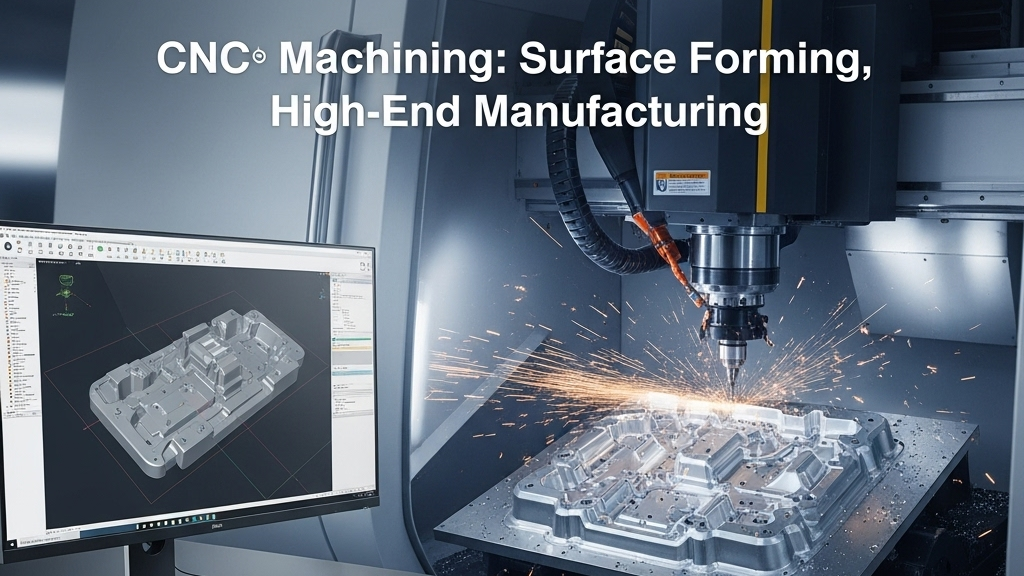
In injection mold manufacturing, complex 2.5D and 3D surfaces are becoming increasingly common, demanding more from CNC machining technology. Especially for appearance parts such as lighting and automotive trims, the surface must be extremely flat and consistent. The quality of the mold directly determines the final product performance.
Multi-axis CNC machining, 3D path planning, and simulation become the key to ensuring precise surface machining. With optimized processing schedules and toolpath control, complex surfaces can be formed efficiently with minimal post-processing. Mastering CNC machining for complex surfaces is foundational for mold companies entering high-end manufacturing.
How does CNC achieve precision in complex surfaces?
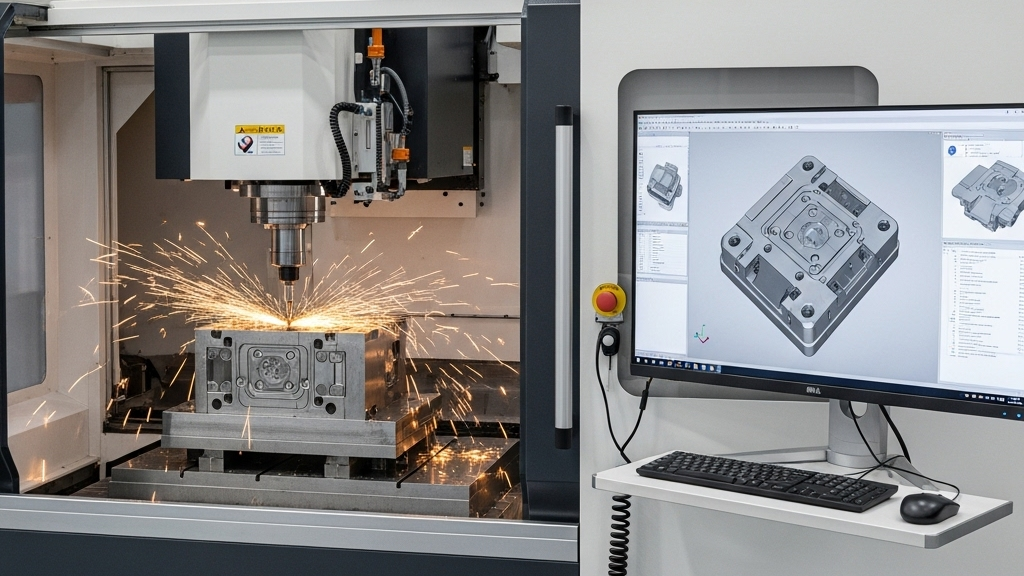
CNC surface machining requires highly synchronized software programming, toolpath control, and machine rigidity. Achieving high accuracy starts from surface reconstruction, tool selection, and cutting strategy optimization. Proper toolpath planning determines cutting efficiency and surface finish.
