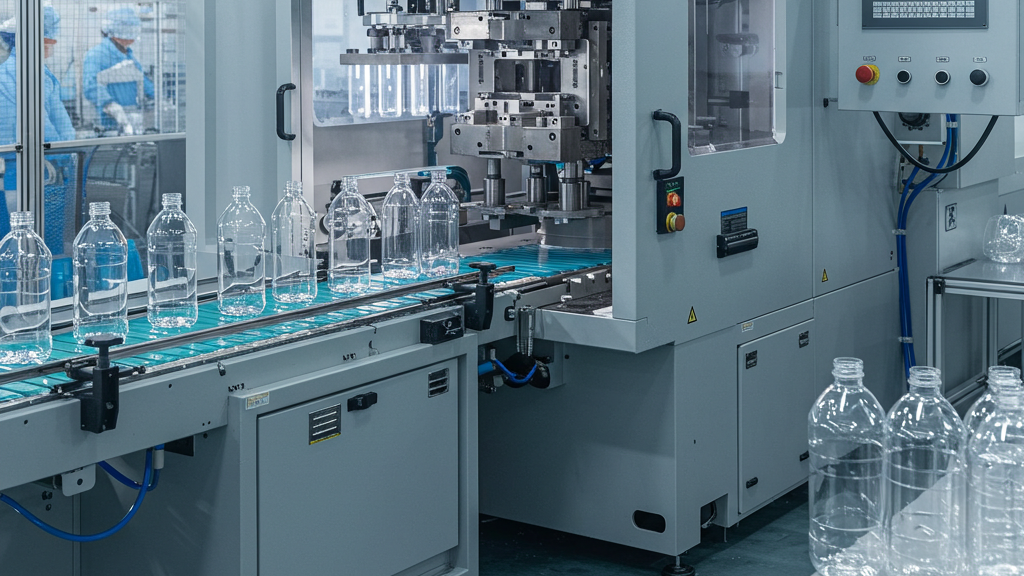
Polycarbonate containers are widely used for their excellent performance, but their core value lies in reliable sealing. Seal failure not only affects the product but also damages brand reputation. Ensuring a perfect seal is a systematic project, especially dependent on high-precision manufacturing processes. This article will professionally explore how to comprehensively ensure the sealing performance of polycarbonate containers.
Sealing performance largely depends on the manufacturing process, especially advanced blow molding technology. The blow molding process directly affects the precision of the container’s mouth, which is related to the tightness of the lid fit. Therefore, choosing a professional blow molding technology partner is crucial. Next, we will deeply analyze the key technical details of sealing blow-molded polycarbonate containers.
How do Design and Materials Affect Sealing?
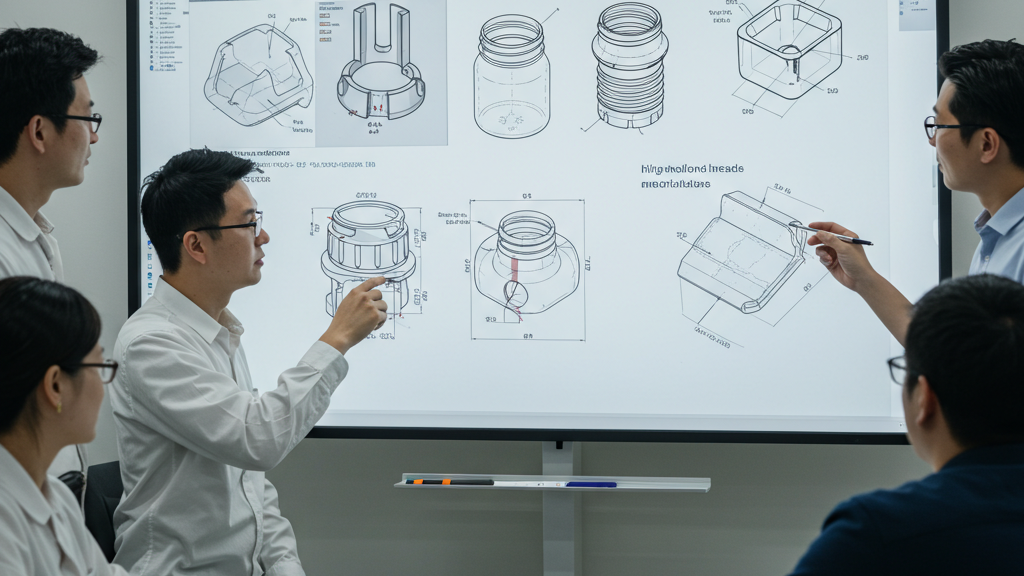
In the initial stages of a polycarbonate container’s lifecycle, namely during design and material selection, the foundation for its future reliable sealing is subtly established. Carefully considered structural design and precisely matched material properties are indispensable cornerstones for building a robust sealing defense.
