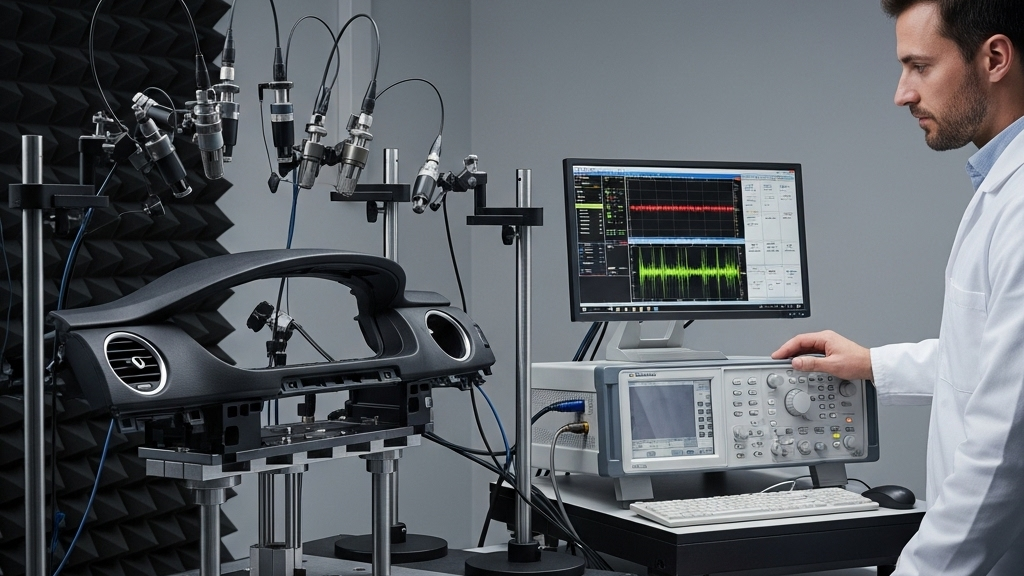
The acoustic performance and NVH (Noise, Vibration, Harshness) optimization of injection molded parts are crucial in modern manufacturing, particularly in industries like automotive and electronics, where strict acoustic requirements are expected. Using specialized fixtures for acoustic testing can significantly improve the performance of injection molded parts and reduce noise issues. This process not only enhances the product quality but also provides companies with more market competitiveness.
Why Choose Fixtures for Acoustic Testing?
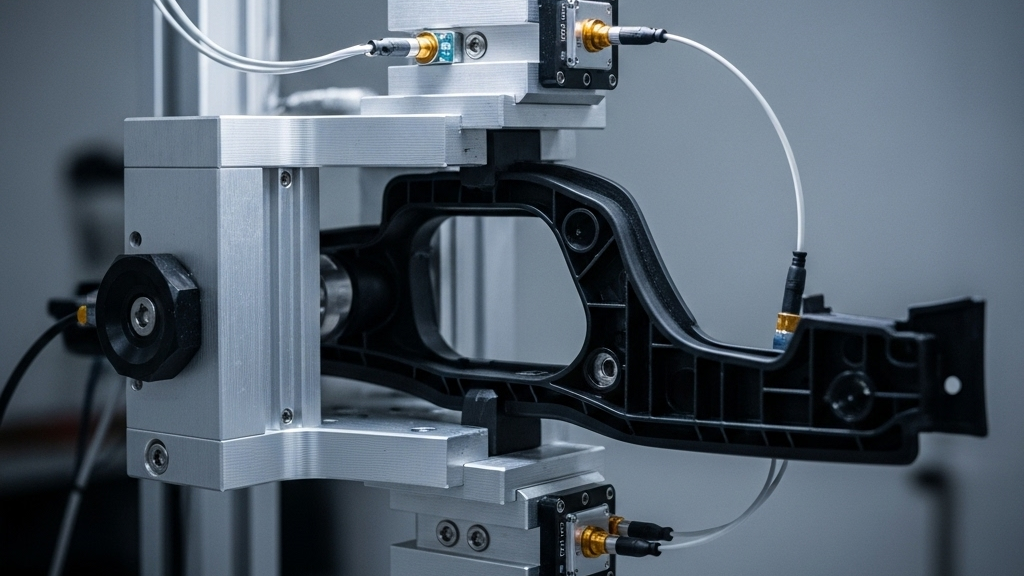
The acoustic performance of injection molded parts directly affects the product’s user experience, especially in noise-sensitive environments. Fixtures provide stable support and an accurate testing environment, which is key to successful acoustic testing.
