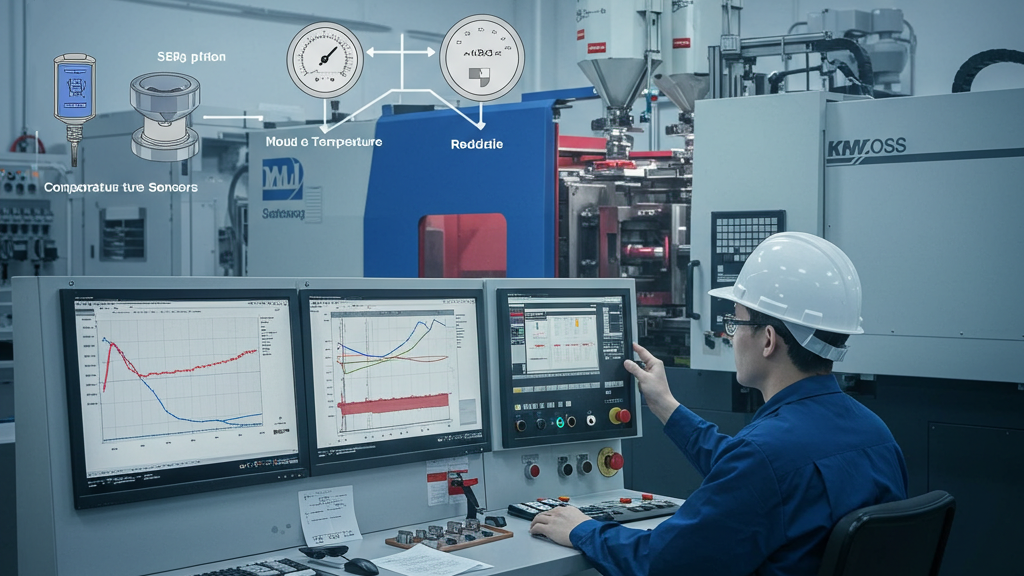
Color, for ABS injection molded products, has transcended mere decoration to become a key element of function and brand expression. Breaking through the limitations of single-color, achieving multi-color co-injection is a focal point of industry innovation. This article will explore the key technologies, process flows, advantages, and challenges of multi-color co-injection of ABS products from a professional perspective, providing a reference for technical personnel.
what key technologies can achieve precise fusion of different colored ABS materials within the same mold cavity? Next, we will focus on mainstream processes such as double-shot moulding and multi-component injection molding, analyze their principles, equipment requirements, and considerations in ABS applications, and explore how to control the fluidity, weld lines, and molding quality of color materials to achieve multi-color designs.
What are the mainstream processes for ABS multi-color co-injection?
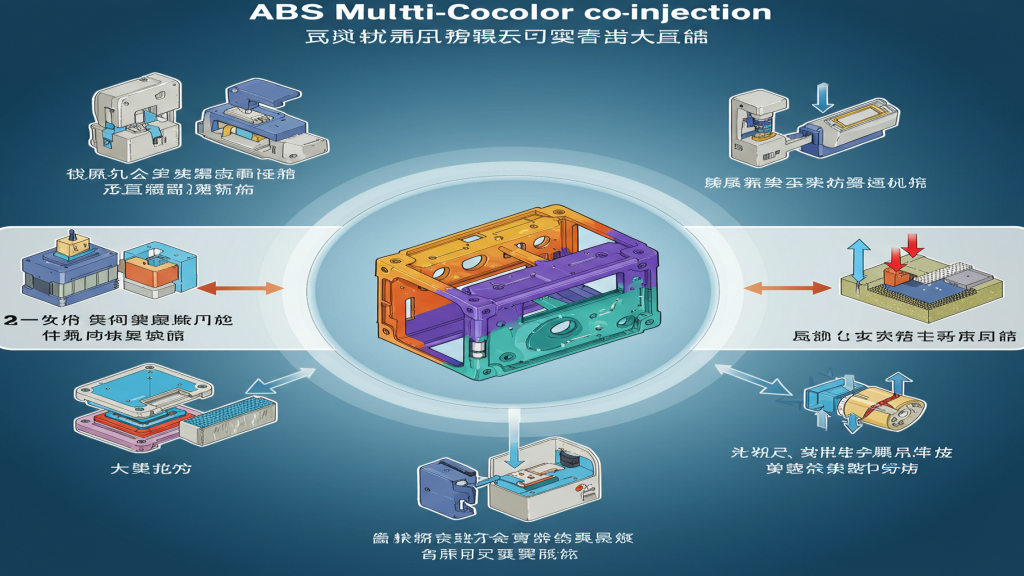
Achieving multi-color injection molding effects for ABS products currently relies on several mature process technologies. These processes skillfully control the injection timing and paths of different color materials, giving products rich color layers and functional integration.
