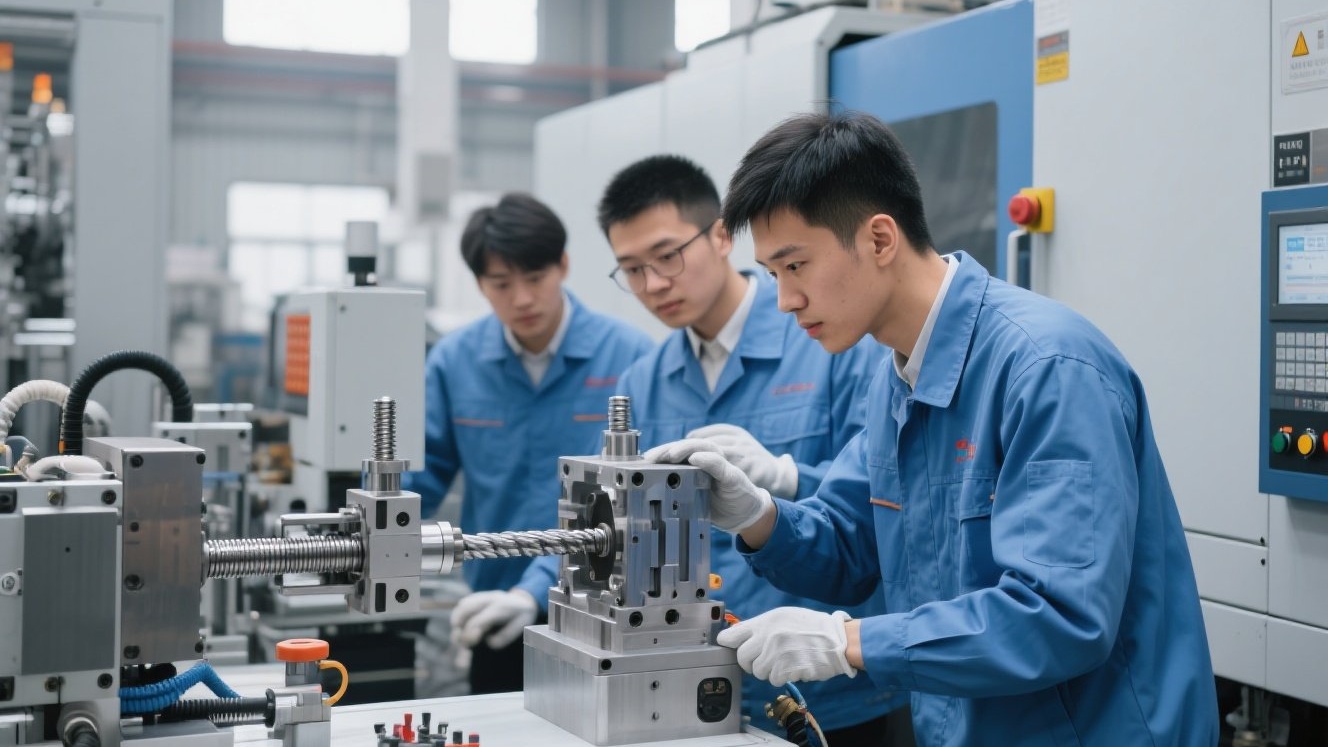
ABS sheets are attracting much attention due to their wide range of applications. However, overheating and decomposition during injection molding are critical issues that affect product quality. Excessive melt temperature can damage the ABS molecular structure, reduce performance, and generate harmful gases. Therefore, effectively preventing overheating is crucial for high-quality injection molding production. This article will explore multiple aspects, from materials to equipment, aiming to provide professional guidance on avoiding overheating and decomposition of ABS sheets.
Avoiding ABS overheating and decomposition is not solely dependent on controlling a single step but is the result of multiple factors working together. To systematically address this issue, we will delve into the key process parameters that affect melt temperature. This includes the temperature control of the injection molding machine, screw speed, injection pressure and speed, as well as holding pressure and cooling. By meticulously analyzing these core steps, we can develop more precise prevention strategies.