- Multi-Axis Machining: 5-Axis Benefits Enables cutting from multiple angles in a single setup.
- Path Optimization: PowerMill Toolpath Analysis Enhances continuity and reduces redundant moves.
- High-Speed Tools: Small-diameter tools suit fine detail carving under high RPM.
- Simulation Verification: Prevents interference and overcuts, ensuring accuracy.
How to manage curvature transitions and draft angles in CNC machining?
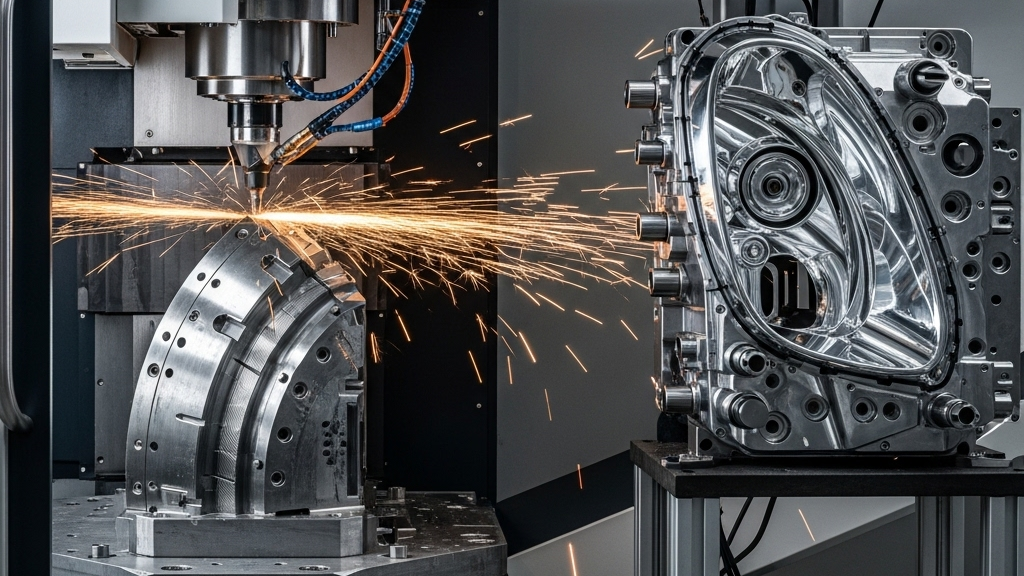
Complex 2.5D/3D surfaces often encounter issues with draft angles in transition areas, leading to demolding problems or surface sink marks. It is essential to account for these transitions in the mold design phase. Proper draft angle design helps avoid downstream molding defects.
- Curvature Analysis: Moldflow Curvature Check Flags high-risk areas early.
- Contour Machining Strategy: Layered contouring controls curvature changes effectively.
- Undercut Optimization: Design split lines to avoid interference.
- Fillet Compensation: Connects surfaces with radii to enhance mold release.
Can CNC improve surface gloss of transparent components?
