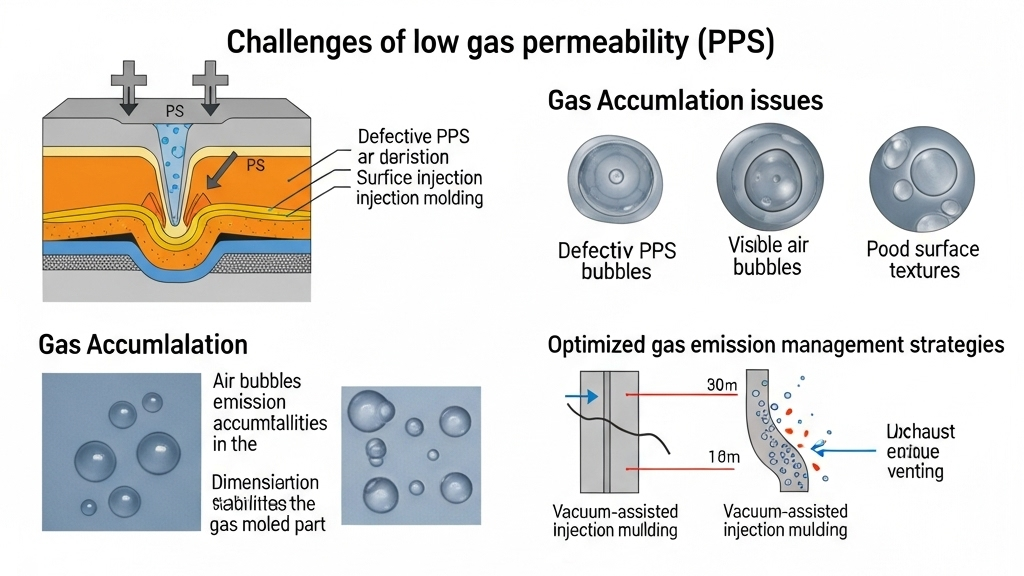
PPS (Polyphenylene Sulfide) is known for its excellent chemical stability and high temperature resistance in injection molding. While these outstanding properties make PPS an ideal choice for high-demand environments, its low gas permeability is often overlooked. Low gas permeability can lead to gas accumulation and product defects during the injection molding process, affecting production efficiency and final product quality.
Understanding the impact of PPS’s low gas permeability is crucial for improving the quality of injection molded products. Optimizing gas emission management and technical solutions can significantly enhance the stability of the injection molding process, thereby reducing the occurrence of production issues.
Why is PPS’s low gas permeability a critical issue?
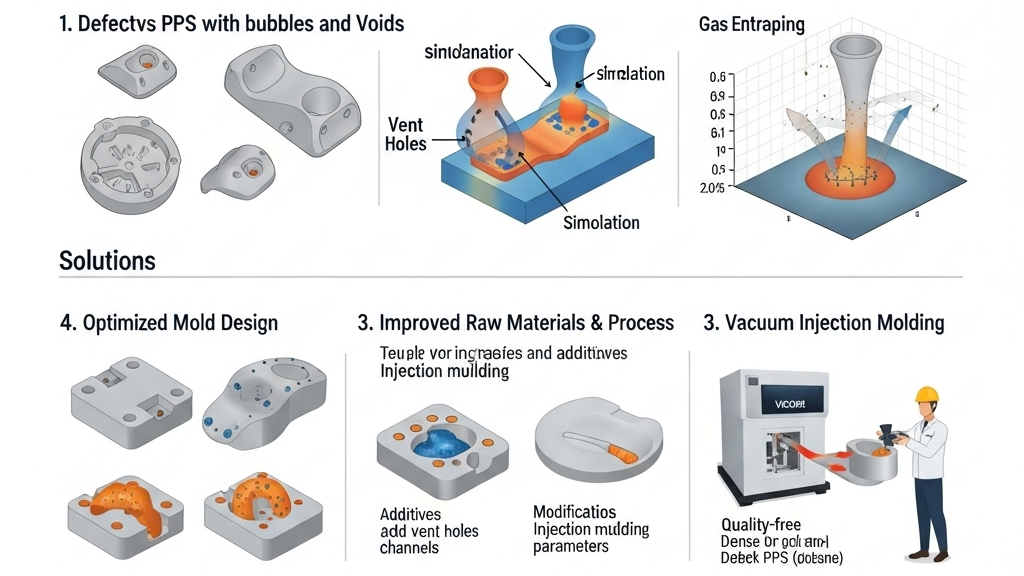
PPS’s low gas permeability can result in gas accumulation and trapped air bubbles within the product. If not addressed, this issue directly impacts the final product’s strength and appearance. Through proper mold design and production processes, the risk of gas accumulation can be effectively minimized, ensuring the product meets quality standards.
