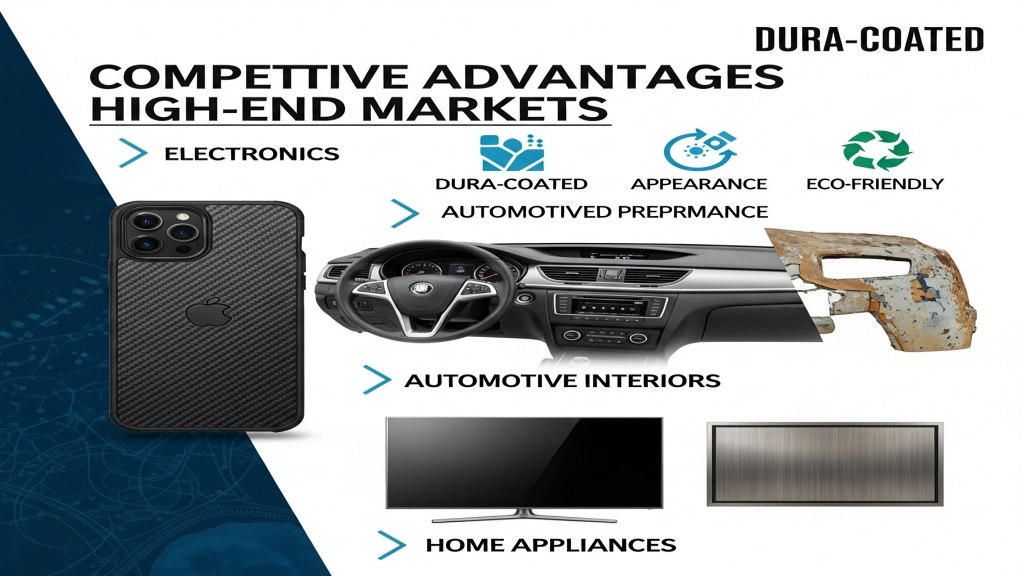
As an innovative surface treatment technology, Dura-Coated has been widely adopted for aesthetic upgrades of injection molded parts. It enables high-end textures like carbon fiber or brushed metal without changing base materials.It not only enhances the product’s visual appeal but also broadens its application scope.
The Dura-Coated layer has strong adhesion and abrasion resistance, allowing plastic parts to retain structural integrity while gaining functional aesthetics. This technology is becoming a preferred solution in consumer electronics and automotive interiors.
How to Achieve Carbon Fiber or Brushed Metal Texture?
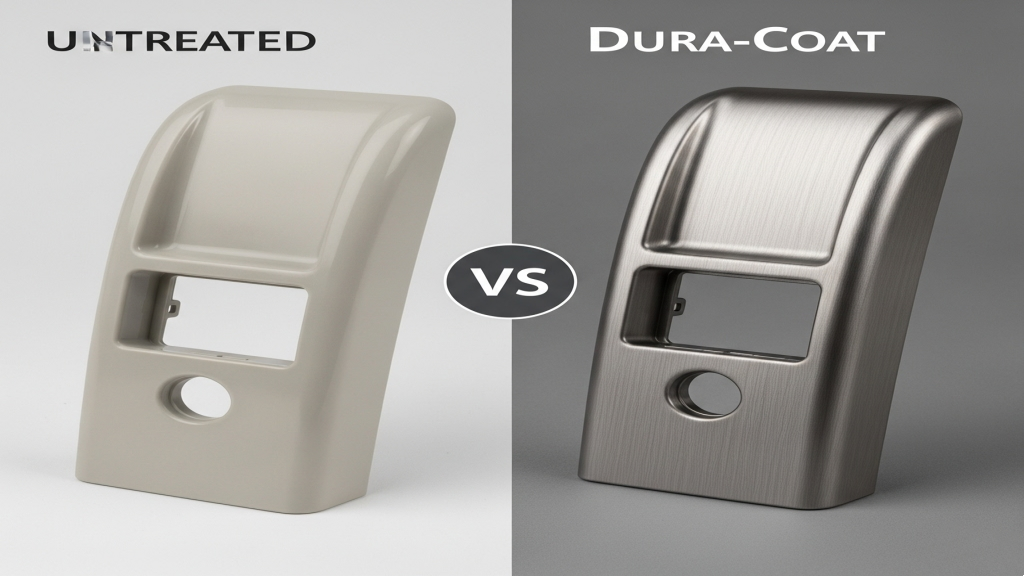
Dura-Coated is achieved through multilayer coating and UV curing, forming a realistic texture layer on injection surfaces. This method precisely replicates the fine weave of carbon fiber or the grain of brushed metal, significantly boosting product appeal.
- Coating Control MattersMold Release Consideration: Requires proper mold design to keep the coating intact.: Consistent thickness and equipment speed are critical for uniform texture.
- UV Curing Advantage: Rapid curing forms a tough outer layer with scratch resistance.
- Mold Release Consideration: Requires proper mold design to keep the coating intact.
- Surface Cleanliness Required: Must be dust-free before coating to prevent defects.
Which Injection Parts Are Suitable for Dura-Coated?
