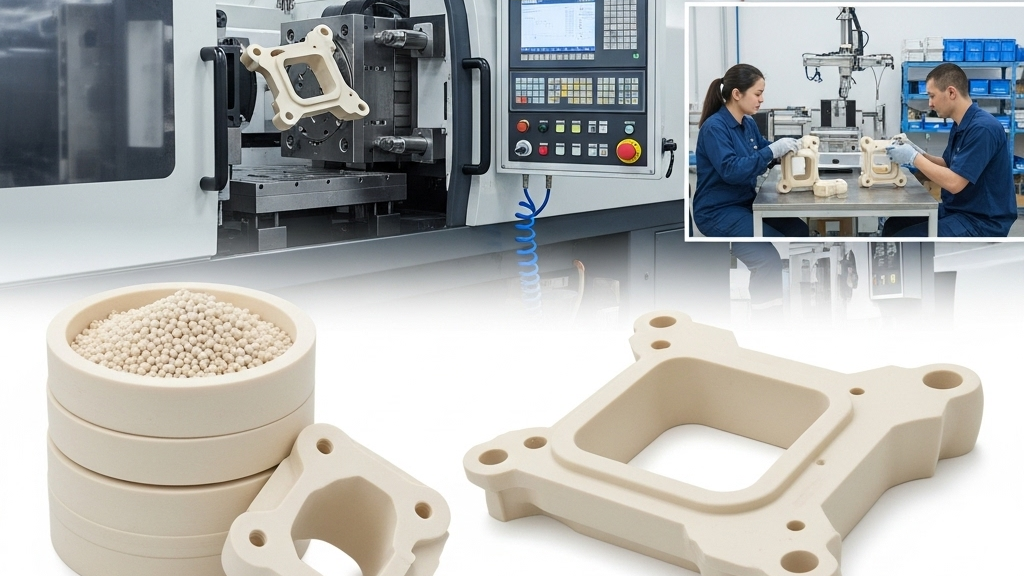
In modern manufacturing, improving product assembly efficiency is crucial. Companies are actively seeking innovative materials and processes to streamline operations, reduce costs, and optimize product quality. Delrin (Polyoxymethylene, POM), as a high-performance engineering plastic, has become an ideal choice in the injection molding field due to its excellent mechanical properties and dimensional stability. This article will explore how Delrin injection molding can optimize product assembly processes, thereby enhancing manufacturing efficiency and competitiveness.
The unique advantages of Delrin material, fully demonstrated through precision injection molding, directly improve assembly efficiency. Its excellent flowability allows for the integral molding of complex components, reducing the number of parts and connection points. At the same time, Delrin’s outstanding dimensional stability effectively avoids poor fit during assembly. In addition, the material’s low coefficient of friction and self-lubricating properties simplify lubrication requirements, further shortening assembly time.
How do Delrin Properties Simplify Part Design and Assembly?
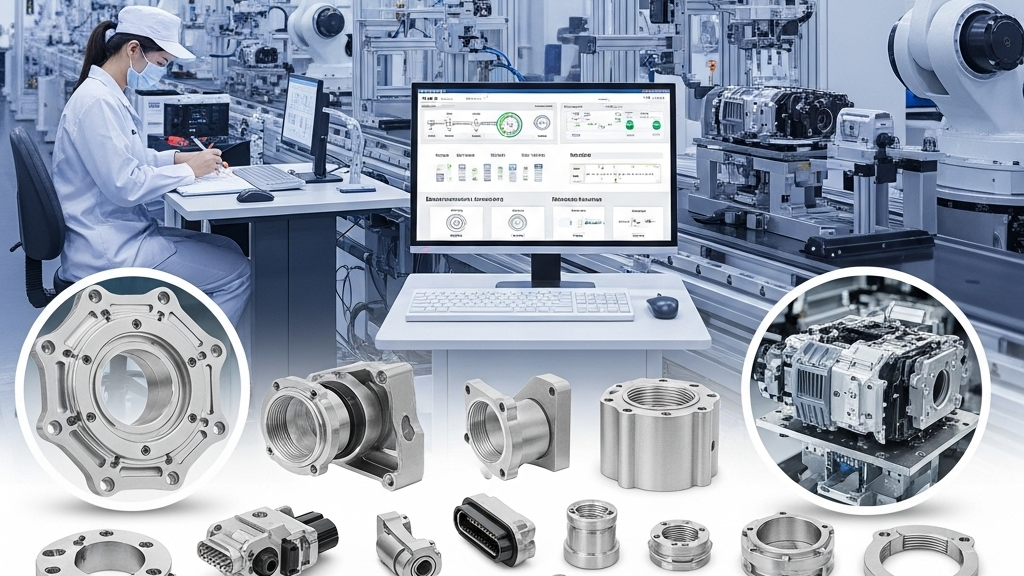
Delrin’s exceptional material properties provide significant advantages for product design, enabling the integration of multiple part functions into a single injection-molded component. This fundamentally reduces the number of required components, thereby simplifying the overall product structure and subsequent assembly processes.
