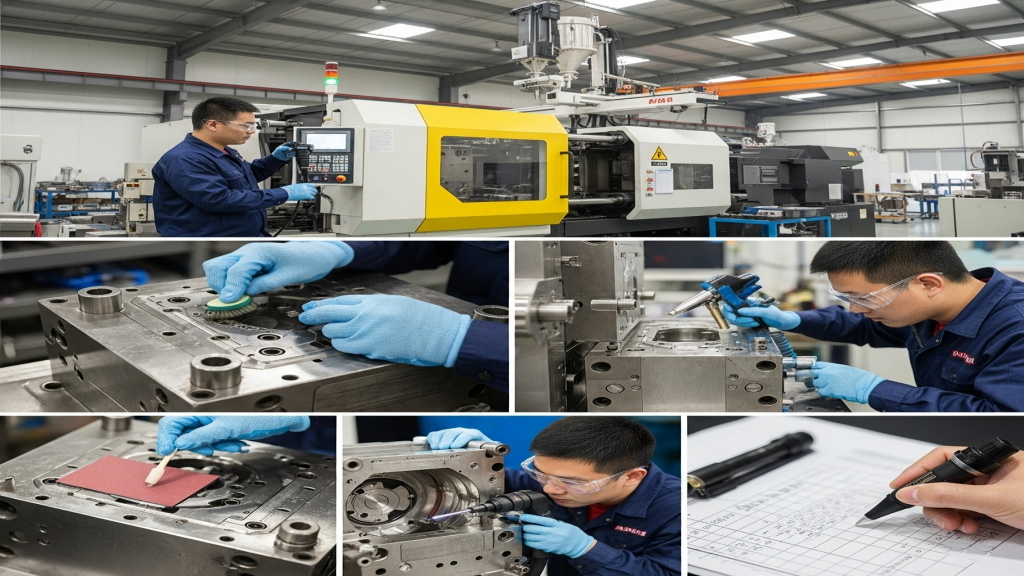
Multi-cavity molds are extremely efficient in injection molding production, but maintaining consistent melt temperature within each cavity is a challenge, especially for heat-sensitive materials like ABS. ABS doesn’t have a strict “melting point”; instead, the focus should be on the viscous flow temperature above its softening point. Subtle differences in melt temperature can lead to issues in product dimensions, performance, and appearance.
Ensuring ABS melt temperature consistency in multi-cavity molds requires systematic consideration. This includes mold design, runner layout, heating and cooling systems, as well as the injection molding machine’s performance and process parameters. Runner balance is crucial, as it ensures that the melt experiences a similar flow history and shear heating before entering each cavity.
How does runner design equalize ABS melt temperature?
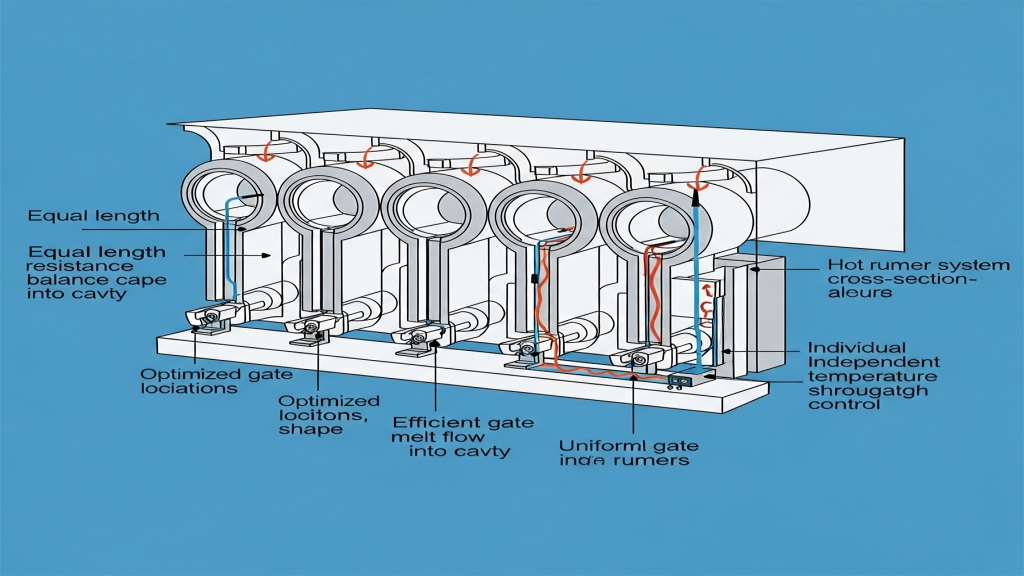
Mold runner design is critical for temperature uniformity of ABS melt in multi-cavity molds. A reasonable runner layout can effectively control the flow behavior of the melt, thereby affecting the shear heating effect generated during the filling process and ensuring a high degree of temperature distribution consistency in each cavity.
