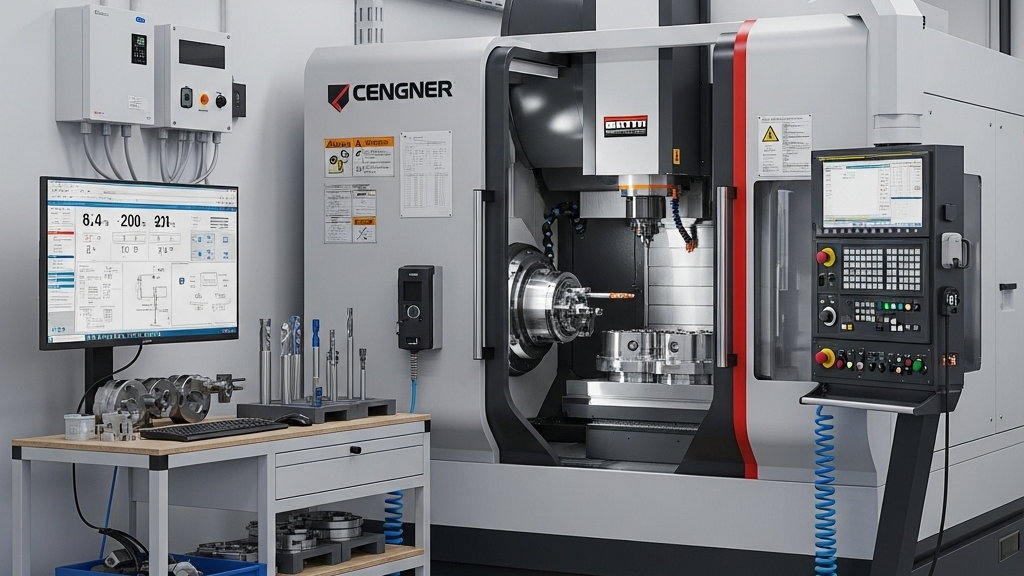
In the field of precision instruments, CNC machining of carbon steel components requires extremely high standards, especially when it comes to stability. To ensure the accuracy and stability of each component during the machining process, proper operational procedures and equipment selection are indispensable. Modern CNC machining technology provides powerful support for the efficient processing of carbon steel components, but maintaining stability remains a key focus for every manufacturer.
As the market’s demand for precision continues to increase, how to effectively enhance stability during the machining process and reduce errors has become a critical issue. By introducing advanced detection technology and automated control systems, the stability of CNC machining has been further improved.
How to Improve CNC Machining Precision?
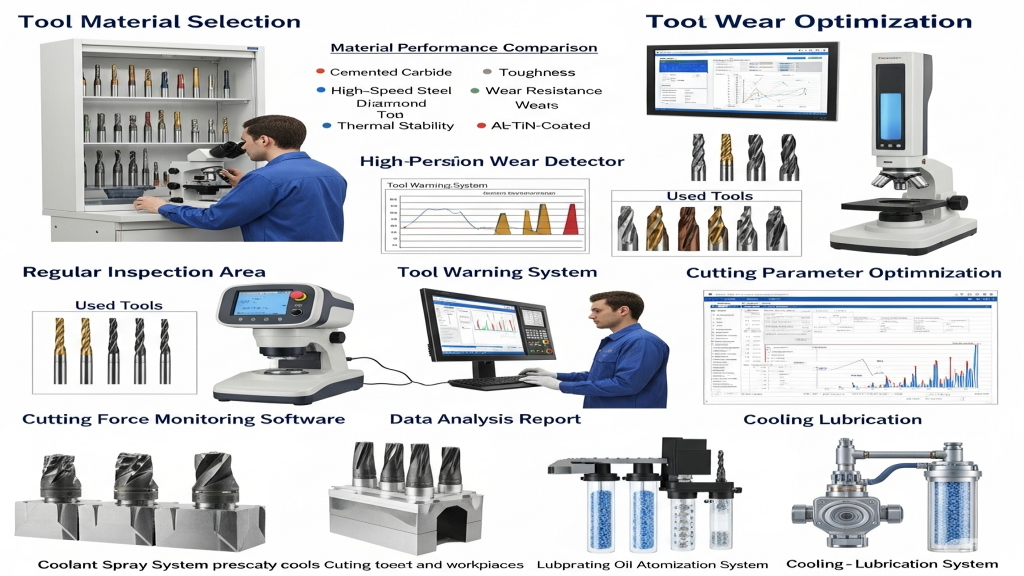
CNC machining precision directly impacts the quality of carbon steel components. By selecting the right tools, adjusting machining parameters, and controlling environmental variables, precision can be effectively improved. High-precision machining not only reduces waste but also improves production efficiency.
- Tool selection: The material and shape of the tool are critical to precision.
- Environmental control: Temperature and humidity control can minimize thermal expansion errors.
- Cutting parameters: Proper cutting parameters ensure machining stability.
- Machine performance: High-precision CNC machines provide more stable machining conditions.
How to Prevent Thermal Deformation in CNC Machining?
