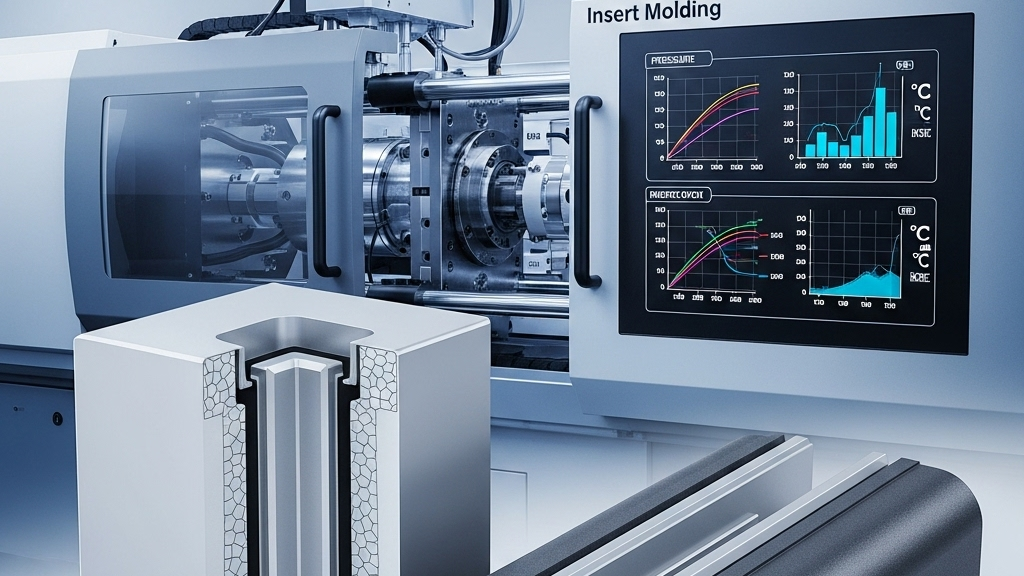
Insert molding is a process where metal or other non-plastic materials are embedded into plastic parts. By properly controlling injection molding parameters, we can ensure strong bonding and high precision between the insert and plastic material. Optimized insert molding technology not only improves product performance but also reduces production costs, which is crucial for modern manufacturing.
How to ensure strong bonding between inserts and plastics?
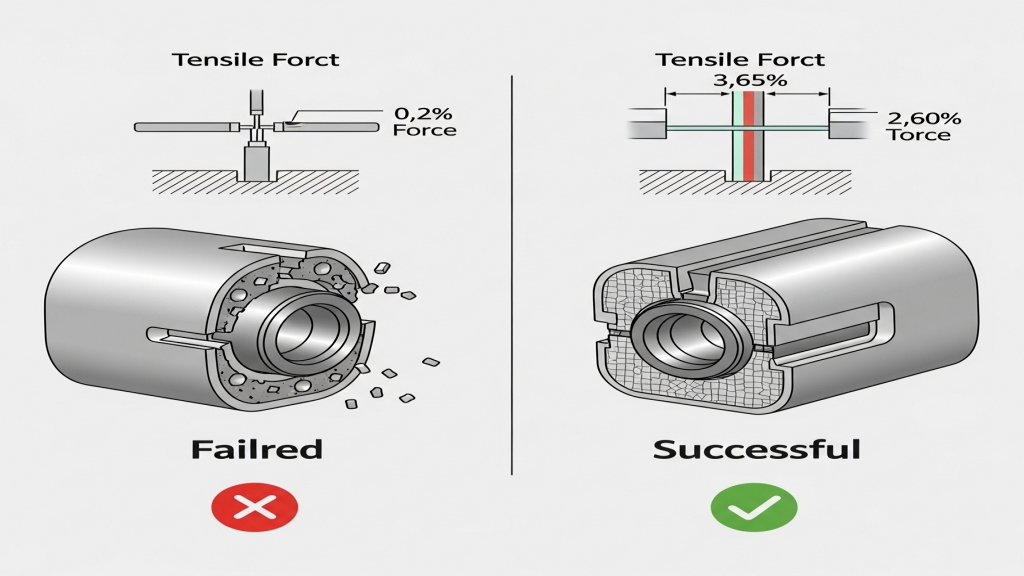
The strength of bonding between inserts and plastics primarily depends on the surface treatment of the insert and the temperature and pressure control during the molding process. By applying appropriate surface treatments to the insert, the adhesion between the insert and plastic can be increased.
- Surface treatment: Techniques such as sandblasting and electroplating can increase the surface roughness, improving adhesion.
- Temperature control: Learn how to optimize temperature control.
- Injection pressure control: Adjusting injection pressure can effectively prevent insert movement or displacement.
- Appropriate mold design: Designing the mold shape properly can ensure a more secure bond between the insert and plastic.
How to ensure precision in insert molding?
