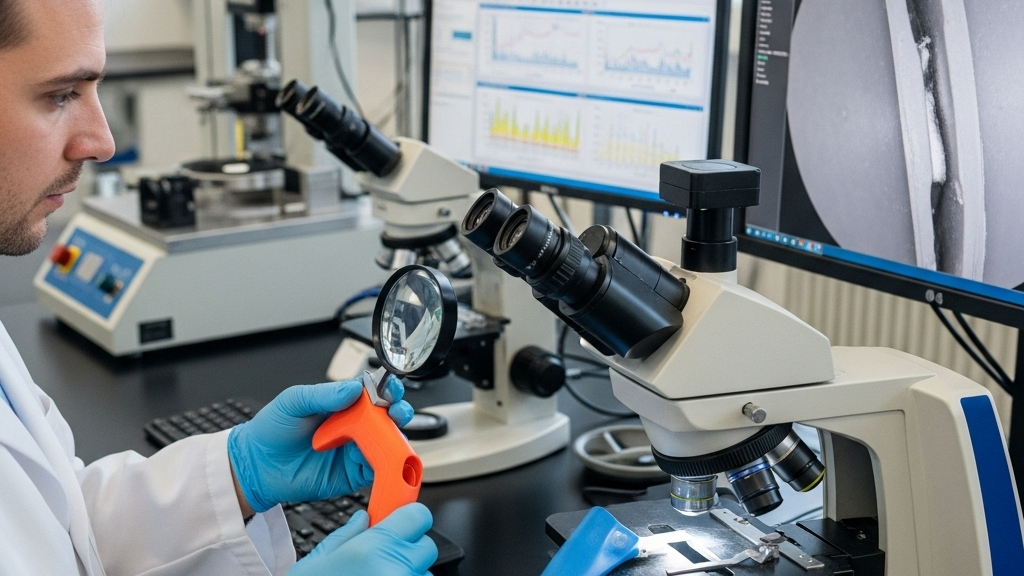
Overmolding is a process that bonds two different materials through injection molding, often used in soft-hard combinations, anti-slip grips, or structural reinforcement. It improves product appearance, touch, and offers greater design flexibility. This process plays a key role in enhancing product value and brand identity.
In high-demand industries like medical, electronics, and automotive interiors, overmolding has become the preferred solution for structure and function integration. With proper material selection, mold design, and process optimization, manufacturers can deliver highly competitive products. The perfect match between material and process is the core of premium overmolding.
Why Is the Bonding Weak in Overmolding?
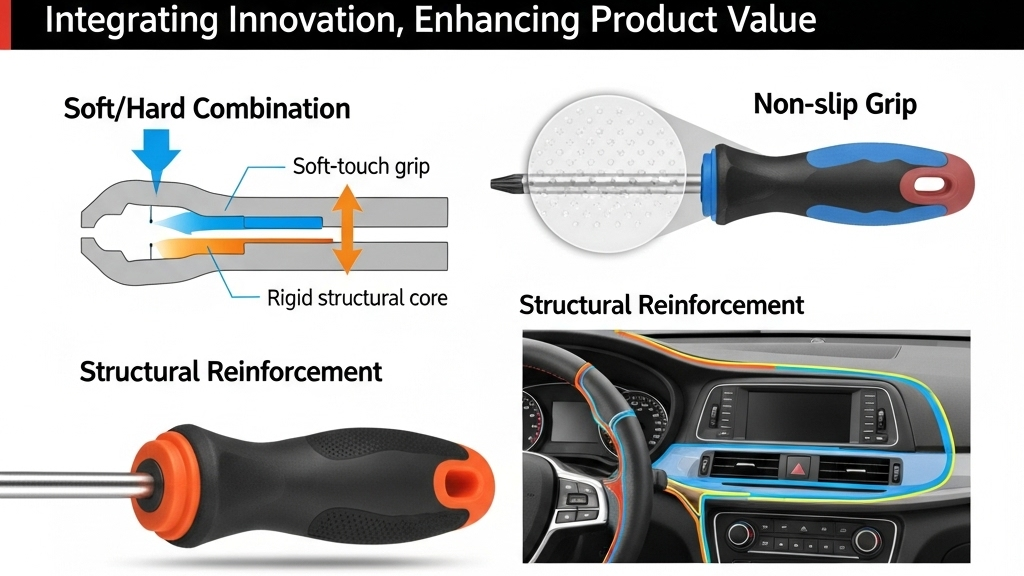
Bonding failures in overmolding are often due to polarity mismatch, insufficient preheating, or mold contamination. Especially in multi-material systems, strong adhesion requires both compatible materials and strict process control. Unstable bonding directly impacts product lifespan and reliability.
- Material Compatibility: Select material pairs with matched polarity.
- Surface Treatment Techniques: Use plasma, flame, or chemical treatment for better adhesion.
- Temperature Management: Ensure proper melt fusion of core and overmold layers.
- Mold Cleanliness Control: Prevent impurities at the bonding interface.
How Do Injection Settings Impact Overmolding?