- Mouth and Neck Design: Meticulously design the container’s mouth and thread shape and dimensions to ensure a precise fit with the lid, forming an effective seal.
- Material Property Considerations: Fully utilize the advantageous properties of polycarbonate and address potential seal-impacting factors like creep through structural design.
- Material Compatibility: Select a polycarbonate grade chemically compatible with the contents and lid material, avoiding interactions that could compromise the seal.
- Dimensional Accuracy and Tolerances: Set reasonable dimensional tolerances in the design to ensure that manufactured containers meet the precise dimensional requirements for sealing.
How Does Blow Molding Process Ensure Sealing?
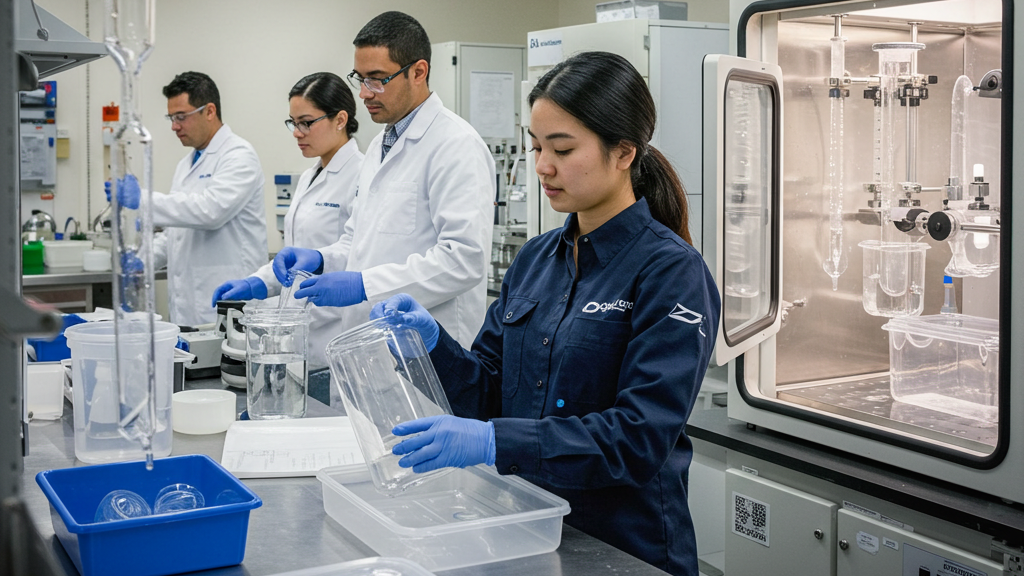
In the manufacturing stage of polycarbonate containers, the blow molding process plays a crucial role in the final sealing performance. From the plasticization of raw materials to the formation of the parison, and then to the blow molding and cooling, each critical control point in the process directly affects the molding accuracy of the container’s mouth and the integrity of the sealing structure.
- Parison Quality: Ensuring that the parison forming the container’s mouth has uniform thickness and consistent temperature is the foundation for sealing accuracy.
- Mold Precision: Relying on high-precision mold design and neck inserts ensures the accurate formation of the container’s mouth shape and threads.
- Process Parameter Control: Precisely controlling the blow molding pressure, speed, and time allows the material to fully conform to the mold, forming a well-defined sealing structure.
