Introduction
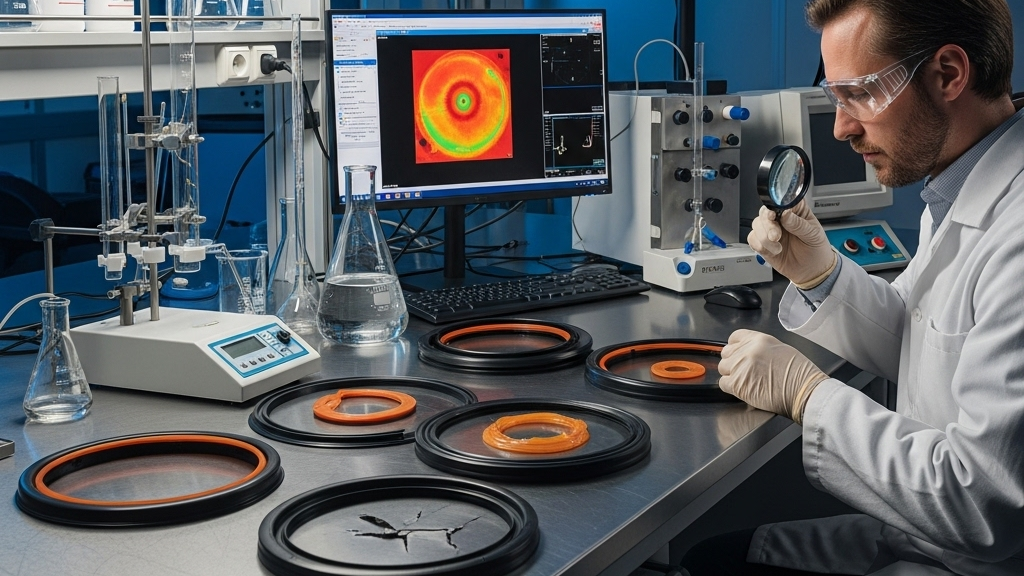
The performance of silicone seals is finalized during the vulcanization stage, and precise control of this process is vital for product consistency. Mastering the “golden window” of vulcanization directly affects yield rate, production efficiency, and customer satisfaction.Seizing the optimal vulcanization timing is key to controlling product quality.
Over-vulcanization or under-curing can lead to sealing failures, dimensional deviations, or mold sticking issues, increasing rework costs. By precisely setting temperature and time, production stability can be effectively managed.Temperature and time control are the foundation for ensuring vulcanization consistency.
Why is the “Golden Window” So Critical?
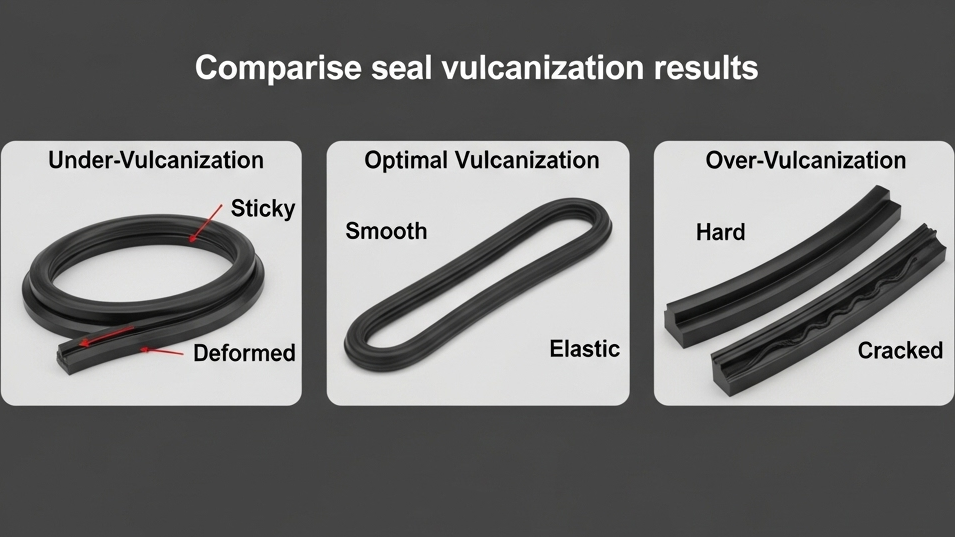
The vulcanization reaction is a dynamic process governed by both time and temperature, and any deviation can result in defects. Improper temperature control often causes bubbles and shrinkage issues.
- Optimal Temperature Range: 170°C~200°C promotes ideal crosslinking.
- Time Sensitivity Analysis: 3–5 minutes is the critical stage for most silicone products.
- Mold Temperature Control: Uniform mold temp enhances vulcanization consistency.
- Additive Adjustment: Cure agent ratios affect the reaction window.
The vulcanization window determines the product’s consistency and performance.
How to Avoid Errors Outside the Vulcanization Window?
