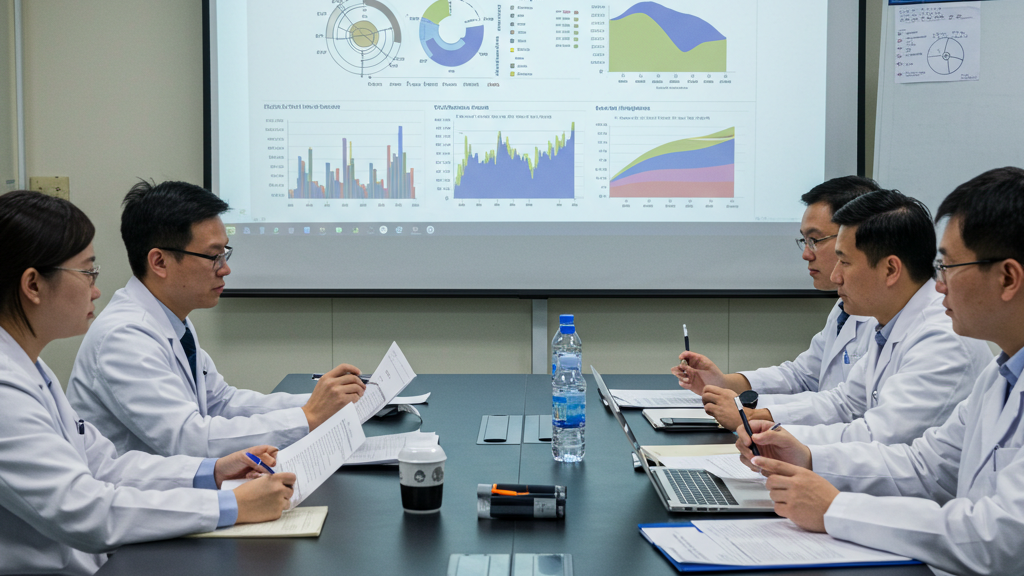
Stress cracking in polycarbonate (PC) injection molded parts, due to their excellent performance, are widely used, but the issue cannot be ignored, directly threatening product reliability. Understanding and resolving this challenge is critical for enhancing product quality. This article will delve into the causes of stress cracking in PC injection molded parts from various aspects, including material, process, mold, and post-treatment, and explore effective solutions.
Stress cracking of PC injection molded parts is the result of a combination of internal and external factors, rather than a single cause. Therefore, understanding these key influencing factors is crucial for solving the problem. Next, we will focus on analyzing material properties and various stress sources generated during the injection molding process, such as melt flow, cooling rate, and mold design defects. In-depth analysis of the root causes of stress generation will lay the foundation for subsequent targeted solutions.
Why is PC Prone to Stress Cracking?
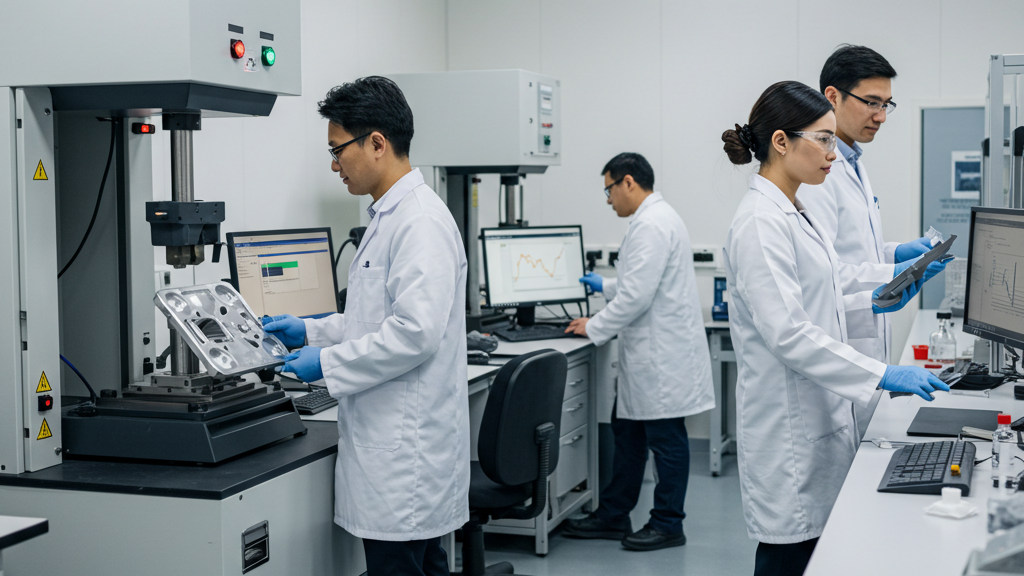
The molecular structural characteristics of polycarbonate material and the inevitable residual internal stress during the injection molding process make it easier to trigger stress cracking under specific conditions. Understanding the fundamental causes of stress cracking in polycarbonate injection molded parts requires an in-depth analysis of the material’s chemical composition, mechanical properties, and the generation and distribution patterns of stress during the molding process.
