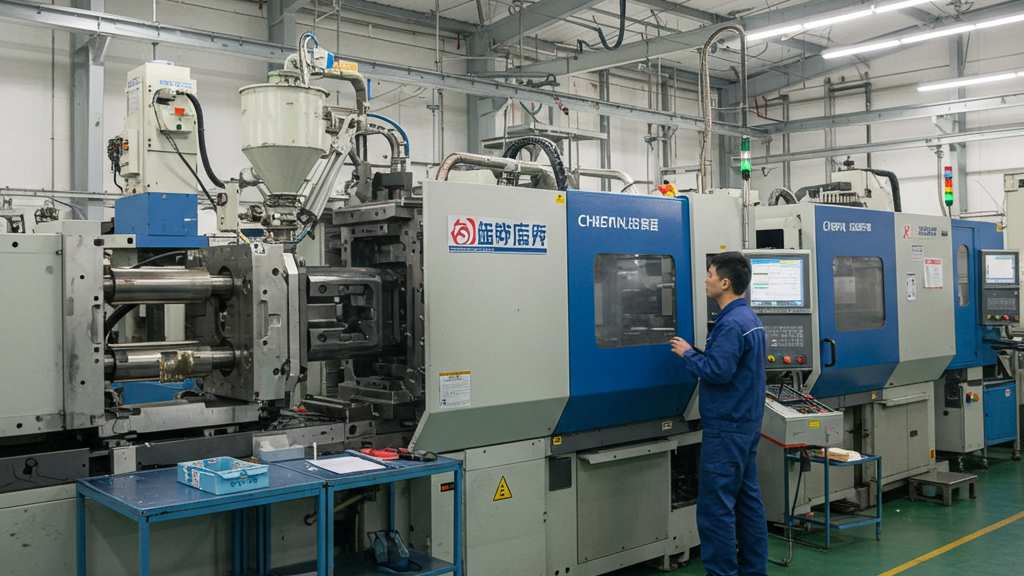
Producing high-quality polycarbonate (PC) lenses requires extreme precision and optical integrity. However, air and gases in the mold cavity are easily trapped during the injection molding process, leading directly to serious defects such as bubbles and burn marks. These defects can significantly reduce the optical performance and yield of the lenses. Therefore, for PC lens injection molding, mold breathing is a critical technique for preventing such defects and ensuring that products meet optical standards.
Now that we understand the hazards of ineffective breathing for PC lenses, it is crucial to achieve effective gas venting. A scientific and rational mold breathing design is more than just simply opening holes; it involves accurately determining the gas accumulation points and setting up appropriate vent channels. By optimizing the vent location, size, and method, we can ensure that gases are smoothly discharged during the filling process. Next, we will delve into the breathing design principles and implementation details for PC lens molds.
Why is Efficient Venting Necessary for PC Lens Injection Molding?
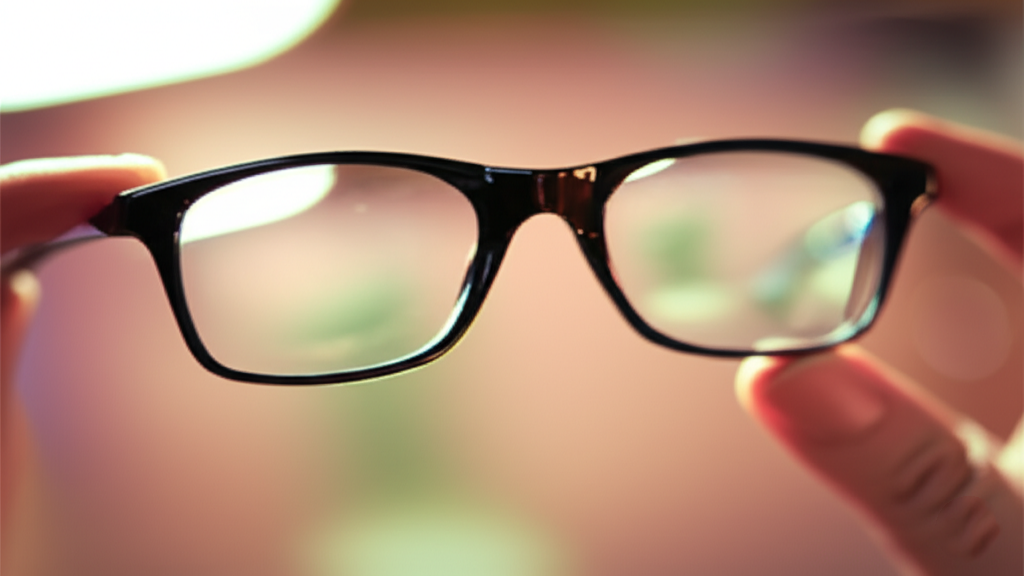
Polycarbonate (PC) lenses are widely used for their excellent optical performance and impact resistance, which places extremely high quality and defect-free requirements on their precision injection molding. Given the flow characteristics of PC material and the common thin-walled or complex structures of lenses, even trace amounts of residual gas in the mold cavity can severely compromise the optical transparency and mechanical properties of the final product.
