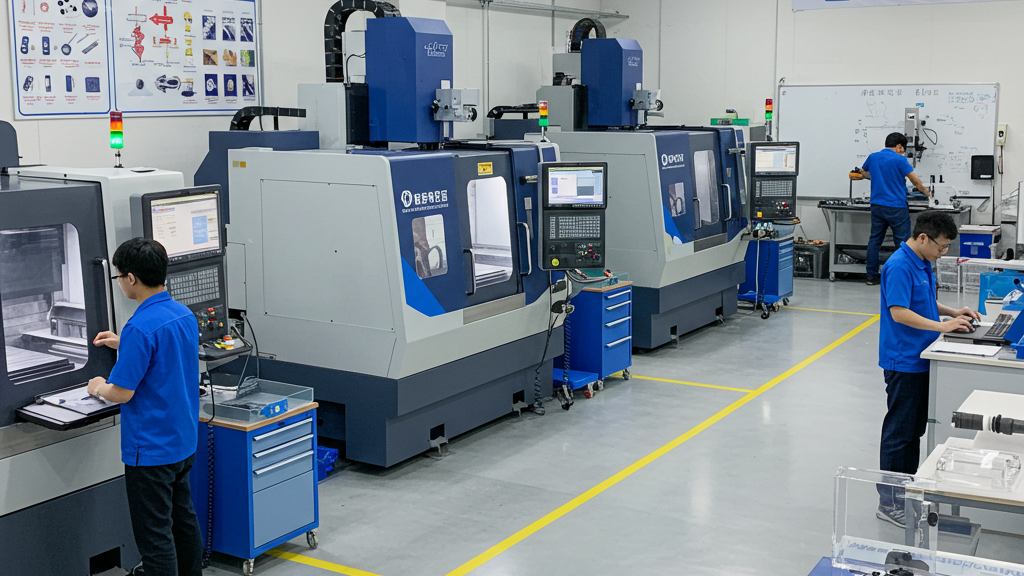
CNC technology has been widely applied in precision acrylic machining, but traditional methods exhibit limitations when facing complex designs. Multi-axis composite machining has emerged to address this, aiming to complete features such as complex curved surfaces and multi-angle holes in a single setup.
Achieving CNC multi-axis composite machining of acrylic is not simply a matter of adding equipment. The key lies in technical support and collaboration. Next, we will delve into the core elements, including the selection of multi-axis CNC machine tools, tool optimization for acrylic, and parameter settings.
What are the advantages of multi-axis composite machining for acrylic?
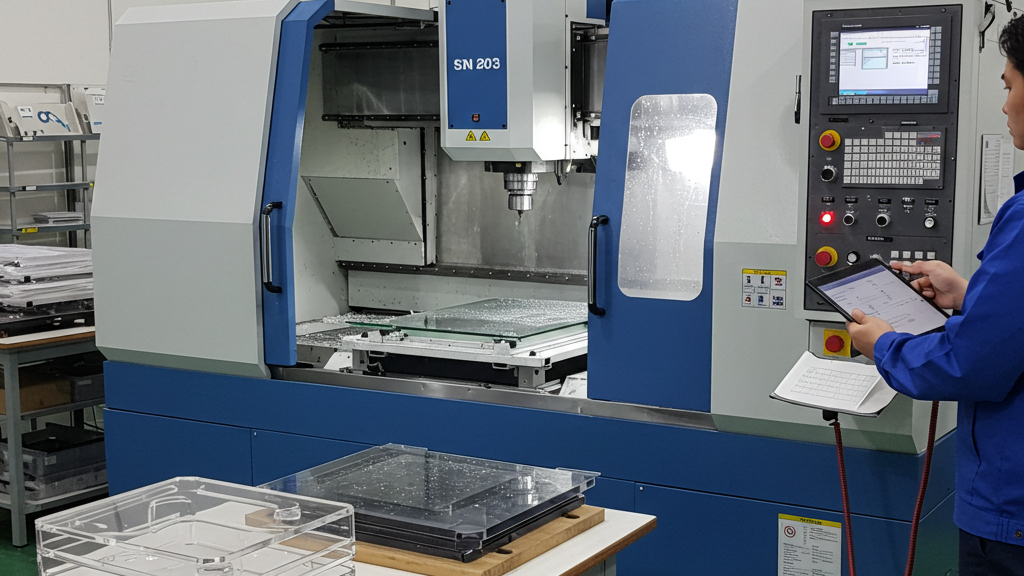
By integrating various machining capabilities into one, multi-axis composite CNC technology breaks through the bottlenecks of acrylic machining, providing strong support for achieving higher quality, higher efficiency, and more innovative product designs.