- Precise Support: Fixtures ensure that injection molded parts stay fixed during testing, improving the accuracy of the results.
- Consistency: Standardized fixtures ensure each test is conducted under the same conditions, eliminating errors.
- Testing Sensitivity: Fixtures help detect minute vibration and noise changes, increasing testing sensitivity.
- How to Improve Fixture Design?: Fixture design significantly influences test results, and optimizing it can improve testing efficiency and accuracy.
How to Optimize the NVH Performance of Injection Molding Parts?
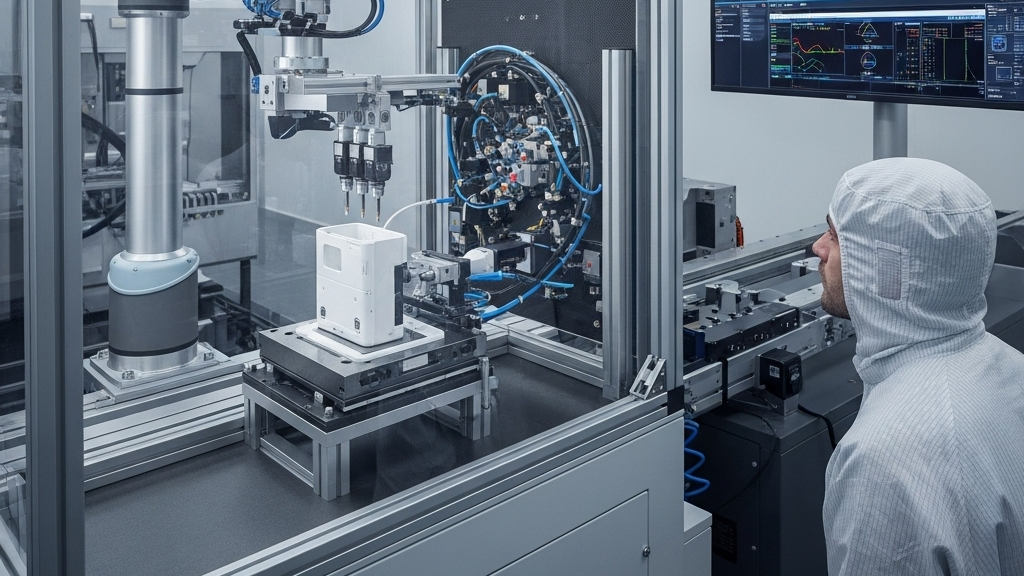
NVH optimization is key to achieving high-quality injection molded parts. Optimizing NVH performance not only reduces product noise but also extends its lifespan.
- Material Selection: Choosing the right injection molding material helps reduce vibrations and suppress noise.
- Efficient Soundproofing Technology: Using soundproof materials or improving structural design effectively reduces noise.
- Structural Design: By designing the internal structure properly, vibration paths can be minimized.
- Surface Treatment: Surface treatment technologies further reduce noise and enhance durability.
How to Implement Acoustic Testing in the Production Process?