What key thermal properties of ABS need to be considered during injection molding?
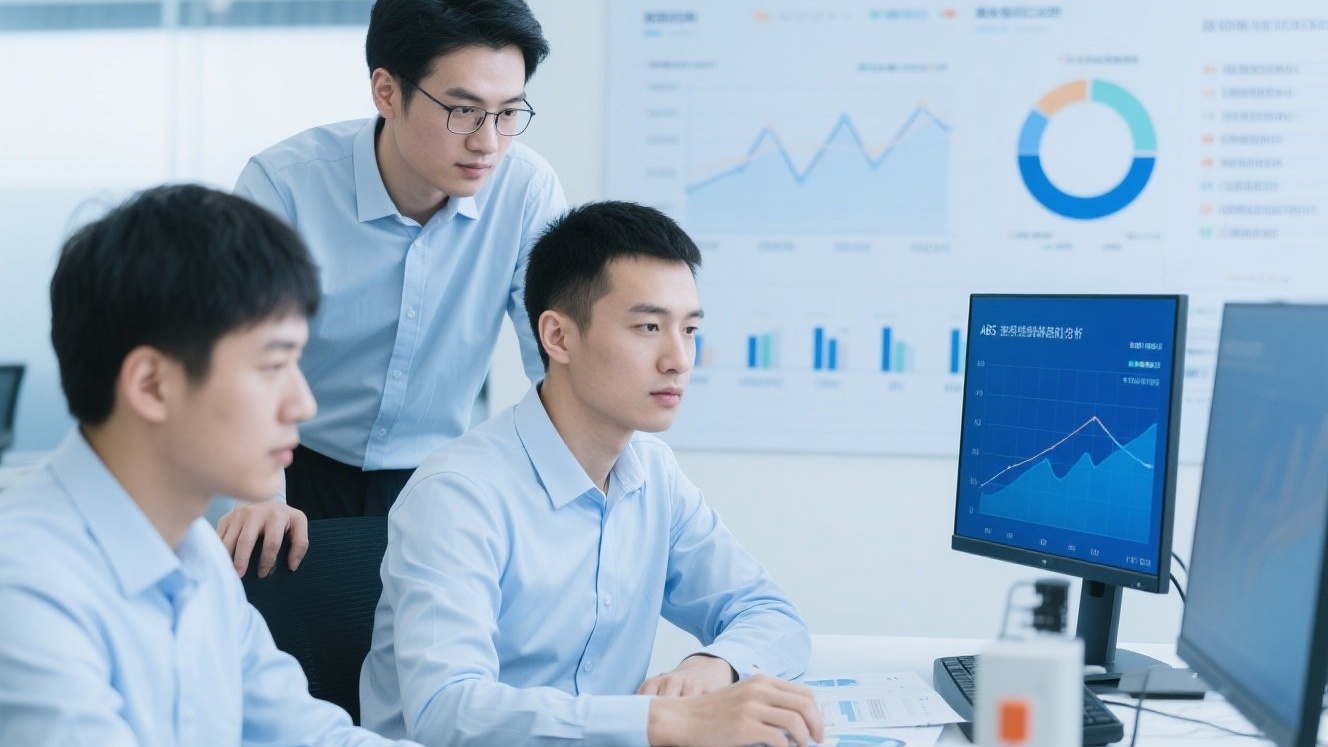
As an amorphous polymer, the molecular chain structure of ABS resin makes it exhibit a certain sensitivity to heat. Understanding these inherent thermal properties is the primary prerequisite for formulating reasonable injection molding processes and avoiding material degradation.
- Thermal Decomposition Sensitivity: The unsaturated bonds in ABS resin make it susceptible to decomposition at high temperatures, affecting product quality and generating harmful substances.
- Thermal Stability Differences: The thermal stability of different grades of ABS varies, and flame retardant grades may be more sensitive to heat.
- Shear Heat Generation: High shear during the injection molding process can cause frictional heat in the ABS melt, leading to localized overheating.
- Low Thermal Conductivity: ABS has poor thermal conductivity, making it difficult to dissipate heat and prone to localized overheating.
