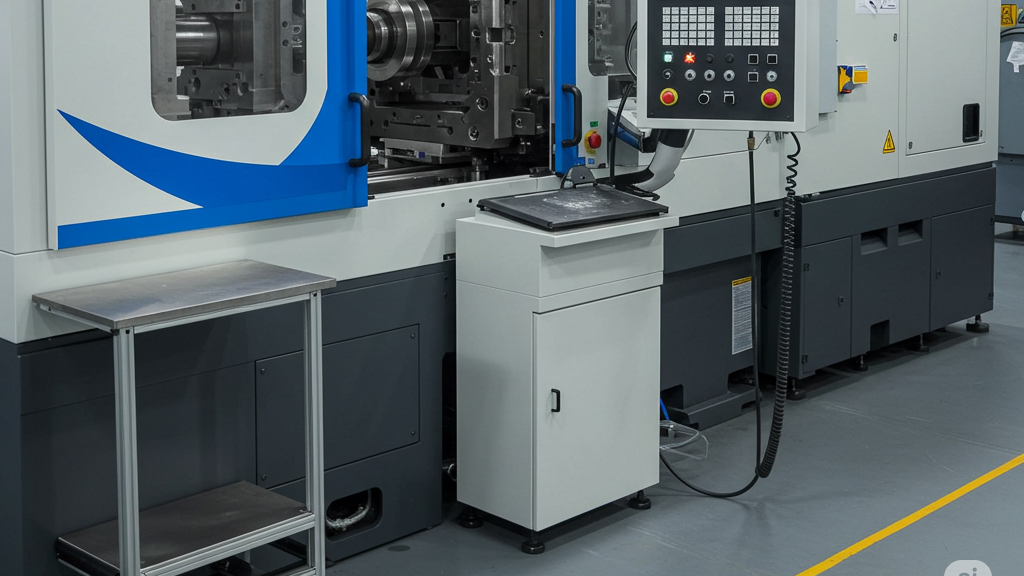
With the increasing demand for functional integration and structural complexity in products, insert molding has emerged as a solution. It can integrate prefabricated inserts with the base material in a single molding process, improving product performance and reliability. Thermoplastic polyurethane (TPU) is widely used due to its excellent properties. How to achieve the combination of TPU injection molding with different inserts is a focus of the industry. This article will explore the technical points, process considerations, and challenges of TPU insert molding, providing professional guidance.
The previous text emphasized the significance of insert molding for product performance and design, as well as the application potential of TPU. Achieving an effective bond between TPU and the insert is not easy, requiring precise process control and parameter adjustment. Next, we will focus on discussing the key aspects of TPU insert molding, such as insert pretreatment, mold design essentials, injection parameter optimization, and interface bonding issues, to build a clear technical framework.
What are the requirements for the insert material and surface in TPU insert molding?
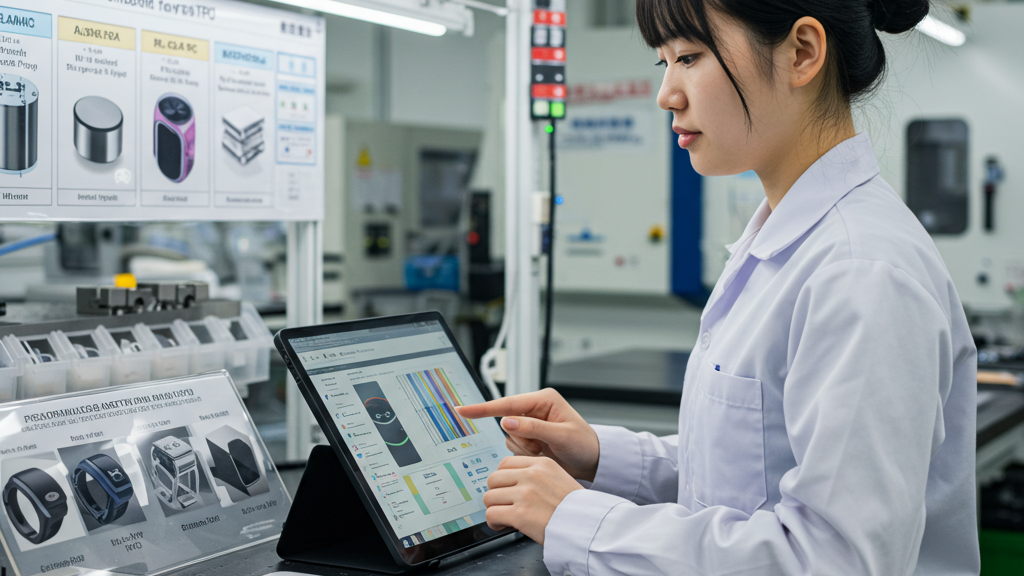
In the thermoplastic polyurethane (TPU) insert molding process, ensuring a strong bond between the insert and the TPU substrate is crucial. Therefore, specific requirements are placed on the insert’s material selection and surface pretreatment, as these factors directly affect the overall performance and reliability of the final product.