- Optimize mold design: Increase vent holes for better gas emission
- Improve raw material quality: Use suitable additives to enhance gas flow
- Adjust production processes: Properly control injection pressure and speed
- Use vacuum injection molding: Eliminate air during production to ensure high-quality products
How can PPS’s gas permeability be improved?
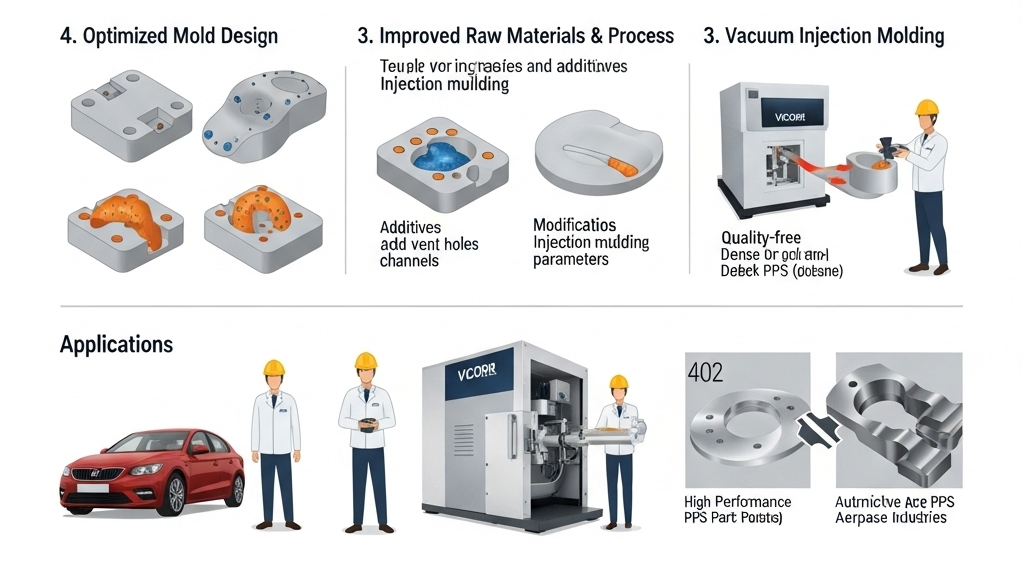
Improving PPS’s gas permeability requires a multi-faceted approach, including optimizing the production process and using suitable additives. With the right production technology, gas bubbles can be prevented, while ensuring the strength and stability of the product. Choosing the right venting techniques can significantly enhance production efficiency and product quality.
- Use molds with stronger venting features: Increase gas emission speed
- Adjust injection pressure and timing: Control gas accumulation during molding
- Select appropriate auxiliary equipment: Such as vacuum pumps to accelerate gas emission
- Optimize raw material formulations: Use more effective additives
How can technology improve PPS’s gas emission efficiency?