- Functional Integration: Delrin’s high strength and rigidity allow for the integration of multiple part functions into a single injection-molded part, significantly reducing the number of components and assembly steps.
- Dimensional Accuracy: Delrin’s excellent dimensional stability and precision molding capabilities ensure precise fitting of parts, reducing assembly rework and adjustments.
- Self-Lubricity: Delrin’s inherent low friction and self-lubricating properties eliminate the need for additional lubrication, simplifying the assembly process.
- Integrated Connection: Delrin’s excellent fatigue resistance supports integrated snap-fit designs, replacing traditional connection methods and enabling fast, tool-free assembly.
How Does the Precision of Delrin Injection Molded Parts Enhance Assembly Efficiency?
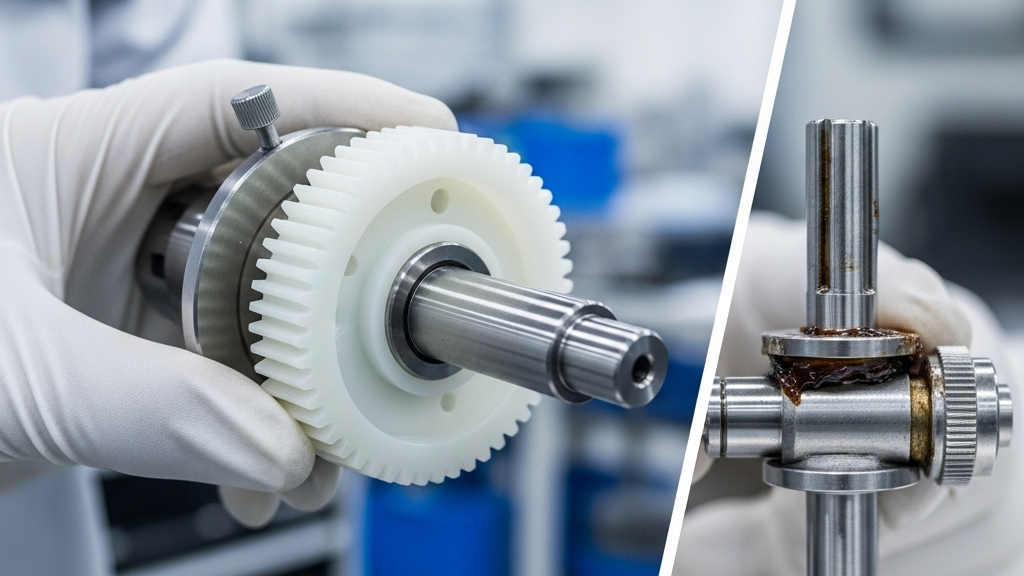
The superior dimensional accuracy and stability of Delrin injection molded parts are key to optimizing product assembly processes. They ensure a perfect fit between components, significantly reducing errors and unnecessary time consumption during assembly.
- Predictable Shrinkage: Delrin’s precisely controllable shrinkage rate results in extremely small dimensional tolerances for injection molded parts, ensuring tight and smooth fitting of components.
- Excellent Dimensional Stability: Delrin maintains dimensional stability even under environmental changes, preventing part deformation and ensuring assembly reliability.
- Reduced Tolerance Accumulation: Delrin’s high precision effectively reduces the tolerance of individual parts, thereby lowering the risk of cumulative tolerance in the overall assembly.
- Boost for Automated Assembly: Delrin’s highly consistent dimensions and shapes make it ideal for automated production lines, significantly increasing assembly speed and efficiency.
How Does Delrin’s Self-Lubricity Optimize Assembly Processes?
