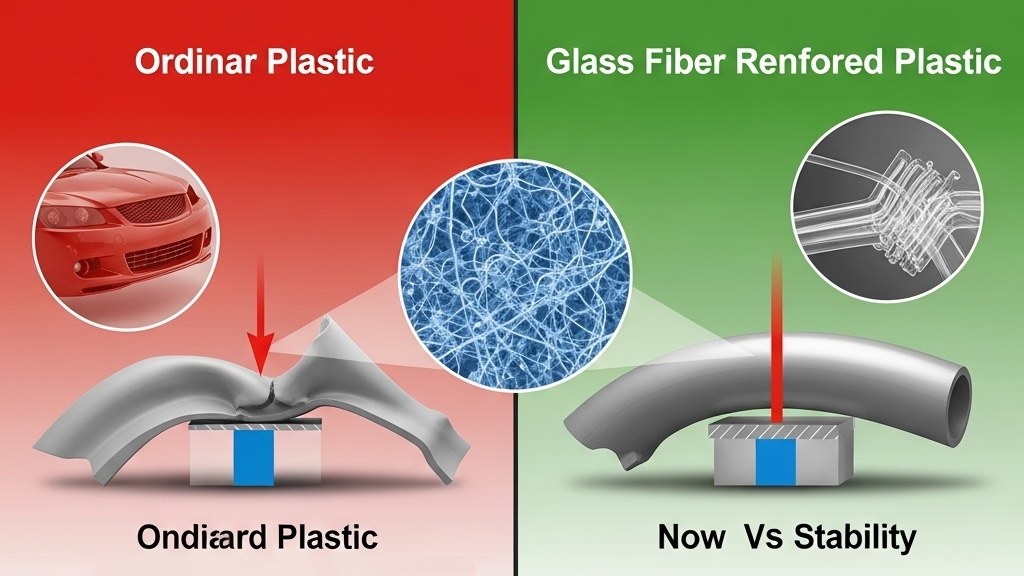
Glass fiber reinforcement is an efficient modification method that significantly enhances dimensional stability and mechanical strength of plastic parts, especially for injection-molded products under long-term load or high temperature. In addition to cost reduction, it also extends product life and ensures consistent performance.
In industries like automotive, electrical, and industrial equipment, glass-fiber-reinforced plastics have gradually replaced metal, becoming key materials for modern lightweight and cost-effective manufacturing. Understanding the reinforcement mechanism is the first step to controlling creep and deformation.
How Does Glass Fiber Improve Creep Resistance?
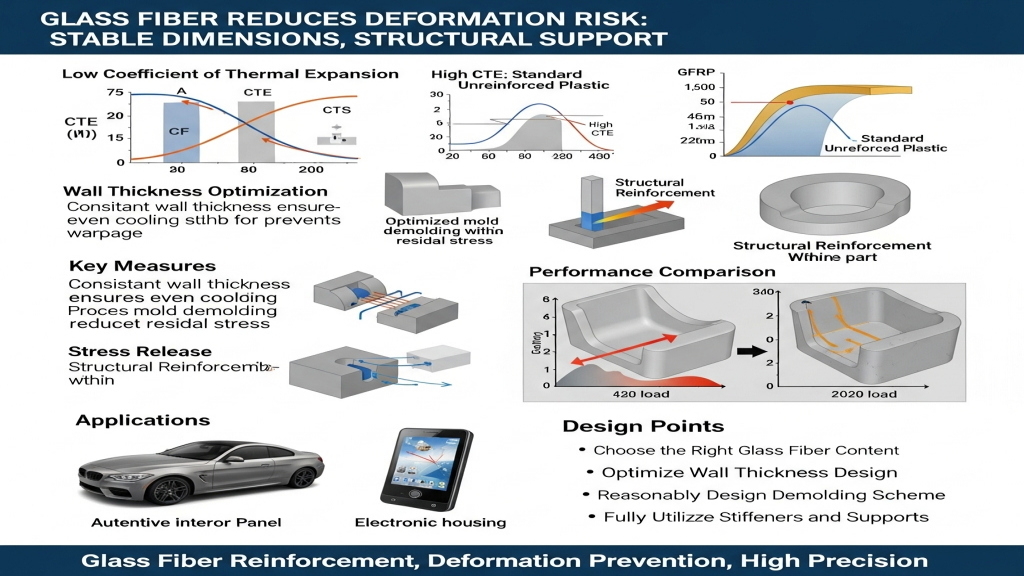
Glass fibers act as a “skeleton” within the molecular structure, restraining polymer chain slippage under long-term loads, effectively reducing creep behavior. Filling rate, fiber length, and orientation are decisive factors in reinforcement performance.
- Filling Ratio Control: A proper glass fiber content is essential for creep resistance.
- Short vs Long Fibers: Short fibers offer uniformity; long fibers provide stronger reinforcement.
- Shear-Induced Orientation: Shear rate influences fiber alignment.
- Directional Design: Optimize fiber alignment according to load direction.
How Does Glass Fiber Minimize Deformation Risks?