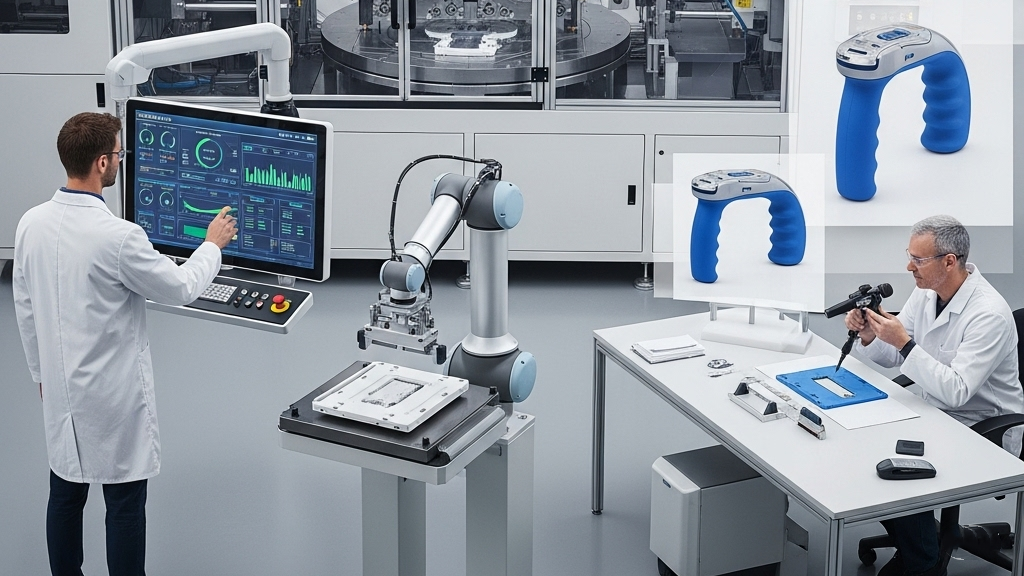
Controlling temperature, pressure, and cooling time is vital for overmolding integrity. Improper settings can cause delamination, warping, or voids, affecting product quality. Precise tuning of process windows determines bonding reliability.
- Mold Temperature Strategy: Maintain ideal adhesion temperature range.
- Pressure Optimization: Prevent material overflow or internal stress.
- Cooling Ratio: Ensure core is shaped before overmolding.
- Injection Sequence: Prioritize key bonding areas.
How Does Mold Design Influence Bonding Accuracy?
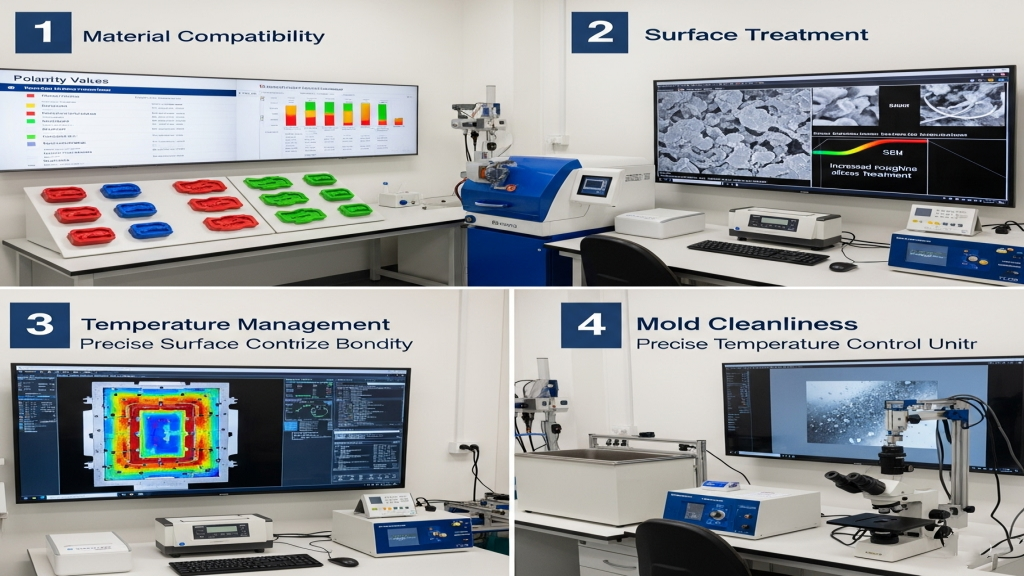
Mold design dictates the precision and bonding success of overmolded products. Misalignment or incomplete overmolding often results from poor parting or venting design. A high-quality overmold tool must address positioning, sealing, and balanced flow.
- Precision Alignment: Prevent misalignment between materials.
- Air Venting: Eliminate bubbles during overmolding.
- Balanced Flow Design: Ensure uniform material distribution.
- Surface Texturing: Increase bonding surface friction.
Bonding Performance Comparison of Common Overmolding Materials
Material Pair |
Surface Treatment |
Bond Strength |
Temp Diff |
Cost |
Mold Complexity |
Application |
TPE + PC | No | High | Medium | Medium | Medium | Medical devices |
TPU + ABS | Yes | Medium-High | Medium | Medium | Medium | Power tools |
TPE + PP | Yes | Medium | Low | Low | Simple | Appliance housings |
LSR + PA | No (requires special design) | High | High | High | High | Auto seals |
Extended Applications
Overmolding is not just about soft-over-hard; it enables multi-color molding, shock absorption, and function integration. Designers can combine ergonomics, protection, and aesthetics in a single piece. Innovative geometry and multi-materials make overmolding a pivotal tech for future development.
1.Structural Overlay: Improves product durability via single-shot molding.
2.Function Integration: Combines soft grip, waterproof, anti-slip features.
3.Brand Differentiation: Dual-color molding delivers visual identity.
4.Simplified Assembly: Reduces gluing and assembly processes.
Conclusion
Overmolding is becoming indispensable in precision molding, offering both enhanced functionality and aesthetics. Success lies in precise coordination of materials, parameters, and mold structure. Only a systematic optimization approach enables manufacturers to stand out in a competitive market.
For expert assistance in implementing for your production needs, visit our resource center or contact us. Let’s help you scale up your manufacturing with precision and efficiency!
Post time: Jul-11-2025