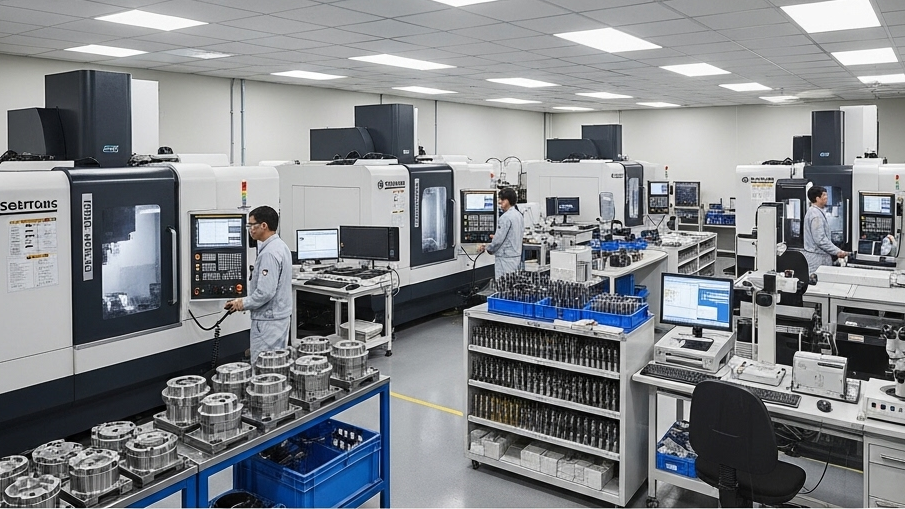
Thermal deformation is an important factor affecting CNC machining precision, especially in the processing of carbon steel materials. By optimizing the cooling system and using efficient cutting fluids, thermal deformation errors can be minimized.
- Coolant use: Using efficient cutting fluids helps to lower temperature fluctuations during machining.
- Machining speed control: Properly reducing machining speed helps reduce heat accumulation.
- Cutting force optimization: Controlling cutting force reduces heat load.
- Tool material selection: Using heat-resistant tool materials reduces the impact of temperature changes on machining precision.
How to Optimize Tool Wear in CNC Machining?
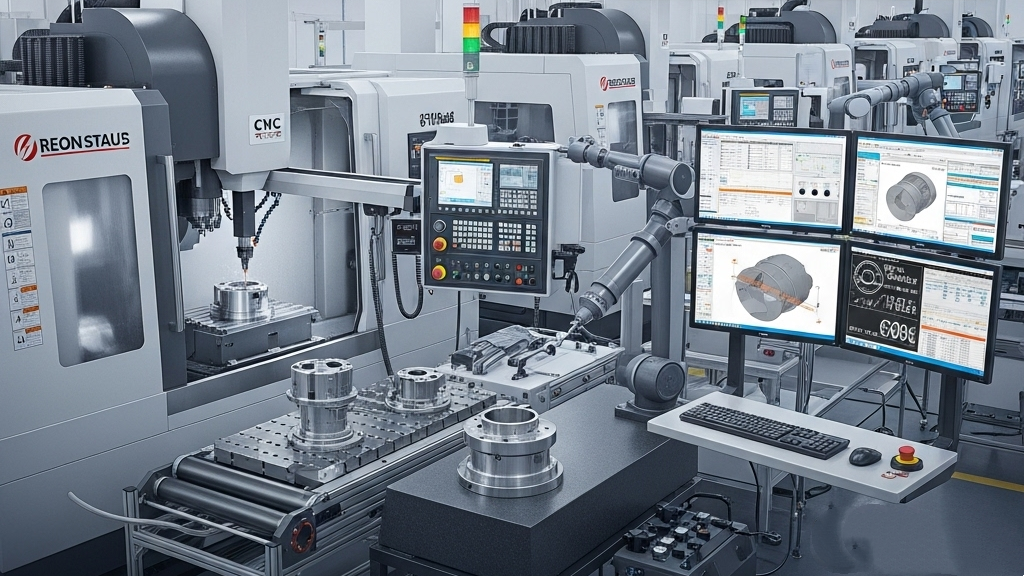
Tool wear directly impacts CNC machining stability and precision. Wear not only causes poor surface quality but can also damage the equipment. Proper tool management and wear monitoring systems can effectively extend tool life.
- Tool material selection: Wear-resistant materials reduce tool wear.
- Regular tool inspection: Regularly inspect tools for wear and replace damaged ones in time.
- Cutting parameter optimization: Adjusting cutting speed and feed rate reduces tool wear.
- Cooling and lubrication: Adequate cooling and lubrication can slow down tool wear.
Comparison of Tool and Machine Selection in CNC Machining
Feature |
Carbide Tools |
HSS Tools |
Machine Stability |
Cutting Efficiency |
Tool Durability | High | Medium | High | Medium |
Cutting Precision | High | Medium | High | High |
Machining Speed | High | Moderate | High | High |
Cost | High | Low | High | Medium |
CNC Machining Stability Optimization Plan
By using advanced technologies and proper management methods, CNC machining stability can be significantly improved. Implementing a variety of measures will provide more efficient and precise solutions for carbon steel component machining.
1.Optimize machining environment: Control temperature and humidity and stabilize equipment.
2.Tool management: Regularly inspect tool status and adjust cutting parameters promptly.
3.Choose high-precision equipment: Use high-precision CNC equipment to ensure machining accuracy.
4.Adopt advanced cooling systems: Minimize thermal deformation with effective cooling systems.
Conclusion
Improving CNC machining stability, especially in the processing of carbon steel components for precision instruments, is crucial. By using proper technologies and management methods, machining accuracy can be greatly improved, ensuring stability throughout the production process. In the future, precision machining technologies will continue to advance towards greater accuracy and stability.
For expert assistance in implementing for your production needs, visit our resource center or contact us. Let’s help you scale up your manufacturing with precision and efficiency!
Post time: Jun-25-2025