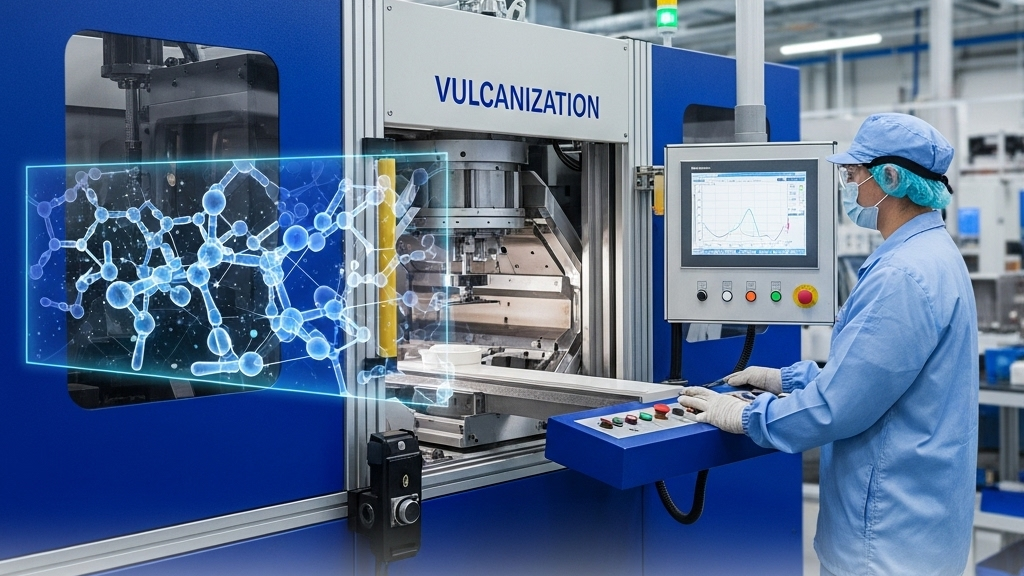
Without strict control, over-curing, under-curing, or shrinkage can occur, compromising the seal’s performance. Automated monitoring systems can effectively prevent uncontrolled vulcanization.
- Smart Temperature Controllers: Real-time mold cavity temp detection ensures reaction stability.
- Material Storage Management: Prevents aging or loss of reactivity.
- Exhaust Design: Proper venting avoids uneven curing.
- Press Precision: Stable clamping enhances repeatability.
Precise thermal control and equipment stability are crucial to maintaining process stability.
What Process Details Define the “Window”?
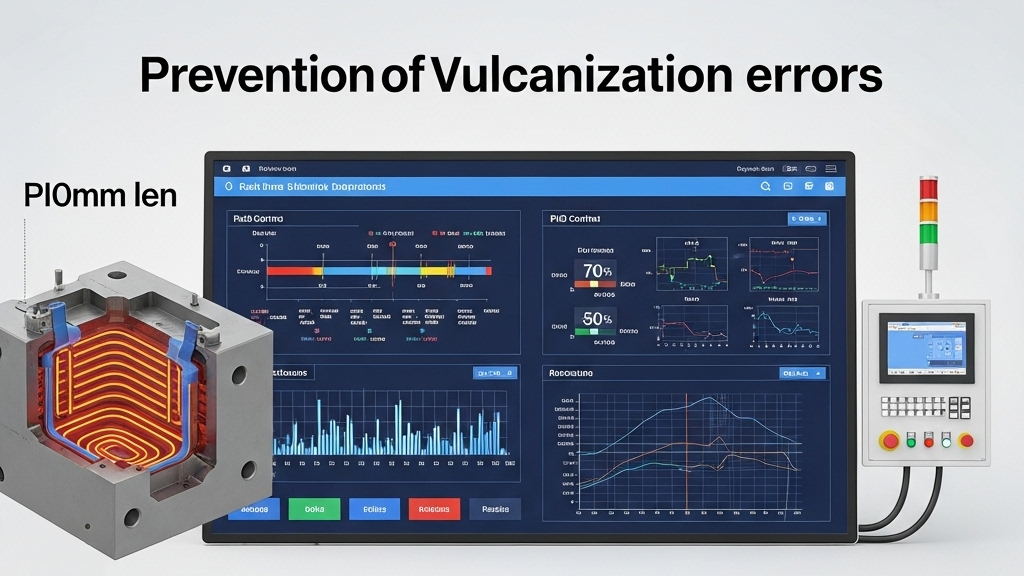
Mold design, material ratio, and injection rate all influence the vulcanization window. Optimized formulations can significantly widen the vulcanization window and improve tolerance.
- Thermal Conductivity of Molds: Improved channels accelerate heat balance.
- Curing Agent Selection: Determines onset temperature and rate.
- Injection Rate Control: Impacts preheat and curing progression.
- Pressure Holding: Time under pressure affects crosslinking quality.
Structure, material, and parameters together define the vulcanization window’s quality.
Comparison of Key Factors Influencing the Vulcanization Window
Item |
Mold Temp Control |
Holding Time |
Cure Agent Ratio |
Injection Speed |
Cycle Time Impact | High | Medium | Medium | High |
Surface Defect Risk | Medium | Low | High | Medium |
Seal Uniformity | High | High | Medium | Low |
Process Stability | High | Medium | Medium | Medium |
How to Secure the “Golden Window” Using Automation?
Silicone vulcanization has moved toward intelligent control. From thermocouples in the mold to closed-loop systems, automation ensures consistent part quality. Digital feedback systems greatly reduce human error impacts.
1.Thermal Flow Automation: Improves temperature consistency across cavities.
2.Smart Data Logging: Every cycle is traceable.
3.Window Alerts: Notifications when variables exceed target ranges.
4.One-Touch Setup Switching: Adjusts to batch or mold changes.
Conclusion
The “golden window” in silicone seal vulcanization is the focal point of process control, determining dimensional stability and sealing function. Effective parameter control and automation are essential for consistency.
In a dynamic manufacturing environment, accurately defining and applying this window significantly reduces defects and rework. Balancing temperature, time, and pressure unlocks stable, efficient production.
For expert assistance in implementing for your production needs, visit our resource center or contact us. Let’s help you scale up your manufacturing with precision and efficiency!
Post time: Jul-16-2025