- Cooling Process: Properly controlling the cooling rate and temperature in the neck area ensures dimensional stability and prevents deformation of the sealing area.
How is Sealing Performance Subjected to Quality Control and Testing?
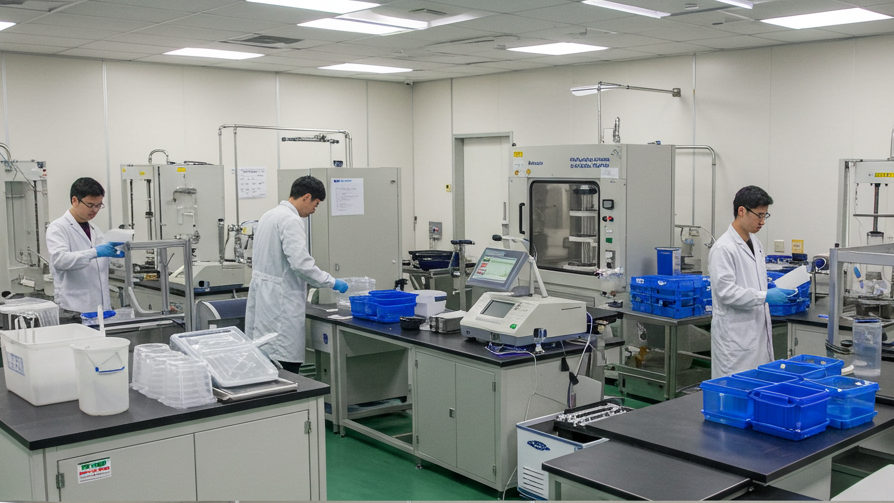
Even if design and production processes are extremely rigorous, the final product’s sealing performance still needs to be confirmed through systematic quality control and verification. Scientific and effective testing methods are the last critical line of defense in evaluating whether a polycarbonate container can provide long-term reliable sealing.
- Dimensional Accuracy Testing: Precisely measure key dimensions of the container’s mouth and perform statistical control to ensure compliance with design requirements.
- Non-Destructive Leak Testing: Employ pressure, vacuum, or submersion methods for rapid leak detection to screen out sealing defects.
- Closure Fit Testing: Evaluate the torque applied to the lid and the resulting sealing force to ensure good fit between the lid and the container mouth.
- Environmental and Aging Testing: Conduct high and low temperature, drop, and accelerated aging tests to verify long-term sealing reliability.
From design to testing
Key Stage/Aspect for Ensuring Sealing |
Key Focus |
Design and Material Selection | Precise neck finish structure design and selection of suitable material compatibility. |
Blow Molding Process Control | Controlling mold accuracy, parison quality, and key process parameters (e.g., cooling). |
Quality Detection and Verification | Performing critical dimension inspection and sealing tests simulating actual conditions. |
Troubleshooting and Continuous Optimization | Systematically analyzing sealing failure causes and continuously improving design and process. |
Diagnosing and Optimizing Sealing Issues
Whether it involves adjusting the mold, refining process parameters, or improving material formulations, this continuous cycle of problem-solving and performance optimization is the ultimate guarantee for the long-term reliable sealing of polycarbonate containers.
1.Root Cause Analysis: Conduct an in-depth analysis of sealing failure patterns and root causes to precisely pinpoint the issue.
2.Physical Inspection: Perform a detailed inspection of the container mouth and lid, looking for physical defects and dimensional deviations.
3.Process Tuning: Analyze and adjust molding process parameters to eliminate instability during production.
4.Design and Material Optimization: Based on the diagnosis results, improve the container design or replace it with a more suitable material combination.
Conclusion
Ensuring the excellent sealing performance of polycarbonate containers is not a task for a single step but a systematic project throughout the product’s entire life cycle. Only by closely integrating these technical key points with management measures can we ultimately create a truly safe, reliable, and flawless polycarbonate sealing solution, effectively guaranteeing the quality of the contents and winning market trust.
For expert assistance in implementing for your production needs, visit our resource center or contact us. Let’s help you scale up your manufacturing with precision and efficiency!
Post time: May-12-2025