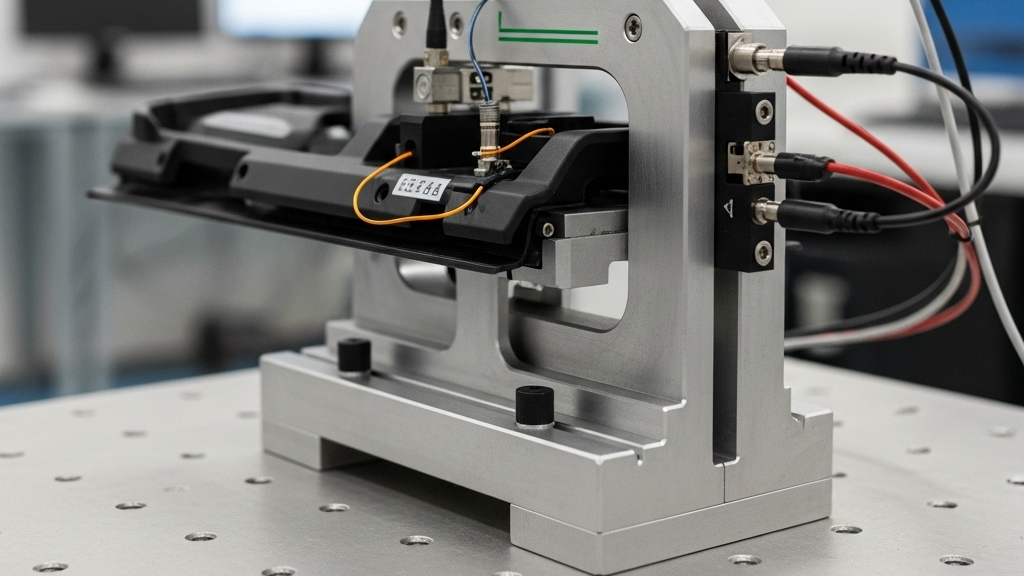
Implementing acoustic testing requires precise process control and optimization. By integrating acoustic testing into the production line, product quality can be monitored in real-time, ensuring that every product meets the expected NVH standards.
- Testing Timing: Perform tests at different stages after molding to identify potential issues.
- Real-Time Monitoring System: Install acoustic sensors for real-time data collection and analysis.
- Process Control: Strict process controls prevent unnecessary noise and vibration from occurring.
- Optimization Plan: Adjust production processes based on test results to ensure that each batch meets quality standards.
Acoustic Testing and NVH Optimization Comparison Table
Testing Phase |
Fixture Use |
Acoustic Testing Method |
NVH Optimization Method |
Results Comparison |
Test Preparation | Precise Support | Fixed Test Environment | Optimize Material Choice | Improved Accuracy |
Test Execution | Efficient Testing | High Sensitivity Sensors | Structural Design Optimization | Reduced Noise |
Data Analysis | Result Analysis | Real-Time Data Monitoring | Soundproof Treatment | Enhanced Performance |
Result Evaluation | Data Comparison | Comparative Analysis | Vibration Control Optimization | Improved Durability |
Key Factors in NVH Optimization
Choosing the right materials, designs, and testing methods is crucial in enhancing the acoustic performance and NVH optimization of injection molded parts. A long-term acoustic testing and optimization process helps products stand out in the market while enhancing a company’s product development capabilities. By regularly optimizing production processes and testing methods, companies can not only improve product competitiveness but also significantly reduce production costs.
1.Importance of Material Selection: Choosing the right material not only enhances the acoustic performance but also offers cost benefits.
2.Effects of Design Optimization: Structural and surface treatment optimizations significantly improve NVH performance.
3.Improvement of Testing Stages: Performing acoustic testing at various production stages helps monitor product quality effectively.
4.Need for Continuous Optimization: Continuous acoustic testing and process optimization help ensure long-term product quality.
Conclusion
through effective fixture support and acoustic testing, the NVH performance of injection molded parts can be significantly improved. Ongoing acoustic testing and optimization not only enhance product quality but also provide companies with more market opportunities. To stay competitive in a tough market, optimizing the acoustic performance of injection molded parts has become a key step.
For expert assistance in implementing for your production needs, visit our resource center or contact us. Let’s help you scale up your manufacturing with precision and efficiency!
Post time: Jun-26-2025