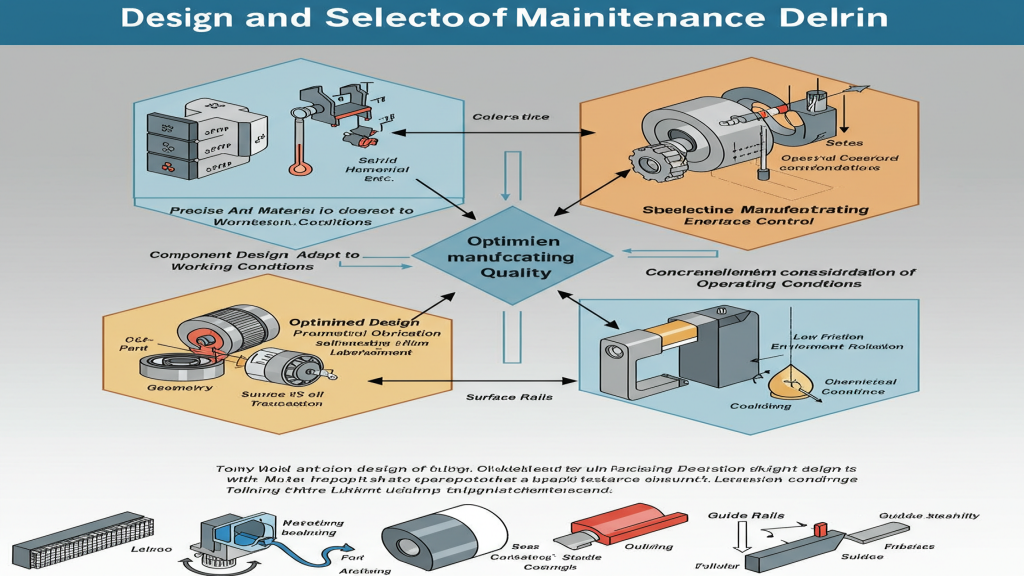
Currently, the flame retardancy ratings of ABS plastic sheets are mainly classified according to the UL 94 standard, which evaluates the combustion characteristics of materials by simulating flames. These ratings represent different behaviors of the material after ignition, such as flame spread rate, self-extinguishing capability, and whether or not burning drips are produced.
- HB Rating: Slow horizontal burning rate, but cannot prevent flame spread and dripping.
- V-2 Rating: Vertical burning self-extinguishes, but burning drips are allowed to ignite cotton.
- V-1 Rating: Vertical burning self-extinguishes faster, drips must extinguish before dropping.
- V-0 Rating: Vertical burning self-extinguishes rapidly and no burning drips are allowed.
What are the testing standards for different flame retardancy ratings?
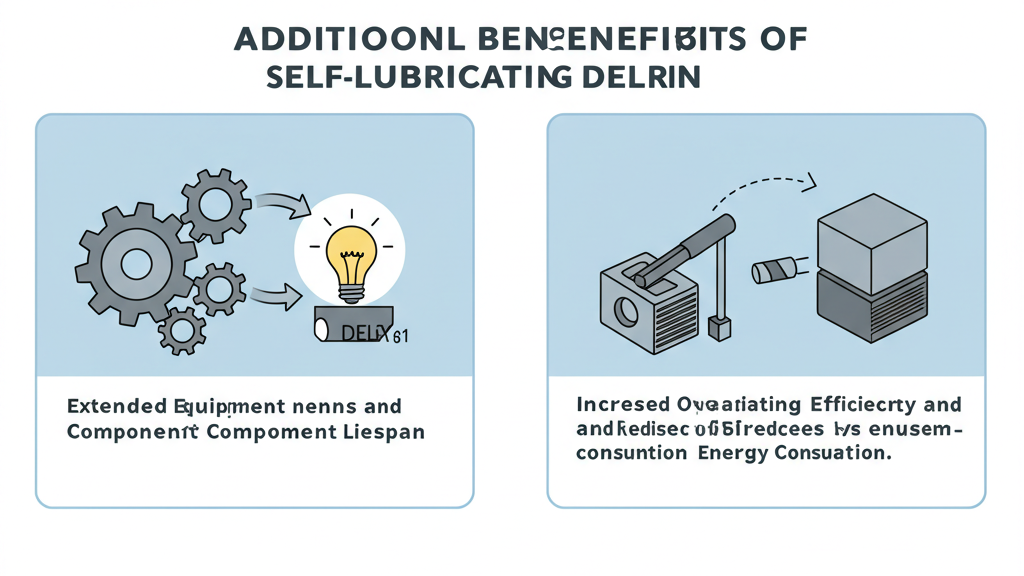
For ABS plastic sheets with different flame retardancy ratings, performance evaluation is mainly based on a series of rigorous testing standards. These standards aim to quantify the burning behavior of materials by simulating actual fire conditions, thereby determining their flame retardancy rating and reflecting their safety in the event of a fire.
- UL 94 Horizontal Burning Test: Evaluates the material’s resistance to flame spread in the horizontal direction.
- UL 94 Vertical Burning Test: Evaluates the material’s self-extinguishing capability and the ignitability of drips in the vertical direction.
- Oxygen Index Test (LOI): Measures the minimum oxygen concentration required for a material to burn; the higher the value, the less flammable.