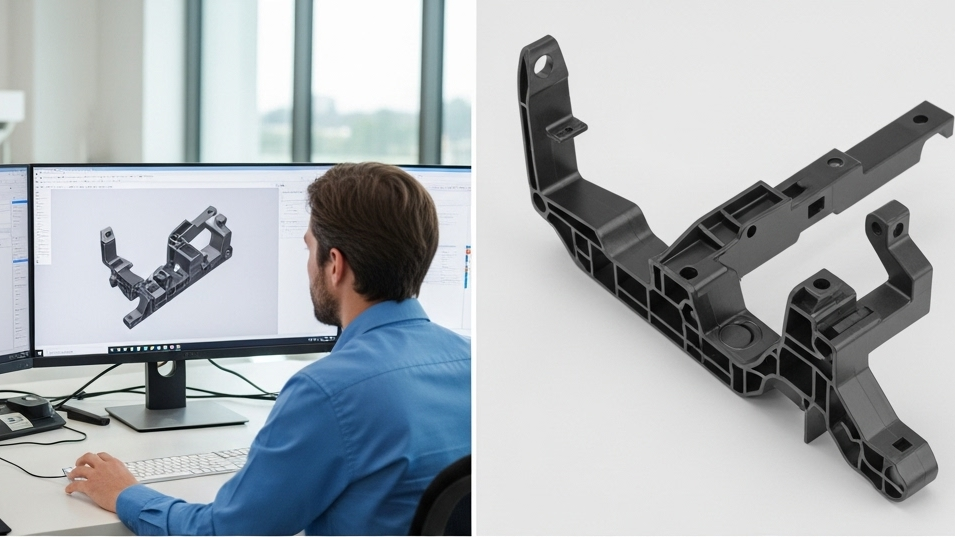
Delrin’s inherent self-lubricating and wear-resistant properties bring revolutionary optimization to product assembly. These superior properties make traditionally necessary lubricants or separate bushings redundant, thereby significantly simplifying the assembly process.
- Elimination of External Lubrication: Delrin’s inherent low friction characteristics eliminate the need for additional lubricants during assembly.
- Replacement of Traditional Bushings: Thanks to its wear resistance and dimensional stability, Delrin can be used directly as sliding components, replacing separate bushings and reducing parts and assembly steps.
- Simplified Assembly Process: Without the need for lubrication or bushing installation, Delrin parts can be assembled directly, simplifying the tools and operations required.
- Improved Long-Term Reliability: Delrin’s self-lubricating properties ensure continued low friction throughout the product’s life cycle, reducing maintenance needs and improving long-term reliability.
Advantages of Delrin injection molding
Optimization Area | Key Delrin Advantage | How it Simplifies Product Assembly |
Design Simplification | High strength & stiffness, supports functional integration | Reduces part count, enables consolidated designs, lowers assembly complexity |
Precision Enhancement | Excellent dimensional stability & predictable shrinkage | Ensures precise part fit, minimizes tolerance stack-up and rework |
Process Optimization | Self-lubricating, low friction, high wear resistance | Replaces traditional lubricants and bushings, streamlines assembly steps, reduces labor time |
Automation Enabler | Highly consistent dimensions, suitable for robotic handling | Boosts automation efficiency and reliability, decreases manual intervention and costs |
The Impact of Delrin Injection Molding on Cost-Effectiveness
Adopting Delrin injection molding technology goes far beyond simply manufacturing high-quality parts. It triggers a series of synergistic effects throughout the production line, profoundly impacting automation levels and cost-effectiveness. The inherent advantages of this material, combined with precision injection molding processes, significantly optimize production flow, resulting in comprehensive operational benefits for businesses.
1.Increased Automation: The high precision and stability of Delrin injection molded parts make them perfectly suited for automated production lines, reducing manual intervention and increasing efficiency.
2.Lowered Operating Costs: Delrin’s self-lubricating properties reduce material and labor requirements, shorten injection molding cycles, and thus lower overall operating costs.
3.Optimized Supply Chain: Delrin’s integrated designs reduce the number of part types, simplifying supply chain and inventory management, and improving efficiency.
4.Improved Product Quality: The high precision of Delrin components reduces assembly defects and scrap rates, improving first-pass yield and brand reputation.
Conclusion
Delrin injection molding plays a central role in optimizing product assembly. Its exceptional material properties, such as high strength, rigidity, and dimensional stability, can significantly simplify component design, enabling functional integration and thereby reducing the number of parts. At the same time, Delrin’s high precision and self-lubricity effectively improve component fit, significantly shortening assembly time and reducing rework rates.
For expert assistance in implementing for your production needs, visit our resource center or contact us. Let’s help you scale up your manufacturing with precision and efficiency!
Post time: May-22-2025