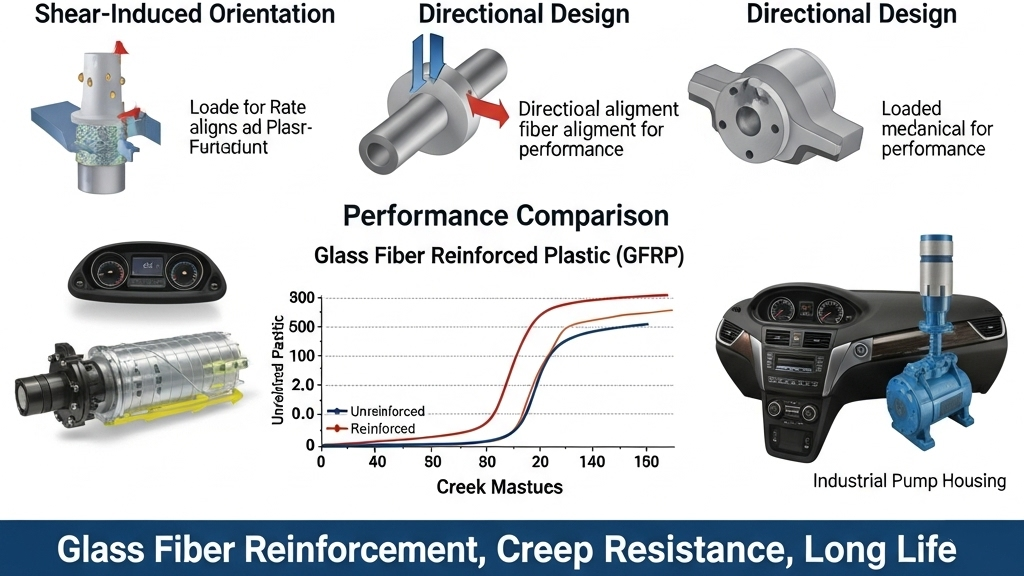
Glass fiber reinforcement significantly reduces the coefficient of thermal expansion and shrinkage, thereby improving dimensional consistency during usage. It plays a crucial structural role in parts subjected to environmental or internal stress.
- Thermal Expansion Control: Glass fibers reduce CTE effectively.
- Wall Thickness Optimization: Minimize uneven cooling by designing uniform wall thickness.
- Stress Release: Mold release design helps reduce residual stresses.
- Structural Reinforcement: Ribs or supports enhance dimensional stability.
Which Processing Parameters Affect Reinforcement Effectiveness?
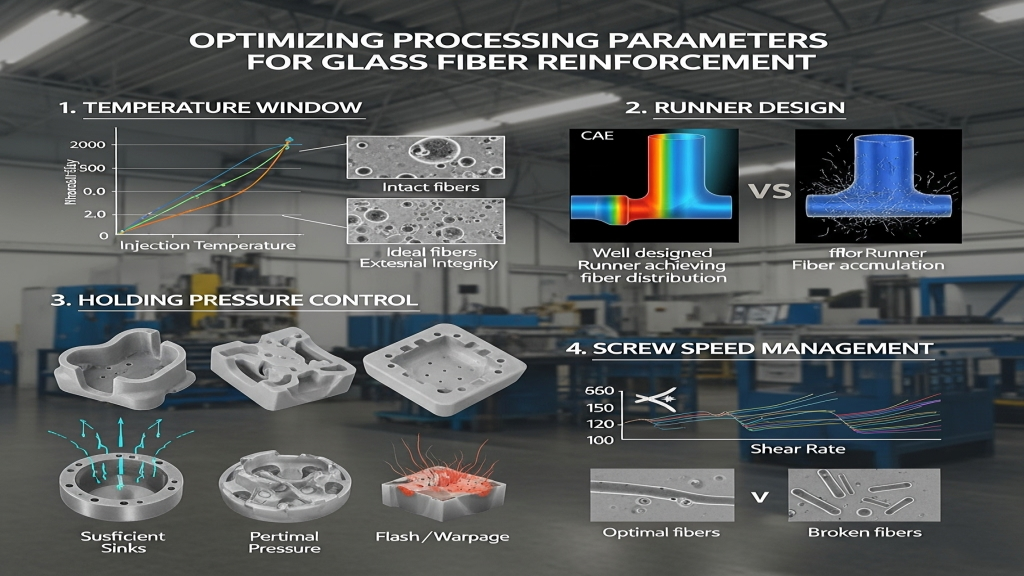
The distribution of glass fibers is highly influenced by processing conditions. Excessive injection temperature, shear rate, or mold pressure can cause fiber breakage or poor dispersion. Controlling the processing window is key to maximizing performance.
- Temperature Window Setup: Prevent thermal degradation of fibers.
- Runner Design: Well-designed runners reduce fiber stagnation or segregation.
- Holding Pressure Control: Optimize balance between pressure and deformation.
- Screw Speed Management: Maintain fiber integrity through controlled shear.
Impact of Glass Fiber Content on Injection Performance
Property |
No Fiber |
10% GF |
30% GF |
50% GF |
Creep Resistance | Poor | Fair | Good | Excellent |
Dimensional Stability | Low | Medium | Stable | Highly Stable |
Flowability | High | Medium-High | Medium | Low |
Shrinkage | High | Medium | Low | Very Low |
Strength Enhancement | None | Moderate | Significant | Exceptional |
Processing Tolerance | Wide | Relatively Wide | Normal | Narrow |
Industrial Value of Glass Fiber Reinforcement
Glass fiber reinforcement is not merely about performance—it represents the transformation of plastic injection into high-end applications. It plays an irreplaceable role in supporting high-load, precision, and metal-replacement scenarios.
1.Lightweight Metal Substitution: Replacing metal parts in automotive and appliances to reduce cost and weight.
2.Optimized Structural Components: Enhances long-term reliability in brackets and connectors.
3.Extended Product Lifespan: Mitigates deformation and fatigue caused by creep.
4.Reduced Maintenance Costs: Consistent material performance reduces replacements and repairs.
Conclusion
Glass fiber reinforcement is a cost-effective solution that significantly improves the anti-creep and anti-deformation capabilities of injection-molded parts. By coordinating material selection, structural design, and process parameters, its full benefits can be achieved. Its industrial value extends beyond the material itself and is key to advancing manufacturing innovation.
For expert assistance in implementing for your production needs, visit our resource center or contact us. Let’s help you scale up your manufacturing with precision and efficiency!
Post time: Jul-08-2025