- Glow Wire Test (GWT): Evaluates the material’s ability to resist ignition caused by a heat source.
Application Advantages and Limitations of Each ABS Grade?
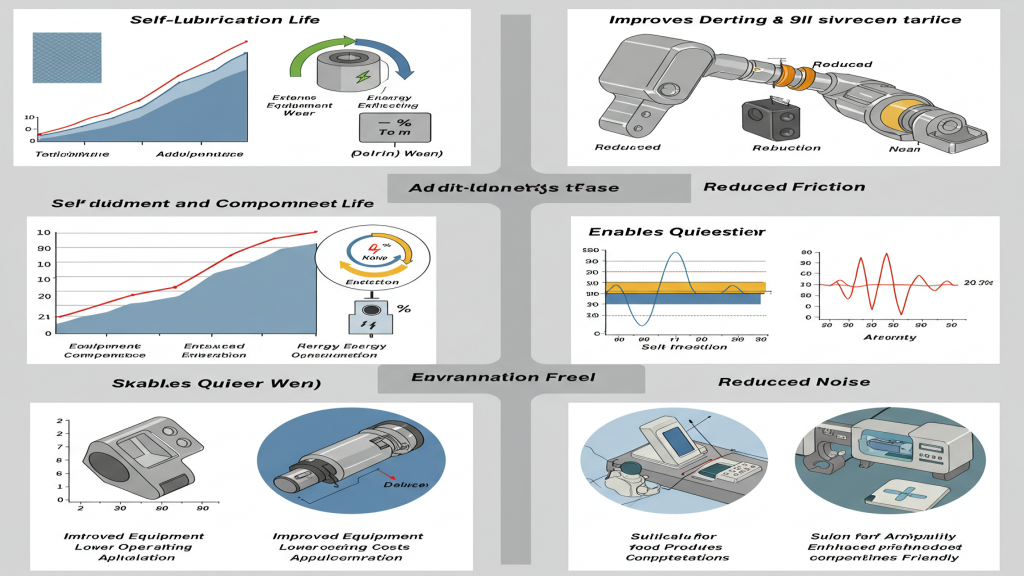
Due to the differences in fire resistance performance, ABS plastic sheets with different flame retardancy ratings exhibit their own unique advantages and limitations in practical applications. These characteristics directly determine their applicable scope and performance in different industries and fields. For example, in the electronics and electrical appliance industry, where safety requirements are extremely high, the selection of flame retardancy ratings is particularly critical.
- HB Grade: Low cost, easy to process, but poor flame retardancy, mostly used for non-critical components with low fire protection requirements.
- V-2 Grade: Improved flame retardancy, moderate cost, but burning drips may cause secondary fires.
- V-1 Grade: Stronger self-extinguishing capability, drips can self-extinguish, widely used in electronics and electrical appliances and automotive interiors.
- V-0 Grade : Optimal flame retardancy performance, highest safety, often used in high-demand areas such as high-end electronics and electrical appliances, medical, and construction.
Characteristics and typical application limitations
Flame Retardant Grade |
Main Characteristics |
Typical Application Areas |
Main Application Limitations |
HB | Slow horizontal burning rate | Decorative parts of home appliances, toys, stationery, etc. | Not suitable for applications with fire safety requirements |
V-2 | Self-extinguishing vertical burning, allows flaming drips that ignite cotton | Some electronic and electrical component housings, office equipment, etc. | Limited in applications with strict restrictions on dripping |
V-1 | Faster self-extinguishing vertical burning, drips must extinguish before falling | Housings of electronic and electrical products (e.g., TVs, monitors), some automotive interior parts | Relatively higher cost |
V-0 | Rapid self-extinguishing vertical burning, no flaming drips | High-end electronic and electrical housings, medical equipment, aerospace interiors, high fire-rated components in construction, critical safety parts in automotive interiors | Higher cost, potentially slightly higher processing difficulty |
Application Limiting Factors
When selecting ABS plastic sheets for specific scenarios, in addition to the critical factor of their flame retardancy rating, it is also necessary to comprehensively consider multiple factors such as cost, processing performance, and environmental requirements. The final material selection often requires seeking an optimal balance between flame retardancy, economy, processability, and environmental friendliness to meet the comprehensive needs of specific application scenarios.
1.Cost Factors: Higher flame retardancy ratings are usually accompanied by higher material costs.
2.Processing Performance: Adding flame retardants may affect the flowability and moldability of ABS. High flame retardancy grade materials may have increased processing difficulty or cost.
3.Environmental Requirements: Environmental regulations and consumer preferences restrict the use of certain traditional flame retardants. Environmentally friendly flame retardant ABS may face challenges in terms of cost or performance.
4.Physical and Mechanical Properties: Increasing the flame retardancy rating sometimes sacrifices other physical and mechanical properties of ABS, requiring a trade-off between comprehensive properties.
Conclusion
In practical applications, material selection is not solely determined by the flame retardancy rating. Factors such as cost, processing performance, environmental requirements, and physical and mechanical properties also play important roles and may create mutual constraints with the flame retardancy rating.
For expert assistance in implementing for your production needs, visit our resource center or contact us. Let’s help you scale up your manufacturing with precision and efficiency!
Post time: May-07-2025