- Complex Shape Machining: Multi-axis linkage significantly improves the precision machining capability of complex acrylic geometries.
- Reduced Setup and Improved Efficiency: Completing multi-process machining in a single setup greatly shortens the production cycle and reduces errors.
- High Precision and Quality: More optimized toolpaths and cutting conditions result in higher machining accuracy and surface quality.
- Process Integration and Cost Reduction: Integrating multiple processes reduces equipment investment and process flow, enabling more economical production.
What are the key technologies for multi-axis composite machining of acrylic?
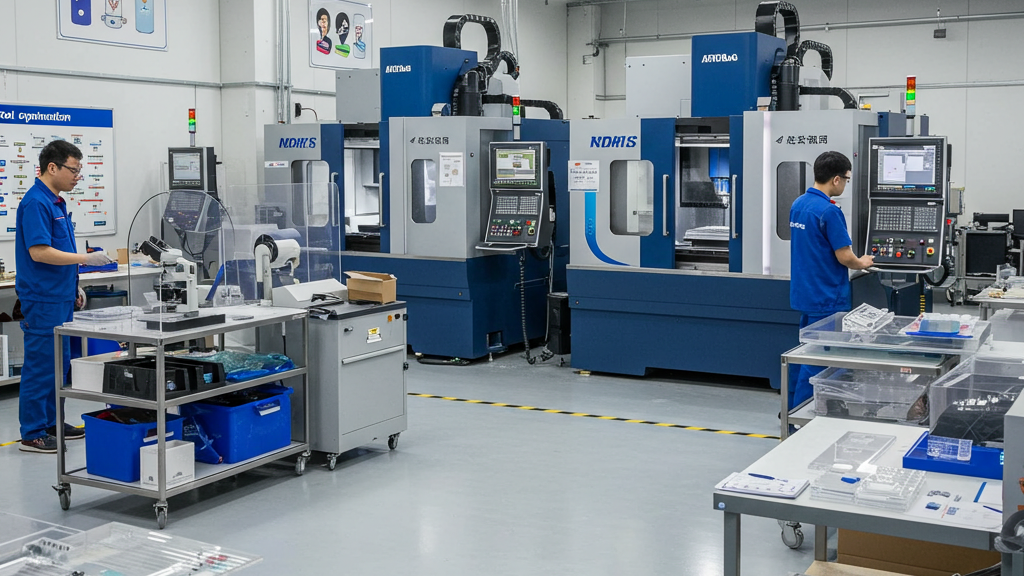
Successfully achieving multi-axis composite machining of acrylic requires careful consideration and optimization of several key technical aspects. Among these, the performance selection of machine tools, the rational application of cutting tools, and the precise setting of process parameters are core elements for ensuring machining efficiency and quality.
- Machine Tool Selection and Configuration: Select high-precision, high-rigidity multi-axis linkage CNC machine tools and rationally configure related components.
- Cutting Tool Optimization and Selection: For acrylic characteristics, choose sharp, good chip removal special cutting tools and optimize the design.
- Process Parameter Setting: Accurately set process parameters such as cutting speed and feed speed to avoid overheating and ensure quality.
- CAM Programming and Simulation: Use professional CAM software to plan and optimize toolpaths and perform simulation verification.
How to optimize CAM programming for multi-axis composite machining of acrylic?
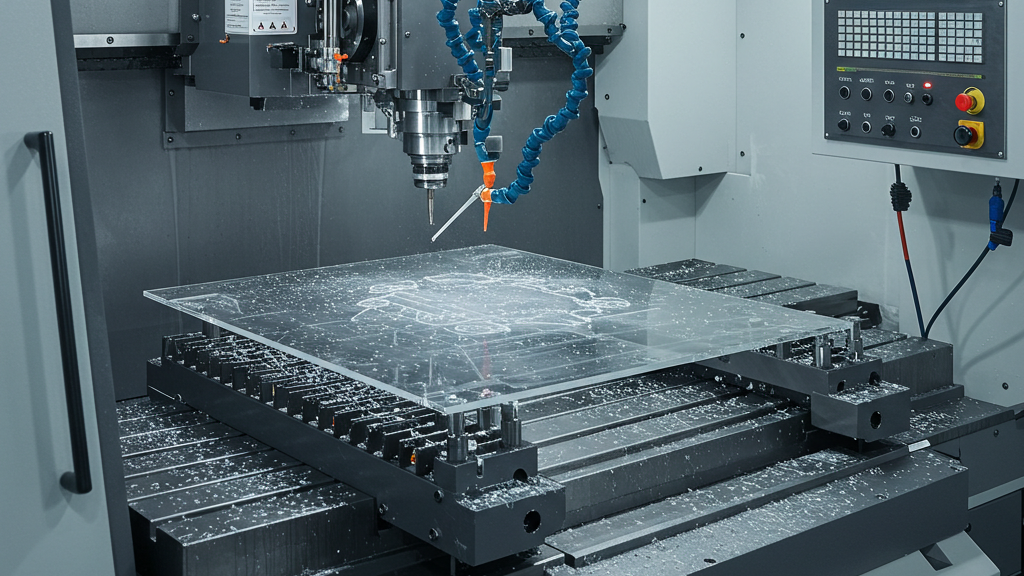
Given the special physical properties of acrylic materials, precise machining strategies must be developed during CAM programming and path planning for multi-axis composite machining, giving full consideration to its heat sensitivity, tendency to generate chip adhesion, and susceptibility to scratches.