- Stringent Optical Requirements: PC lenses have zero tolerance for transparency and defects, with even small gas residues leading to product rejection.
- Melt Characteristics and High-Speed Filling: The high viscosity of PC melt and the characteristics of thin-wall, high-speed filling make it extremely easy for gases to become trapped in the mold cavity.
- Gas Compression Leading to Burn Marks: The diesel effect caused by trapped, high-pressure gas can cause the PC resin to burn, damaging the product’s appearance and performance.
- Complex Structures Prone to Trapping Gas: The complex and diverse geometries of PC lenses easily create “dead zones” where gas is difficult to vent.
How Does Mold Breathing Work?
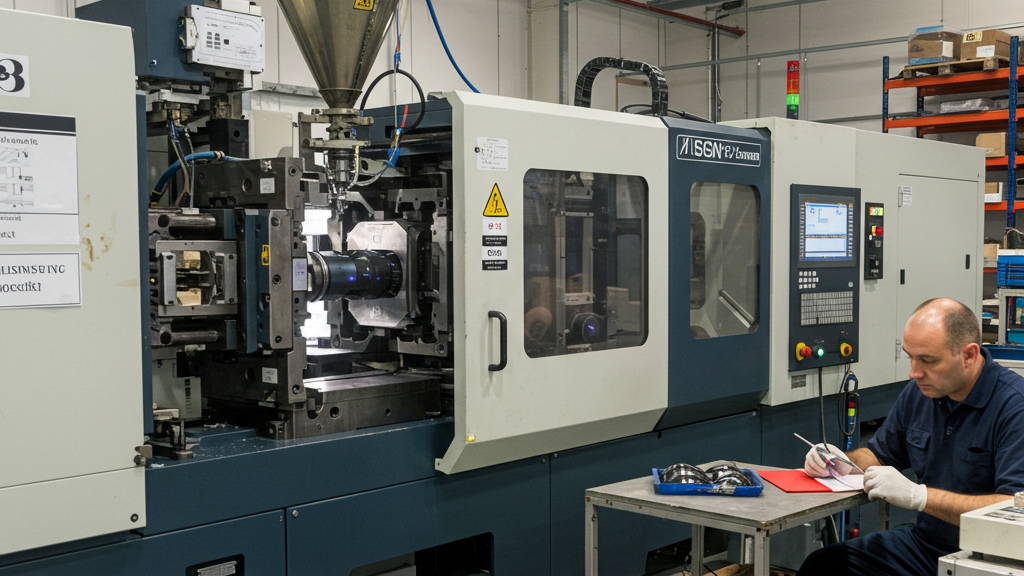
Having clarified the importance of efficient breathing in PC lens injection molding, a deep understanding of the basic working principles of mold breathing becomes essential. The core of this process lies in providing a low-resistance escape path for the gas that is compressed and pushed during the injection process, which is prioritized over melt filling, through specific structures within the mold.
- Gas Displacement: As the injected melt enters the mold cavity, it squeezes and pushes out the existing gas.
- Building an Escape Channel: The mold provides a low-resistance path for the gas through vent slots and holes.
- Pressure Difference Driving: The pressure difference between the mold cavity and the outside drives the gas to escape along the channel.
- Melt Solidification Sealing: The micro-shallow channel allows the melt to solidify quickly, achieving gas separation and sealing the mold cavity.
How Does Venting Prevent Defects in PC Lenses?