- Material Compatibility: The insert material needs to have good chemical or physical bonding potential with TPU.
- Surface Cleanliness: The insert surface must be clean and free of contamination to ensure direct contact.
- Surface Roughness: Appropriate surface roughness helps the TPU melt form mechanical interlocking.
- Preheating Treatment: Properly preheating the insert can improve the wettability and bonding strength of TPU.
What factors should be considered in the mold design for TPU insert molding?
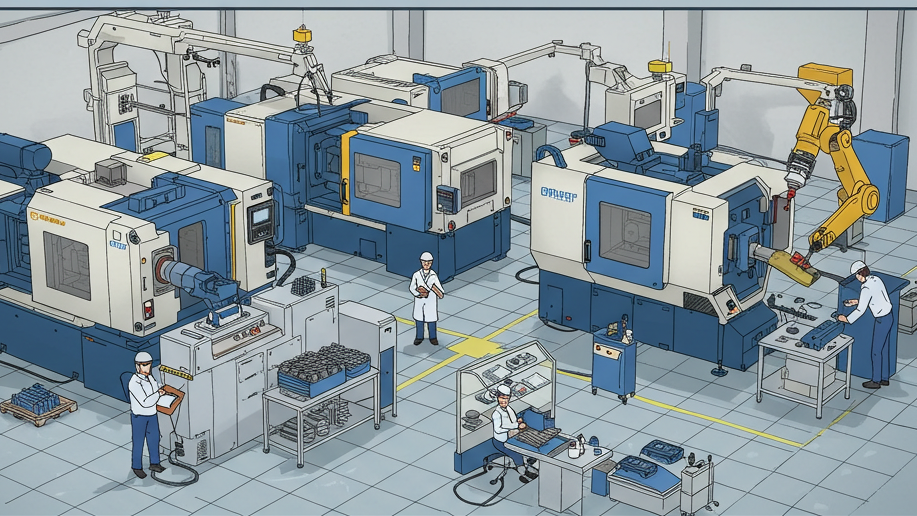
For inserts of different shapes and sizes, the design of TPU insert molding molds is a precise engineering task. To ensure that the insert maintains its precise position during the injection molding process and achieves high-quality encapsulation, the mold design must carefully consider the insert’s fixing method and the injection path of the molten TPU.
- Precise and Reliable Insert Positioning System: The mold needs to be designed with precise positioning structures to fix the insert position.
- Optimized Feed System Design: A reasonable feed system ensures uniform coating of the insert with TPU and reduces impact.
- Effective Venting System: The mold needs to have good venting function to avoid incomplete filling and bubbles.
- Mold Structure and Cooling Adapted to Insert Characteristics: The mold strength and cooling design need to adapt to the shape and size of the insert.
How can TPU injection parameters be optimized for inserts?