- Double-shot moulding: Double-shot moulding imparts a multi-color appearance with clear boundaries and high bonding strength to ABS products through two independent injection molding processes.
- Multi-component injection molding: Multi-component injection molding uses two or more injection units to achieve simultaneous or sequential injection of multiple ABS materials, bringing more complex functional and color designs.
- Overmolding: Overmolding first molds an ABS substrate and then overmolds another color ABS in specific areas, often used to enhance product feel and visual effects.
- Insert molding: Insert molding pre-places ABS inserts of different colors into the mold, and then injects the main ABS material, forming a localized multi-color effect.
What are the key points for process parameter control in ABS multi-color co-injection?
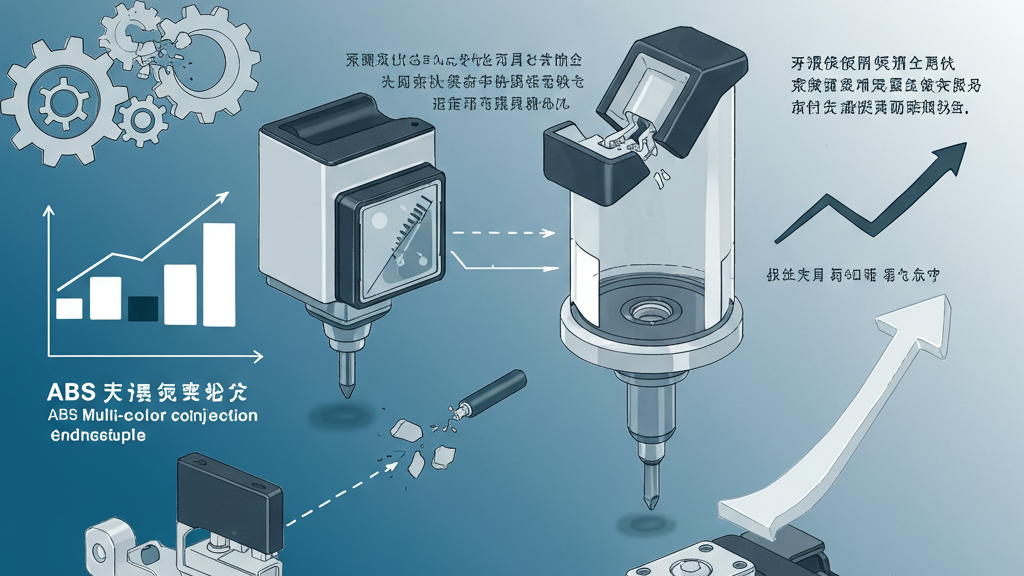
When performing multi-color co-injection with ABS materials, precise control of process parameters is crucial, as it directly affects the quality of the final product and the realization of multi-color effects. Considering the physical and chemical properties of ABS, such as melt flow, heat sensitivity, and potential differences between different color batches, the setting of process parameters requires extra caution.
- Melt Temperature Control: Precisely control the melt temperature of each injection unit to ensure similar fluidity of different colored ABS materials, avoiding fusion defects.
- Injection Pressure and Speed Control: Reasonably set injection pressure and speed according to the mold and material characteristics to optimize filling and interface fusion effects.
- Holding Pressure and Time Control: Adjust holding pressure parameters to compensate for shrinkage and improve dimensional accuracy and the bonding strength of multi-color areas.
- Mold Temperature Control: Maintain a uniform and appropriate mold temperature to promote uniform cooling and solidification of different colored ABS materials, reducing deformation.
What are the key aspects of mold design for ABS multi-color co-injection?
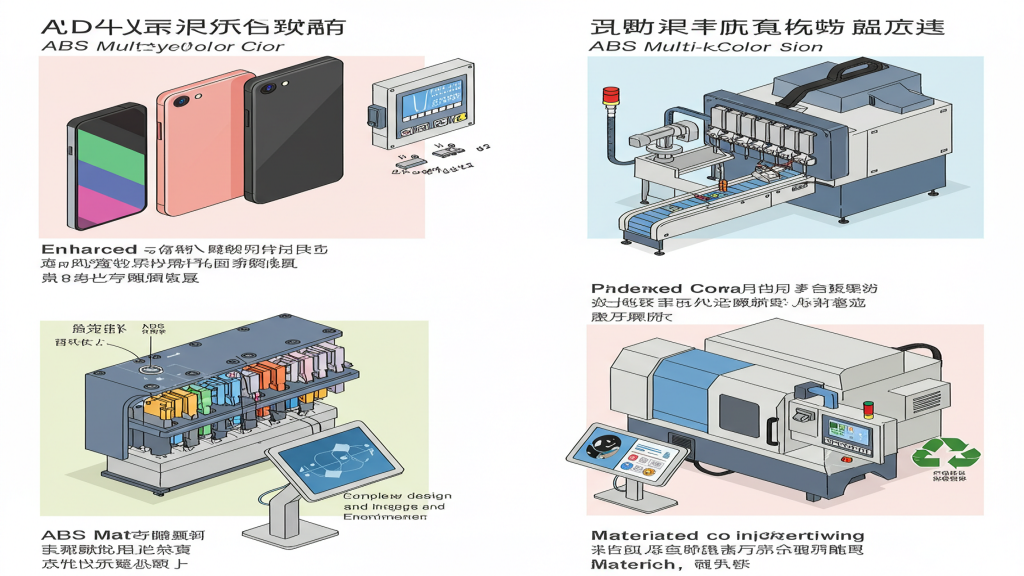
The realization of high-quality ABS multi-color co-injection products largely depends on precise and optimized mold design. To ensure smooth filling, uniform fusion of different colored ABS materials, and excellent appearance and performance of the final product, every aspect of the mold needs careful consideration. Among these, key elements such as runner layout, gate location, and parting surface treatment are particularly important.