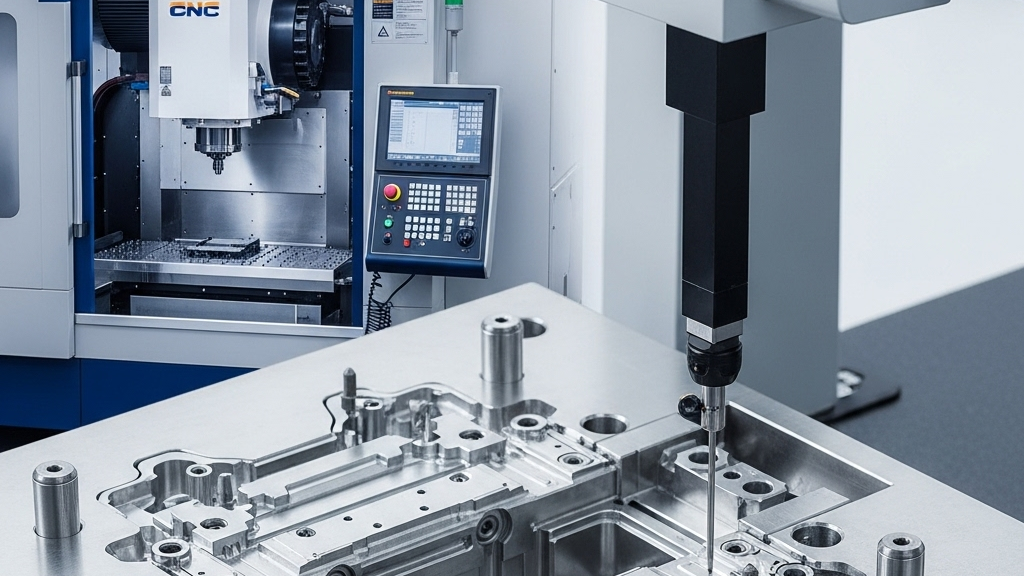
Precision control is essential for insert molding, especially in precision products. By strictly controlling various parameters during the injection molding process, we can ensure the proper placement and dimensional accuracy of the insert in the plastic part.
- Mold precision: Using high-precision mold manufacturing techniques can ensure product dimensional stability.
- Injection speed control: Learn how to control injection speed.
- Optimizing holding time: Appropriate holding time can effectively prevent dimensional fluctuations.
- Cooling system design: Optimizing the cooling system can prevent deformation caused by uneven cooling.
How to improve the production efficiency of insert molding?
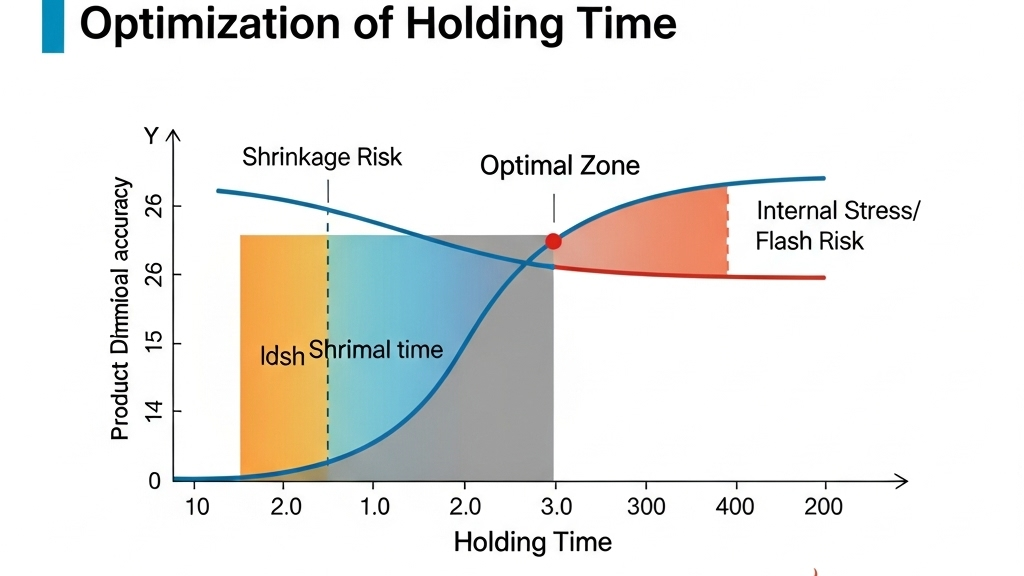
The production efficiency of insert molding directly impacts production costs. By optimizing production processes and reducing unnecessary downtime, overall production efficiency can be improved.
- Increased automation: Automated equipment can reduce manual intervention and improve production efficiency.
- Mold temperature control system: Learn how to optimize mold temperature control.
- Multi-cavity design: Multi-cavity mold design allows multiple products to be produced in one cycle, improving production efficiency.
- Quick-change systems: Quick-change mold systems can significantly reduce mold changeover time.
Comparison of Key Points for Insert Molding Technology
Key Technical Points |
Surface Treatment |
Temperature Control |
Injection Pressure |
Cooling System |
Influencing Factors | Insert adhesion | Material flow | Insert stability | Product dimensional stability |
Optimization Methods | Sandblasting, electroplating | Precise temperature control | Precise pressure adjustment | Uniform cooling |
Applicable Scenarios | Various metal inserts | Plastic part injection | High-precision insert molding | Precision products |
Production Efficiency | Medium | High | High | High |
How to choose suitable insert materials and design?
Choosing suitable insert materials and design solutions can significantly enhance product quality and production efficiency.
- Select appropriate insert materials: For example, the choice of metal inserts should consider chemical compatibility with plastics.
- Optimize insert design: The shape of the insert should match the mold design to ensure no displacement during the molding process.
Conclusion
Ensuring the strength and precision of insert molding requires proper control of various technical factors. By optimizing surface treatments, injection parameters, and mold designs, product quality and production efficiency can be greatly enhanced. Achieving precise and efficient insert molding processes is crucial for modern manufacturing.
For expert assistance in implementing for your production needs, visit our resource center or contact us. Let’s help you scale up your manufacturing with precision and efficiency!
Post time: Jul-01-2025