What parameter controls are crucial to avoid ABS overheating and decomposition?
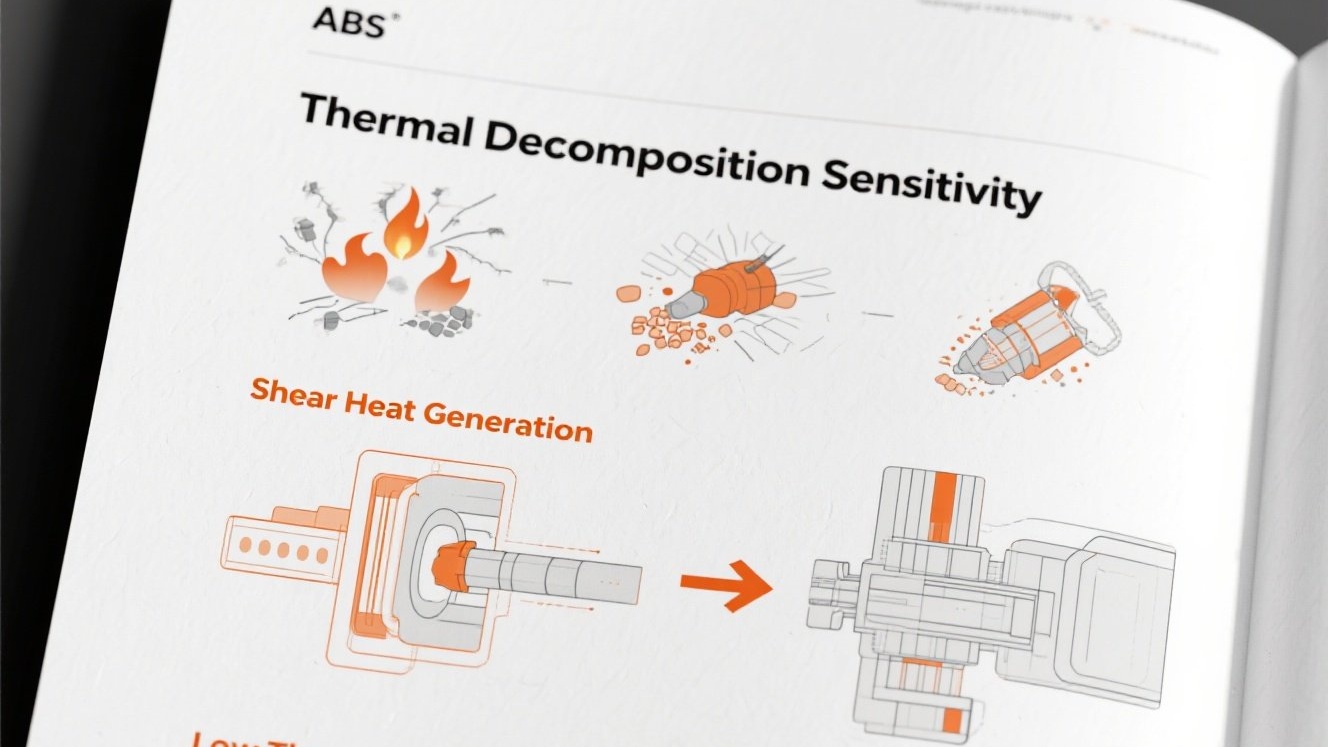
Precisely setting injection molding process parameters is a critical step in preventing ABS overheating and decomposition. Reasonable control of temperature, pressure, and speed can ensure that ABS remains in a safe and stable state during melting, injection, and cooling, thereby ensuring the quality of the final product.
- Melt Temperature Control: Accurately set the temperature of each zone of the barrel within the recommended range to avoid overheating caused by prolonged high-temperature dwell and poor plasticization.
- Injection Speed Control: Reasonably control the injection speed, especially avoiding excessive speeds, to reduce shear heat generation during melt flow.
- Injection and Holding Pressure Control: Avoid excessive injection and holding pressures to reduce shear stress and high-temperature dwell time.