- Independent Feed System: Design independent runners for each color of ABS to ensure that the materials do not interfere with each other and fill along the intended paths.
- Reasonable Gate Location and Type: Optimize gate layout and type to avoid obvious weld lines on critical surfaces and improve product appearance.
- Precise Parting Surface Design and Sealing: Design reliable mold movement mechanisms and tight seals to ensure precise separation and good bonding of multi-color materials.
- Effective Venting System: Set up a reasonable venting structure to ensure smooth expulsion of gas from the mold cavity, avoiding product defects.
Characteristics of ABS application
Process Name |
Working Principle |
Key Features |
Advantages in ABS Application |
Aspects to Note in ABS Application |
Typical Application Examples |
Two-Shot Injection Molding | Two independent injection units sequentially inject different colored/material ABS into the same mold. | Clear color separation, high bonding strength, capable of complex multi-color/material combinations. | Suitable for ABS products requiring clear two-color or functional dual-material, such as tool handles, appliance housings. | Requires precise mold design and control, pay attention to the compatibility of the two ABS materials and weld line control. | Power tool handles, two-color buttons, automotive interior parts |
Multi-Component Injection Molding | Two or more injection units simultaneously or sequentially inject multiple different colored/performance ABS. | Enables richer color and functional integration, such as soft-hard bonding, functional differentiation of different colored areas. | Can manufacture ABS products with complex color distribution and functional integration, such as multi-colored toys, complex structural parts. | Mold design is very complex, process control requirements are high, consider the compatibility of multiple ABS materials and injection timing. | Multi-colored toys, automotive dashboards, electronic product housings with soft-hard bonding |
Overmolding | First molding an ABS substrate of one color, then overmolding specific areas with another color ABS. | Good bonding strength, commonly used for achieving local multi-color or different tactile designs. | Suitable for ABS parts requiring local color changes or different tactile sensations, such as handles, buttons. | Requires two molding steps, production efficiency may be lower, ensure good adhesion between the substrate and overmolding material. | Tool handles with overmolding, appliance buttons, anti-slip mats |
Insert Molding | Pre-placing ABS inserts of different colors in the mold, then injecting the main color ABS. | Relatively simple process, suitable for small batches or local color variation needs. | Suitable for small batches or products with frequent design changes, as well as ABS parts with locally specific colors. | Color bonding area may not be natural enough, precise control of insert fixing and positioning is required. | Electronic product decorative parts, local color markings |
What are the Advantages and Challenges of ABS Multi-Color Co-Injection?
Multi-color co-injection technology brings significant application advantages to ABS products, not only giving products a more attractive appearance and greater design flexibility but also potentially achieving functional integration and enhancing product market competitiveness. When choosing to adopt multi-color co-injection technology, it is necessary to comprehensively evaluate product requirements, technical capabilities, and cost budgets, weighing the pros and cons to achieve the best application results.
1.Enhance Appearance and Design: Multi-color co-injection directly achieves a brilliant appearance and flexible design without additional processes.
2.Improve Efficiency and Reduce Costs: One-time molding reduces post-processing, shortens cycles, and lowers overall production costs.
3.Enhance Functionality and Value: The combination of multiple materials enhances product functionality, and multi-color designs increase product added value.
4.Improve Environmental Performance: Reducing processes such as painting reduces VOC emissions and facilitates product recycling.
Conclusion
Achieving multi-color co-injection for injection-molded ABS products is a key technology that integrates materials science, mold design, and precision processing. Through mainstream processes such as two-shot molding, multi-component injection molding, overmolding, and insert molding, ABS products can break through the limitations of traditional single colors, exhibiting a rich and colorful appearance and integrated functionality.
For expert assistance in implementing for your production needs, visit our resource center or contact us. Let’s help you scale up your manufacturing with precision and efficiency!
Post time: Apr-30-2025