- Runner Geometric Balance: By designing runners of equal length or equal resistance, ensure that the melt simultaneously and evenly enters each cavity, thereby maintaining a consistent temperature.
- Runner Cross-Sectional Shape and Size: Optimize the runner cross-section (e.g., round) and size to reduce uneven shear heat and ensure uniform melt temperature distribution.
- Gate Design: Carefully design the gate location, size, and shape to help the melt fill evenly and reduce unnecessary shear heat, thus ensuring a consistent initial temperature in each cavity.
- Hot Runner System Application: Utilize hot runner technology to maintain a constant melt temperature within the runners and ensure the melt enters each cavity at a consistent temperature through independent temperature control.
Which process parameters affect ABS melt temperature consistency?
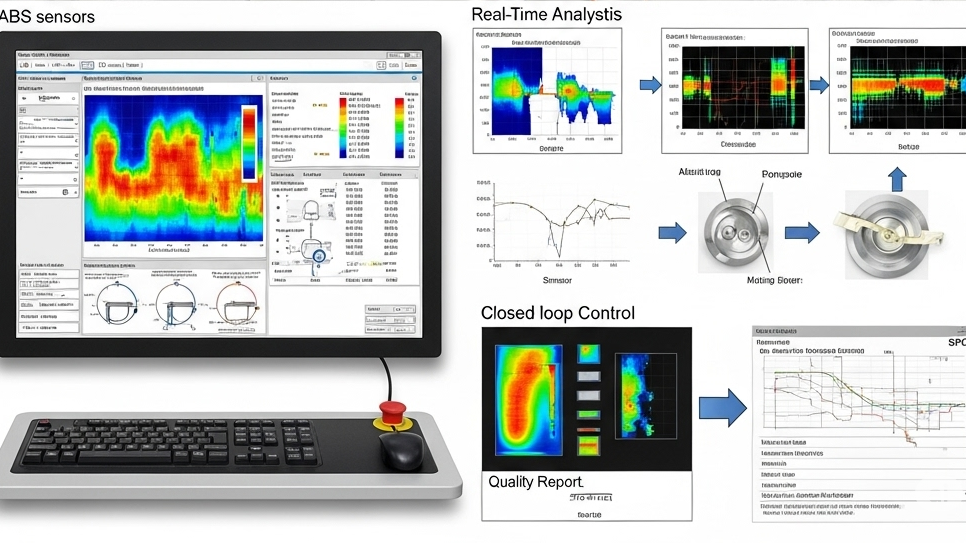
In multi-cavity injection molding, the consistency of ABS melt temperature is deeply affected by several key process parameters. The precise setting and optimization of these parameters directly determine the thermal history of the melt during the plasticization and injection stages, thereby affecting the uniformity of product quality.
- Barrel Temperature Setting: Optimize the barrel temperature settings in each zone to ensure uniform plasticization of ABS and stable melt temperature before entering the runner.
- Screw Speed and Back Pressure: Properly adjust the screw speed and back pressure to control shear heating and promote uniform mixing of the melt.
- Injection Speed and Holding Pressure Profile: Carefully set the injection speed and holding pressure profile to balance the filling of each cavity and reduce temperature differences.
- Cycle Time and Cooling Time: Optimize the cycle time and cooling time to maintain overall thermal balance of the mold and ensure melt temperature stability.
How does the mold temperature control system stabilize ABS melt temperature in each cavity?