- Screw Speed and Back Pressure Control: Moderately adjust the screw speed and back pressure to prevent excessive shear heat generation and prolonged melt dwell time in the barrel.
How do mold design and equipment maintenance affect the risk of ABS overheating?
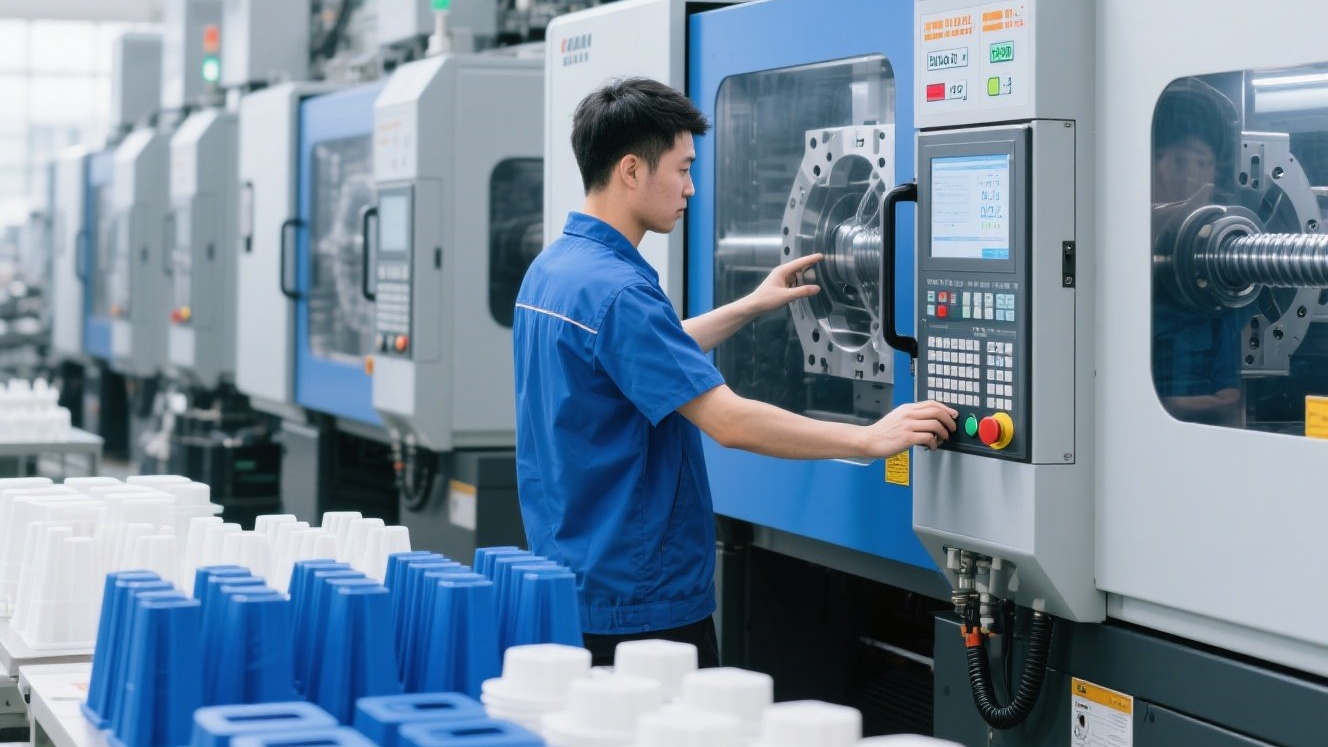
Proper mold design is directly related to the flow state and heat dissipation efficiency of the ABS melt. Inappropriate design can easily cause local stagnation and heat accumulation. At the same time, good maintenance of injection molding equipment is a key guarantee for ensuring stable execution of process parameters and avoiding accidental overheating.
- Unreasonable Runner and Gate Design: Poor runner and gate design can increase melt flow resistance, leading to shear heat generation and stagnation overheating.
- Inefficient Cooling System: Inefficient mold cooling extends the dwell time of ABS at high temperatures, increasing the risk of overheating and decomposition.