- Material Structure Characteristics: The rigid structure of polycarbonate molecular chains makes them more susceptible to cracking at stress concentration points.
- Residual Internal Stress from Molding: High-pressure shear and uneven cooling during the injection molding process tend to leave residual stress inside the PC part.
- Environmental Sensitivity: Polycarbonate is sensitive to certain chemical substances, and contact may induce environmental stress cracking.
- Poor Process Parameters: Excessively high injection pressure or excessively fast cooling rates can significantly increase the internal stress level of PC injection molded parts.
What Process and Mold Factors Affect PC Stress Cracking?
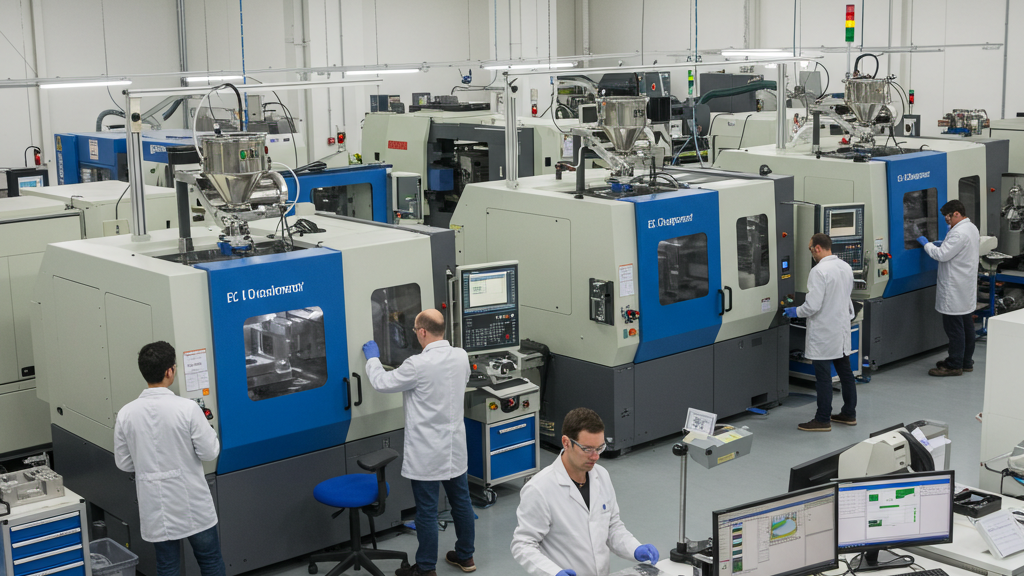
The quality and performance of polycarbonate injection molded parts are highly dependent on precise control of process parameters and rational mold design. These two directly determine melt flow, cooling and solidification, and the final product’s stress state. To explore the mechanism of stress cracking in the polycarbonate injection molding process, it is essential to analyze the role of process parameters such as injection pressure, melt temperature, and mold temperature, as well as mold design elements such as the feed system and cooling system.
- Injection Pressure and Speed: Excessive injection pressure and speed tend to introduce higher residual stress in the PC part.
- Feed System Design: An unreasonable feed system design can easily lead to uneven melt flow and stress concentration.
- Mold Temperature Control: Improper mold temperature control can cause uneven distribution of internal stress in the PC part.
- Clamping Force and Demolding: Excessive clamping force and improper demolding operations may cause stress damage to the PC part.
How to Remedy and Prevent PC Stress Cracking?