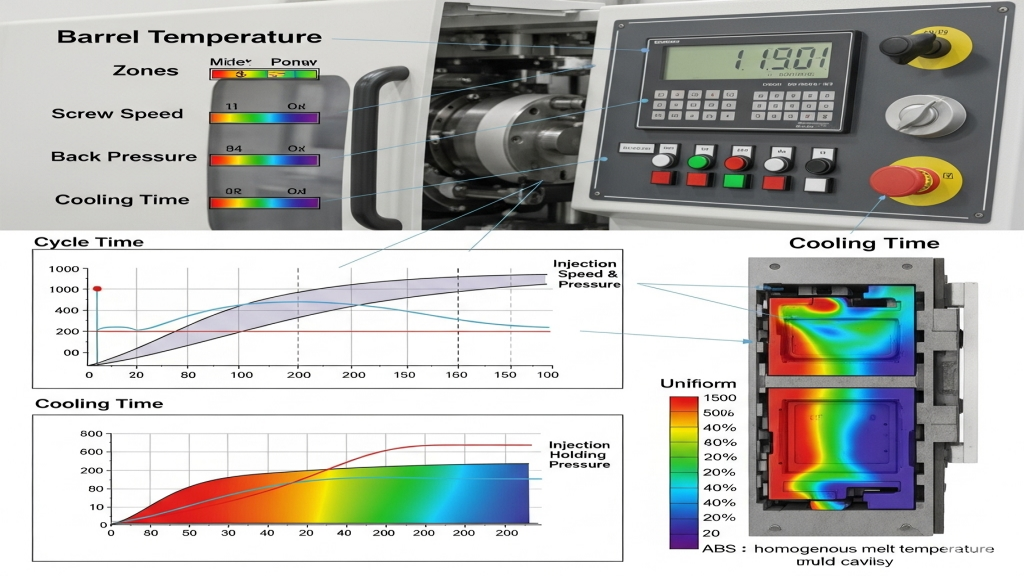
An advanced mold temperature control system is the core to ensure accurate and stable ABS melt temperature in multi-cavity injection molding. These technical measures effectively compensate for the deficiencies of traditional injection molding processes by finely managing the temperature of each mold area, thereby improving the uniformity of product quality.
- Independent Temperature Control Units: Set up independent temperature controls for each cavity or critical area to precisely adjust the temperature and compensate for differences.
- Precise Temperature Control of Hot Runners: The hot runner system is used with independently temperature-controlled nozzles to ensure that the melt enters each cavity at a consistent temperature.
- Optimized Cooling Water Line Design: Improve the cooling water line layout to ensure that heat is evenly dissipated from the mold surface, maintaining stable melt temperature.
- Dynamic Mold Temperature Control: The system can dynamically adjust the mold temperature according to the injection molding stage, more effectively managing the melt temperature gradient.
Key influencing factors
Key Factor | Impact Mechanism | Control Technology/Optimization Strategy |
Mold Runner Design | Uneven melt flow and shear heating | Equal length/resistance runners, optimized gates |
Injection Process Parameters | Varying plasticization quality and filling behavior | Optimized barrel temp, screw speed & back pressure, injection speed |
Mold Temperature Control System | Inconsistent cavity temperature management | Independent temperature control units, high-precision hot runners, optimized cooling |
Online Monitoring & Feedback | Inability to real-time adjust temperature deviation | Sensor monitoring, data analysis, closed-loop automatic control |
Monitoring to ensure ABS melt temperature consistency
In the process of injection molding ABS in multi-cavity molds, it is difficult to cope with dynamic changes in production by relying solely on preset parameters. Establishing an efficient online monitoring and feedback mechanism is essential to ensure the continuous consistency of ABS melt temperature in each cavity, and ultimately ensure the stability and reliability of product quality.
1.Precise Sensor Deployment: Install melt temperature and pressure sensors at key locations to capture real-time melt state data.
2.Real-Time Data Analysis: Through high-speed data acquisition and intelligent algorithms, analyze sensor data in real time and detect anomalies in a timely manner.
3.Closed-Loop Automatic Adjustment: Based on the results of data analysis, the system automatically fine-tunes the injection molding parameters to achieve precise temperature control.
4.SPC and Quality Traceability: Use monitoring data to perform statistical process control and establish a quality traceability system to ensure product quality.
Conclusion
When injection molding ABS products in multi-cavity molds, ensuring the consistency of the melt temperature is a core challenge. This requires collaboration in mold design, injection molding process, advanced temperature control technology, and real-time monitoring. With online monitoring and intelligent feedback, we can adjust and maintain the melt temperature in real-time, ensuring the consistency of product quality. This is the key to enhancing competitiveness and the inevitable path towards intelligent manufacturing.
For expert assistance in implementing for your production needs, visit our resource center or contact us. Let’s help you scale up your manufacturing with precision and efficiency!
Post time: May-21-2025