- Optimize Toolpath for Heat Dissipation: Use smooth toolpaths to reduce the accumulation of cutting heat and avoid melting and adhesion to the tool.
- Control Cutting Parameters to Reduce Force: Rationally set cutting parameters and use multi-axis linkage to disperse cutting forces, ensuring machining stability.
- Design Chip Removal and Cooling Paths: Plan toolpaths that facilitate chip removal and combine auxiliary measures to avoid secondary cutting and scratches.
- Optimize Tool Orientation to Improve Quality: Fully utilize multi-axis linkage to adjust tool orientation, improve surface finish, and reduce damage.
Analysis of processing technology
Feature/Aspect |
Traditional CNC Acrylic Machining |
Multi-Axis Compound CNC Acrylic Machining |
Advantage Comparison |
Complex Shape Machining Capability | Primarily relies on simple axis movement; complex surfaces require multiple setups or special fixtures. | Can flexibly control tool posture through multi-axis linkage; achieves complex surfaces and irregular structures in one setup. | Significantly Enhanced: Capable of machining complex geometries that are difficult or inefficient with traditional methods. |
Number of Setups | Multiple setups usually required for machining different faces or features. | Completes machining of multiple angles and processes in one setup. | Greatly Reduced: Lowers setup errors, shortens auxiliary time and production cycle. |
Machining Accuracy | Multiple setups easily introduce cumulative errors, affecting overall accuracy. | One setup reduces error accumulation; multi-axis linkage enables more precise tool control. | Significantly Improved: Reduces human errors and repetitive positioning errors, ensuring higher machining accuracy. |
Surface Quality | Complex surfaces may require multiple finishing passes; surface consistency is difficult to guarantee. | Multi-axis linkage can optimize tool paths and cutting conditions to obtain more uniform and smooth surfaces. | Significantly Enhanced: Achieves better surface finish and consistency, especially on complex surfaces. |
Process Integration | Single-function machine tools; multiple processes require completion on different equipment. | Can integrate multiple processes such as milling, drilling, and tapping on one machine tool. | Significantly Enhanced: Reduces inter-process flow and waiting time, improving production efficiency. |
Multi-Axis Composite Machining of Acrylic
Although CNC multi-axis composite machining of acrylic exhibits great potential, it also faces challenges such as high equipment costs, high technical barriers, and insufficient accumulation of process experience for acrylic characteristics. With the increasing demand for complex and customized products in the manufacturing industry, as well as the continuous maturity and cost reduction of multi-axis linkage technology, CNC multi-axis composite machining of acrylic is ushering in unprecedented development opportunities.
1.Equipment and Talent: High equipment investment and a shortage of specialized talent restrict the popularization of multi-axis composite machining.
2.Process and Fixturing: Insufficient process experience for acrylic and complex shape fixturing pose challenges.
3.Demand and Technology: Growing customization demands and technological maturity bring opportunities for multi-axis composite machining.
4.Intelligence and Environmental Protection: The future will evolve towards intelligence, automation, and environmental sustainability.
Conclusion
CNC multi-axis composite machining of acrylic offers significant advantages in complex shape manufacturing, reducing fixturing, and improving precision, meeting the growing demand for customization. Although it faces challenges such as high equipment costs and technical barriers, its development opportunities outweigh the challenges. Multi-axis composite machining is an important development direction for the acrylic processing industry.
For expert assistance in implementing for your production needs, visit our resource center or contact us. Let’s help you scale up your manufacturing with precision and efficiency!
Post time: May-06-2025