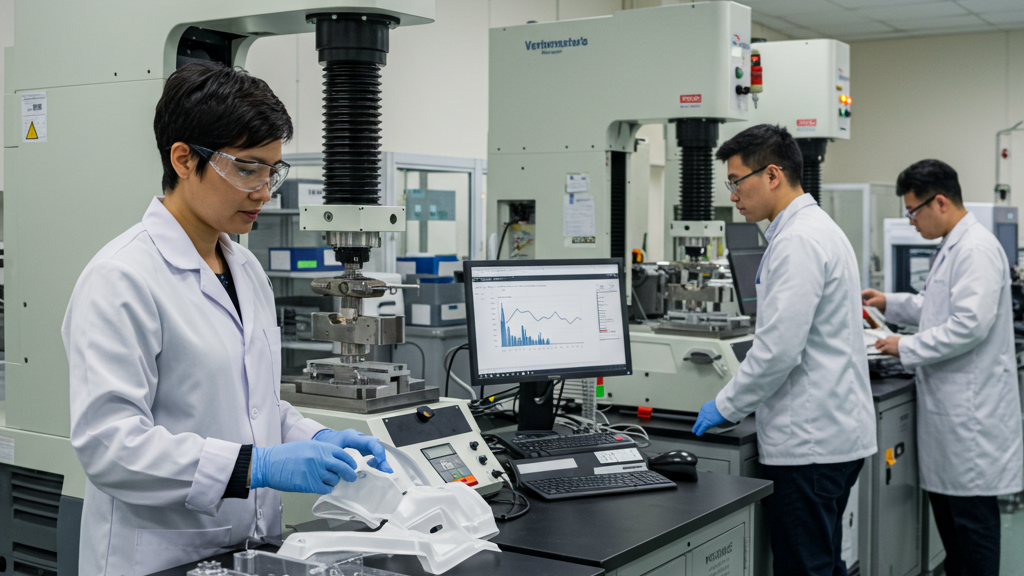
For polycarbonate injection molded parts that have already experienced stress cracking, appropriate post-treatment methods can alleviate internal stress to a certain extent. Preventing recurrence from the source requires careful evaluation and optimization of the entire injection molding process. Addressing the problem of stress cracking in polycarbonate injection molded parts requires focusing both on repairing and remedying existing defects and on improving design and optimizing processes to effectively avoid potential future risks.
- Annealing Treatment: Annealing cracked PC parts can release internal stress and prevent crack propagation.
- Optimize Product Design: Avoiding structures such as sharp corners and thin walls can reduce the risk of PC part cracking from the source.
- Adjust Injection Molding Process: Optimizing injection pressure, mold temperature, and cooling time can reduce internal stress in the PC part.
- Select Corrosion-Resistant Materials or Coatings: For specific environments, selecting appropriate PC grades or surface treatments can improve resistance to environmental stress cracking.
Prevention and control measures table
Aspect |
Measures |
Principle/Purpose |
Notes |
Material | Low Stress PC/Alloy Selection | Reduce Internal Stress/Improve Performance | Consider Chemical Resistance |
Mold Design | Optimized Gate/Uniform Cooling/Avoid Sharp Edges | Uniform Filling/Cooling/Reduce Stress Concentration | Gate Location/Multi-Circuit Cooling/Fillet |
Proper Ejection | Prevent Stress Damage During Demolding | Uniform Ejection Force | |
Process | Low Pressure & Speed | Reduce Shear Stress | Adjust Parameters |
Optimized Melt & Mold Temperature | Ensure Flow/Reduce Uneven Cooling | Consider Cycle Time | |
Extended Holding & Cooling Time | Full Solidification/Reduce Shrinkage & Stress | Avoid Excessive Pressure | |
Annealing (Post-Molding Heat Treatment) | Release & Homogenize Internal Stress | Control Temperature & Time | |
Post-Process | Avoid Incompatible Chemicals | Prevent Environmental Stress Cracking | Inform Users |
Surface Coating | Improve Chemical & Wear Resistance | Consider Adhesion | |
Part Design | Avoid Assembly Stress/Reinforcement Ribs | Reduce External Stress/Increase Rigidity | Proper Tolerances/Avoid Stress Concentration |
Systematic Prevention of PC Stress Cracking
In the long run, systematically preventing stress cracking in polycarbonate injection molded parts requires integrating material selection, process optimization, and product design. Only through this multi-pronged strategy can the long-term reliability and service life of polycarbonate injection molded parts be significantly improved.
1.Proactive Material Selection and Modification: Initially selecting low-stress sensitivity PC or modified materials is the foundation for improving long-term reliability.
2.Full-Process Process Optimization and Control: Establishing complete injection molding process specifications and strictly monitoring them reduces internal stress from the source.
3.Integrated Design and Simulation Analysis: Combining structural and process considerations, using simulation to optimize design, and reduce the risk of stress cracking.
4.Continuous Evaluation and Feedback Improvement: Establishing a monitoring and feedback mechanism, using actual data to guide improvements, and enhance long-term reliability.
Conclusion
Preventing stress cracking requires collaborative efforts in material selection, process optimization, and product design stages. Selecting low-stress PC, optimizing the injection molding process, and avoiding stress concentration structures are crucial. Continuous evaluation and feedback improvement can also enhance the long-term reliability of PC injection molded parts. A multi-pronged approach is essential to effectively reduce the risk of cracking and ensure product quality.
For expert assistance in implementing for your production needs, visit our resource center or contact us. Let’s help you scale up your manufacturing with precision and efficiency!
Post time: May-08-2025