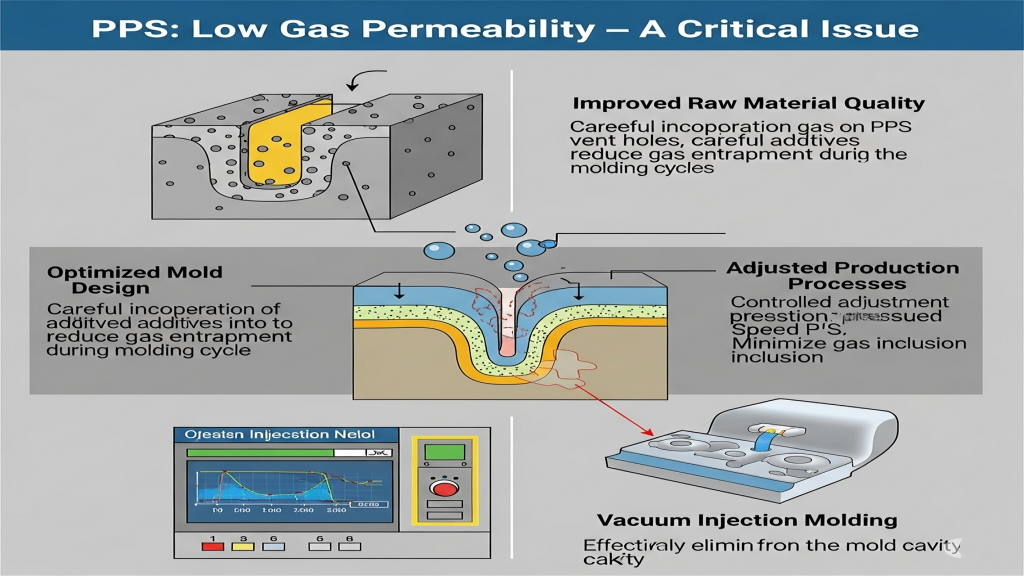
In the process of improving PPS’s low gas permeability, advanced technologies play a critical role. By combining modern injection molding equipment and techniques, gas retention time during production can be effectively reduced, enhancing venting efficiency. Advanced venting technologies, such as high-precision mold design and vacuum injection molding, help reduce production defects and improve product quality.
- Precision mold design: Ensure more efficient gas flow
- Use automation control systems: Precisely regulate gas emission
- Introduce new venting technologies: Enhance gas emission efficiency
- Optimize mold cleaning processes: Regularly check molds to ensure no gas blockages
Comparison of PPS Low Gas Permeability Improvement Solutions
Technology/Method |
Advantages |
Disadvantages |
Application Field |
Cost |
Optimized Mold Design | Improves gas emission efficiency | Requires redesigning molds | Precision Molding | Medium |
Vacuum Injection Molding | Efficient venting, prevents bubbles | Requires high-end equipment | High-Temperature Fields | High |
High-efficiency Vent Materials | Enhances gas channels, improves venting | Higher material cost | Specialized Applications | High |
Injection Molding Process Adjustment | Low cost, easy operation | May affect production cycle | Standard Molding | Low |
The Impact of Low Gas Permeability on PPS Injection Quality
Low gas permeability in PPS injection molding can cause issues such as air bubbles and cracks, affecting both the product’s strength and appearance. Improving mold design and production processes can effectively reduce these issues, ensuring the product’s quality.
1.Impact on Product Strength: Gas bubbles cause uneven internal stress, reducing strength.
2.Impact on Aesthetic Quality: Bubbles and cracks affect appearance, diminishing product aesthetics.
3.Increased Production Costs: Frequent inspections and repairs are required.
4.Reduced Production Efficiency: Ongoing quality issues lead to production halts.
Conclusion
PPS’s low gas permeability is a significant factor affecting the quality of injection-molded products, requiring optimization of mold design and injection molding processes. Improving gas emission efficiency during injection molding effectively enhances both product quality and production efficiency, meeting high production standards.
For expert assistance in implementing for your production needs, visit our resource center or contact us. Let’s help you scale up your manufacturing with precision and efficiency!
Post time: Jul-04-2025