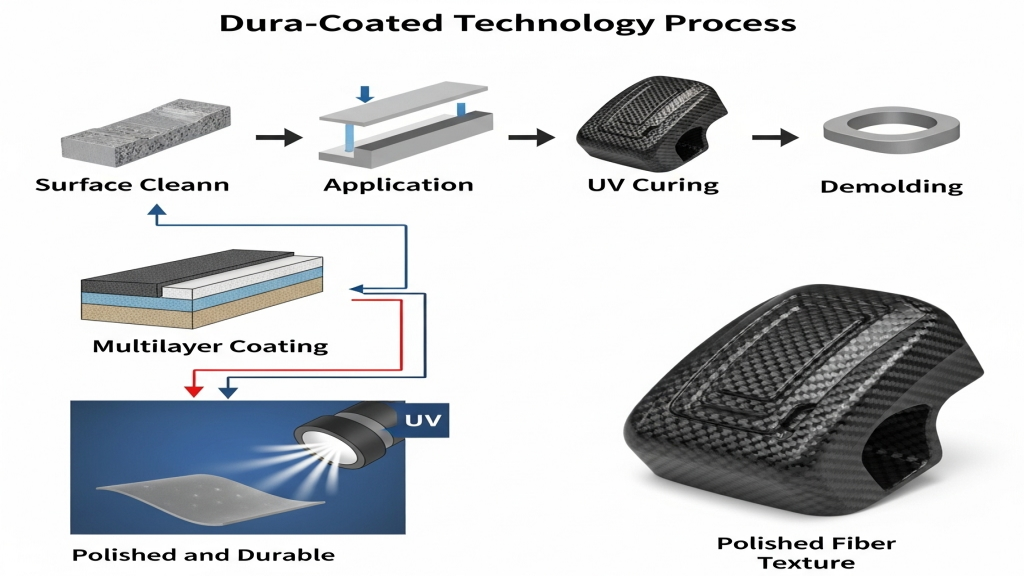
Dura-Coated works best on surfaces with high flatness and dimensional stability, such as PC, ABS, and PMMA plastics. Each plastic type needs tailored basecoats and process controls for optimal adhesion and finish.
- High Compatibility with PC: PC offers thermal stability and clarity, ideal for textured finishes.
- ABS Widely Applied: Excellent basecoat bonding and color accuracy.
- PMMA for Optical Appeal: Can create mirror-like metallic effects post-coating.
- Complex Parts Need Optimized Design: Avoid sharp corners and shadow zones for even coatings.
What Problems Can Arise During the Process?
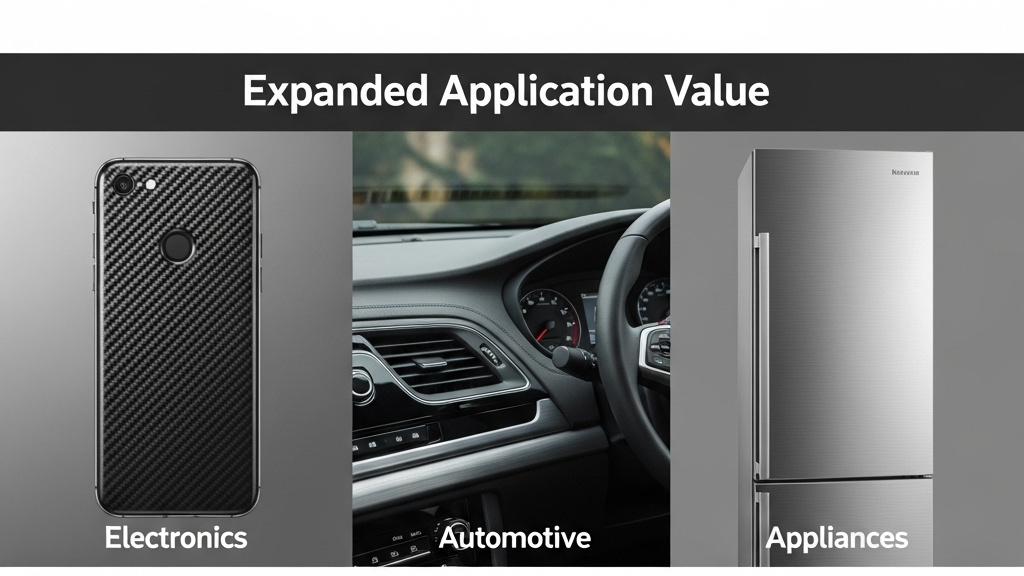
Common Dura-Coated issues include poor adhesion, pattern misalignment, uneven spray, and incomplete UV curing. These typically result from incompatible materials or imprecise control.
- Adhesion Testing Is Crucial: Test adhesion before every production batch.
- Pattern Shift Needs Adjustment: Fine-tune stencil alignment to avoid overlaps.
- Spray Angle Must Be Uniform: Use automated equipment for consistency.
- Calibrate UV Energy: Prevent undercured areas that may peel or stay sticky.
Surface Texture Scheme Comparison
Material/Process |
Dura-Coated Carbon Fiber |
Dura-Coated Brushed Metal |
Electroplating |
IMD Film Injection |
Texture Realism | High | High | Medium | Medium |
Cost Control | Medium | Medium | High | Medium |
Mass Efficiency | High | High | Low | Medium |
Surface Durability | High | High | Medium | Low |
Application Value Expansion
Dura-Coated technology not only gives plastic parts a refined texture but also boosts competitiveness in premium markets. Ideal for use in electronics housings, automotive interiors, and appliance panels. Its lifelike visual and tactile effects surpass traditional painting and plating.
1.Premium Look Creation: Mimics carbon fiber or metal textures for high-end feel.
2.Enhanced Durability: Hard coating and UV resistance for longevity.
3.Eco-Friendly Alternative: No toxic emissions, aligned with sustainability goals.
4.Design Flexibility: Suitable for complex geometries and diverse textures.
Conclusion
Dura-Coated offers a highly effective solution for adding carbon fiber or brushed metal textures to injection molded parts. With excellent fidelity, adhesion, and efficiency, it is an ideal method for aesthetic upgrades.By aligning mold design, coating techniques, and materials, it unlocks new design freedom and commercial potential in the plastics industry.
For expert assistance in implementing for your production needs, visit our resource center or contact us. Let’s help you scale up your manufacturing with precision and efficiency!
Post time: Jul-02-2025