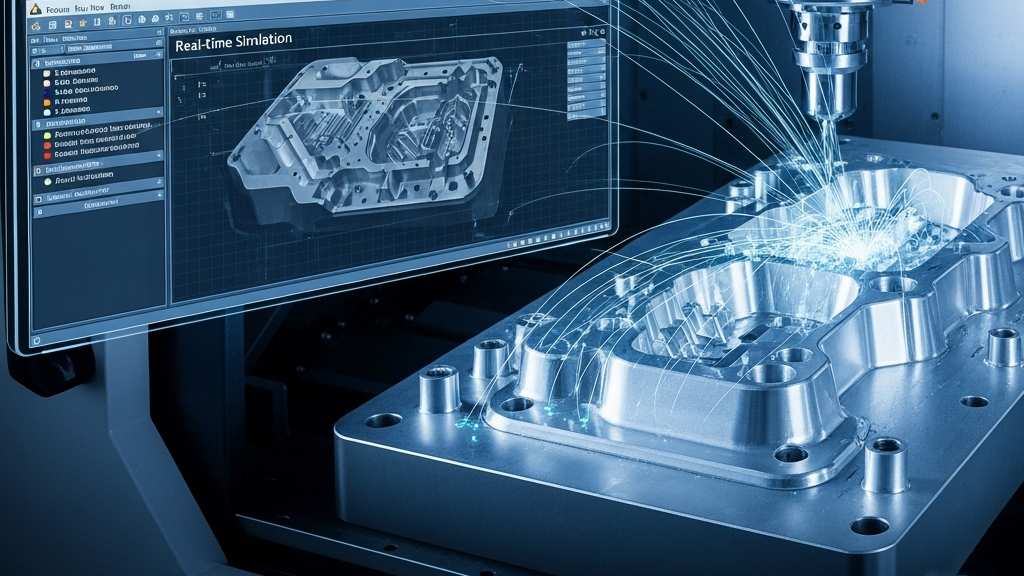
CNC plays a crucial role in mold making for lighting and optical components. High-gloss 3D surfaces reduce polishing steps and influence final light transmittance. Better CNC surface quality shortens lead times and cuts post-process costs.
- Fine Tools: CNC Mirror Tool Tech Suitable for reflective transparent surfaces.
- Optimized Cutting Parameters: Feed rates and RPM are critical to reduce surface texture.
- Minimal Post-Processing: Surfaces meet Ra standards directly after milling.
- Overlapping Pathing: Spiral or raster paths improve uniformity.
CNC Performance Comparison in Complex 3D Mold Details
Machining Type |
Surface Suitability |
Precision |
Speed |
Cost Control |
Surface Finish |
Post-processing |
3-Axis CNC | Simple 2.5D surfaces | Medium | Fast | High | Average | Required |
4-Axis CNC | Rotational/angled planes | High | Medium | Moderate | Good | Depends |
5-Axis Simultaneous | Freeform 3D surfaces | Excellent | Slow | High | Excellent | Not required |
EDM + CNC Hybrid | Hard complex structures | High | Slow | Expensive | Superior | Minimal |
Extended Value of CNC in Mold Fabrication
With diversified product design demands, CNC has become more integrated in mold manufacturing. It’s more than just a tool—it’s a strategic component in mold development. Deep utilization of CNC capabilities is key to increasing product flexibility and production efficiency.
1.Integrated Machining: Combines EDM and milling for enhanced efficiency.
2.Rapid Prototyping Support: Speeds up custom development cycles for transparent parts.
3.Design-Manufacturing Synergy: CAD-CAM integration ensures seamless transitions.
4.Auto Tool Changer: Increases flexibility in continuous complex surface processing.
Conclusion
CNC technology is redefining boundaries in mold manufacturing, especially in handling complex and optical surfaces. With multi-axis strategies, path optimization, and simulation, businesses can strike a better balance between cost and lead time. Mastering CNC strategies for complex surfaces is a key differentiator in high-end mold manufacturing.
For expert assistance in implementing for your production needs, visit our resource center or contact us. Let’s help you scale up your manufacturing with precision and efficiency!
Post time: Jul-03-2025