- Injection Molding Machine Temperature Control System Failure: Failure of the temperature control system can lead to uncontrolled barrel temperature, directly causing ABS overheating and decomposition.
- Screw and Barrel Wear: Worn screws and barrels can affect plasticization uniformity, increase shear heat, and potentially introduce impurities that accelerate decomposition.
Anti-overheating decomposition measures
Category |
Key Parameter/Factor |
Potential Overheating/Decomposition Risk |
Measures to Avoid Overheating/Decomposition |
Material Properties | Thermal Decomposition Temperature,Thermal Stability,Thermal Conductivity | Easy Decomposition at High Temperature,Different Grades Have Varying Stability,Local Heat Accumulation | Choose Suitable ABS Grade,Understand its Thermal Performance Parameters;Avoid Prolonged High-Temperature Processing;Pay Attention to Thick-Walled Part Process Adjustments. |
Process Parameters | Barrel Temperature (Zones) | Overall Overheating Decomposition if Too High,Plasticization Issues Leading to Shear Overheating if Too Low | Precisely Set Each Zone Temperature Within the Recommended Range;Monitor Actual Melt Temperature. |
Injection Speed | Shear Heat Generation,Local Overheating Decomposition if Too High | Employ Multi-Stage Injection Speed Control,Reduce High-Speed Injection Ratio. | |
Injection Pressure/Holding Pressure | Increased Shear Stress,Prolonged High-Temperature Residence Time if Too High | Optimize Pressure Profile,Avoid Unnecessarily High Pressure and Prolonged Holding Time. | |
Screw Speed/Back Pressure | Increased Shear Heat Generation and High-Temperature Residence Time if Too High | Use Appropriate Screw Speed and Back Pressure,Avoid Excessive Shearing. | |
Melt Residence Time in Barrel | Increased Thermal Decomposition Risk if Too Long | Optimize Injection Cycle,Reduce Melt Residence Time in High-Temperature Zones;Adopt First-In,First-Out Principle. | |
Mold Design | Runner and Gate Design | High Flow Resistance,Shear Heat Generation,Stagnation Overheating | Optimize Runner and Gate Design,Reduce Flow Resistance,Avoid Dead Ends. |
Cooling System Design | Low Cooling Efficiency,Slow Heat Dissipation,Local Overheating | Optimize Cooling Channel Design,Ensure Uniform and Efficient Cooling. | |
Equipment Maintenance | Temperature Control System | Malfunction Leads to Excessive or Fluctuating Temperatures,Causing Overheating Decomposition | Regularly Inspect and Maintain the Temperature Control System to Ensure Accuracy and Reliability. |
Screw and Barrel Wear | Poor Plasticization,Increased Shear,Contamination Accelerates Decomposition | Regularly Inspect and Maintain the Screw and Barrel,Replace Worn Parts Promptly. |
Other measures to prevent ABS overheating and decomposition.
Adopting appropriate auxiliary measures and additives is also an important means to enhance the resistance of ABS to overheating and decomposition. These methods can start from the perspective of material modification to further enhance the stability of ABS under high temperature and shear conditions, providing additional guarantees for high-quality injection molding production.
1.Antioxidants: Adding antioxidants can inhibit high-temperature oxidation of ABS and delay thermal degradation.
2.Heat Stabilizers: Using heat stabilizers can combine with the active sites of ABS to prevent degradation reactions.
3.Lubricants: Adding lubricants can reduce melt viscosity and reduce frictional heat generation.
4.Functional Additives: Some additives can improve thermal conductivity or provide a physical barrier, assisting in anti-overheating.
Conclusion
Preventing overheating and decomposition in ABS sheet injection molding requires multi-faceted coordinated control. Understanding the heat sensitivity of ABS is fundamental, and precisely adjusting process parameters such as temperature, pressure, and speed is crucial. Optimizing mold design and maintaining equipment can reduce risks from a hardware perspective.
For expert assistance in implementing for your production needs, visit our resource center or contact us. Let’s help you scale up your manufacturing with precision and efficiency!
Post time: May-19-2025