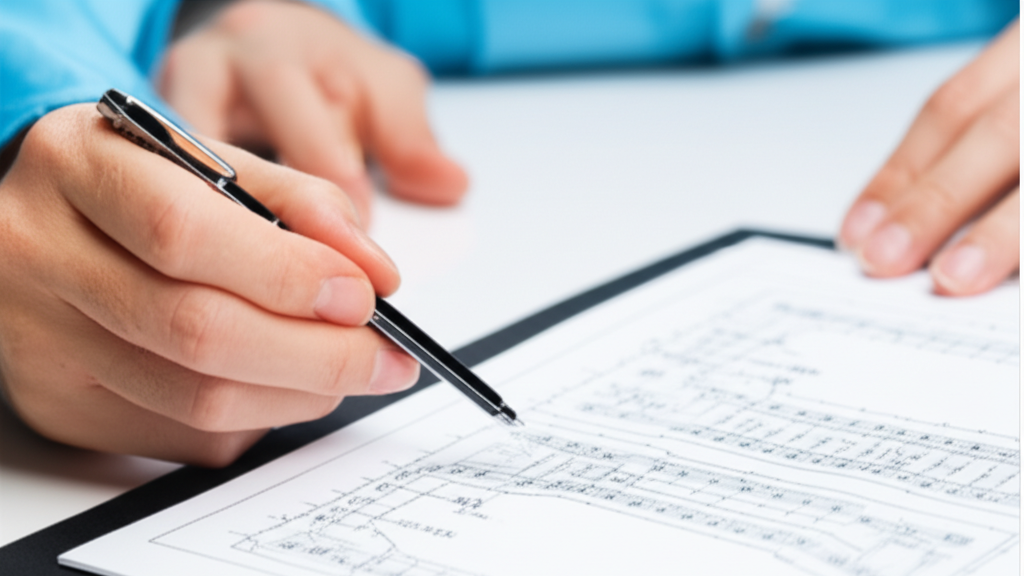
Building upon our understanding of how mold breathing establishes a gas escape path, we further explore how it directly combats key factors leading to defects in PC lenses in practice. By ensuring that gas within the mold cavity is adequately vented, effective breathing design fundamentally eliminates the problems of gas entrapment, high-pressure compression, and the resulting localized overheating and burn marks.
- Eradication of Bubbles and Voids: Effective breathing provides a gas escape path, eradicating bubbles and voids within the mold cavity.
- Reduction of Filling Backpressure: Venting reduces backpressure in the mold cavity, optimizing filling behavior and reducing gas entrainment.
- Prevention of Resin Burning: Prevents extreme compression of gas, avoiding the diesel effect and burning of PC resin.
- Optimization of Flow Quality: Improves melt flow and confluence, enhancing surface and weld line quality.
Control of defect prevention
Mold Venting Working Principle | Key Problem Countered | Common PC Lens Defect Prevented |
Provides Gas Escape Path | Gas trapped in cavity, causing Entrapment | Bubbles / Internal Voids |
Reduces Cavity Filling Back Pressure | Melt pushes High-Pressure Gas, hinders filling | Short Shots / Some Bubbles / Unstable Flow |
Expels Gas Promptly, Prevents Extreme Compression | Gas undergoes Extreme Compression & Adiabatic Heating in confined space | Burning (Diesel Effect) / Resin Degradation Marks |
Optimizes Melt Flow & Merging | Gas Trapped at Melt Merge Points / Poor Flow | Knit Line Defects / Flow Marks / Reduced Transparency |
Key Design Considerations for PC Lens Mold Venting
After fully understanding the importance of mold breathing for preventing defects in PC lenses and its basic working principles, the core challenge turns to how to effectively apply these principles in actual mold design. To ensure that PC lenses achieve the highest standards of optical performance and quality, mold breathing is no longer a simple add-on step, but a critical link that requires strategic planning and precision engineering.
1.Precise Vent Location: It is necessary to accurately determine the vent locations where gas ultimately accumulates through analysis.
2.Precise Dimensions of Vent Slots: The key lies in precisely controlling the shallow depth and effective width of the vent slots.
3.Enhanced Venting Methods: Enhanced venting methods such as vacuum assist should be evaluated and considered.
4.Venting System and Maintenance: A complete venting channel needs to be designed and daily maintenance ensured.
Conclusion
Mold venting is a core key to achieving successful, high-quality PC lens injection molding. By effectively venting gas from the mold cavity, it directly prevents defects (such as bubbles and burn marks) caused by gas entrapment, high pressure, and the diesel effect. This relies on precise venting design and good practical maintenance. Mastering mold venting technology is a prerequisite for stable production of defect-free PC optical lenses.
For expert assistance in implementing for your production needs, visit our resource center or contact us. Let’s help you scale up your manufacturing with precision and efficiency!
Post time: May-16-2025