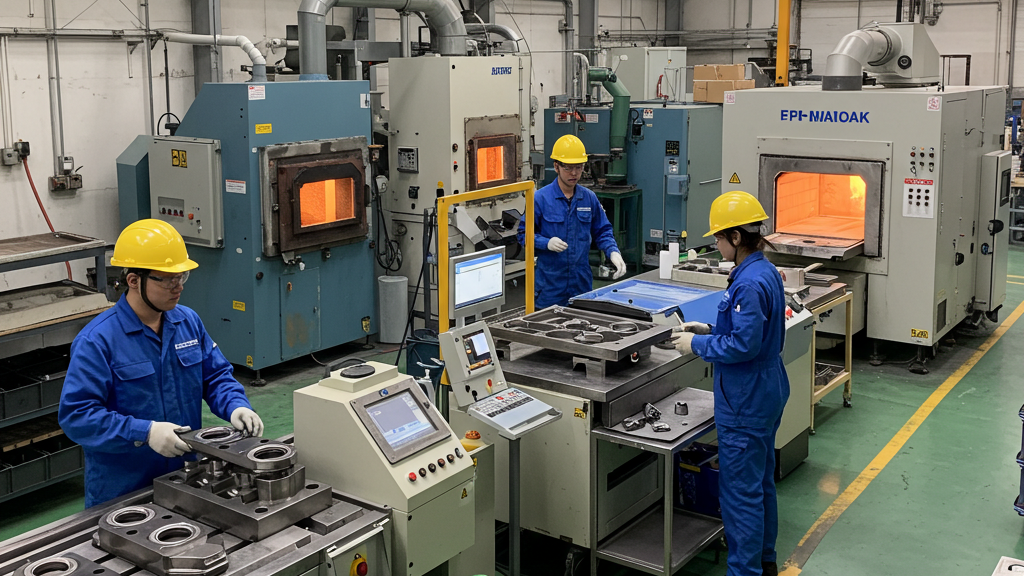
In the TPU insert molding process, the setting of process parameters directly affects the integrity of the insert and the filling quality of the TPU. Therefore, it is necessary to finely adjust and optimize key parameters such as injection temperature, pressure, and speed according to the characteristics of the insert and the flow behavior of the TPU.
- Reasonable Injection Temperature Control: Optimize the injection temperature to balance TPU flowability and the thermal impact on the insert.
- Appropriate Injection Pressure Setting: Adjust the injection pressure to ensure filling and avoid insert damage.
- Optimized Injection Speed Profile: Employ segmented injection speed control to reduce impact on the insert and ensure filling.
- Precise Control of Holding Time and Pressure: Properly set holding parameters to ensure bonding and reduce stress on the insert.
Key elements of TPU insert injection molding process
Key Aspect |
Main Considerations |
Potential Issues |
Solutions / Optimization Directions |
Quality Control Points |
Materials | TPU Type & Properties, Insert Material Compatibility & Surface Treatment | Poor Bonding, Insert Deformation/Contamination | Select Suitable Materials, Perform Surface Pre-treatment | Material Performance & Cleanliness Inspection |
Mold Design | Insert Positioning Method & Accuracy, Gate System Design, Venting Effect | Insert Displacement, Poor Filling, Air Traps | Optimize Positioning & Gate Design, Ensure Effective Venting | Insert Position Accuracy, Product Appearance Check |
Process Parameters | Injection Temperature, Pressure, Speed, Holding Pressure & Time | Insert Deformation/Damage, Insufficient Filling, Weak Bonding | Finely Adjust Injection Parameters, Control Impact on Inserts | Product Filling Completeness, Bonding Strength Test |
Quality Control | First Piece Inspection, In-Process Inspection, Final Inspection, Special Performance Testing (as needed) | Early Defects, Process Anomalies, Final Rejection, Substandard Performance | Strictly Implement Inspection Procedures, Monitor Production Process, Conduct Necessary Performance Tests | Dimension & Appearance Check, Function Test, Performance Evaluation |
Common quality problems after TPU insert bonding
The product quality after TPU bonding with inserts is of utmost importance. Common quality issues such as peeling, cracking, deformation, and insufficient bonding strength require the establishment of a comprehensive quality control system. Through rigorous inspection and testing, potential problems can be identified and resolved in a timely manner, thereby producing high-quality TPU insert molded products.
1.Peeling: Peeling usually stems from insert surface issues, material incompatibility, or improper injection molding parameters. Targeted improvements in surface, material selection, and process are needed.
2.Cracking: Cracking is often caused by excessive internal stress, differences in thermal expansion, or injection molding impact. Mold optimization, process control, and the selection of appropriate materials are necessary.
3.Deformation: Deformation is often caused by excessive injection molding temperature, excessive pressure, or insufficient mold support. It is necessary to reduce temperature and pressure and improve mold design.
4.Insufficient Bonding Strength: Insufficient bonding strength is the result of a combination of factors. A comprehensive optimization of materials, surface treatment, and injection molding process is required.
Conclusion
Thermoplastic Polyurethane (TPU) insert molding is a key technology for manufacturing complex functional products. Precisely controlling injection molding process parameters is crucial, such as temperature, pressure, and speed, to avoid insert damage and ensure good filling of the TPU. From material selection to final inspection, every step needs to be strictly controlled to produce high-performance TPU insert molded products that meet application requirements.
For expert assistance in implementing for your production needs, visit our resource center or contact us. Let’s help you scale up your manufacturing with precision and efficiency!
Post time: May-13-2025