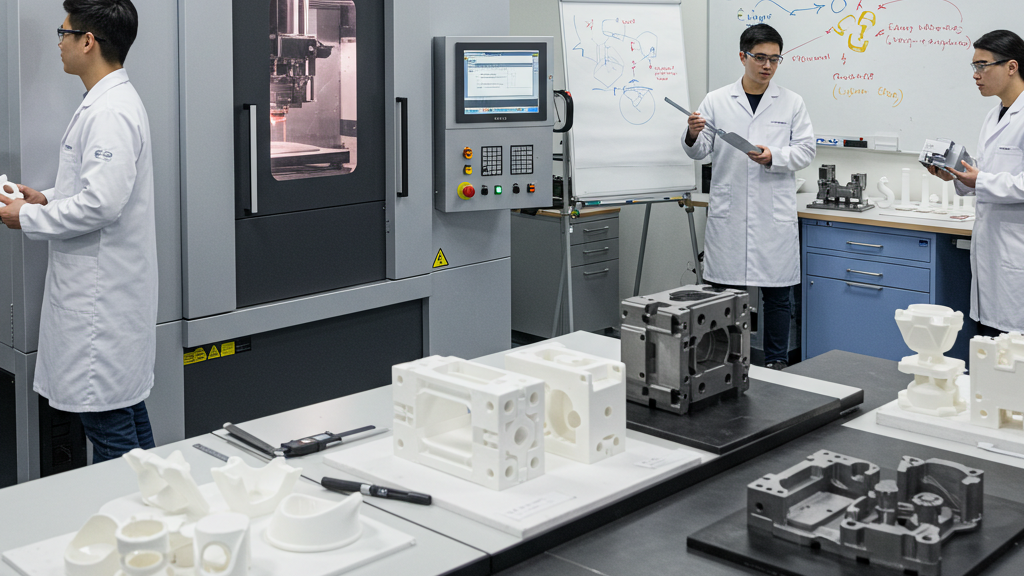
Facing rapidly changing market demands, the design iteration efficiency of injection molded products is crucial. Traditional injection mold development cycles are long, making it difficult to meet the needs of rapid iteration. Selective Laser Sintering (SLS) technology eliminates the need for molds and can directly form complex structures, providing new ideas for the design iteration of injection molded products. This article will explore how to use SLS technology to accelerate the design verification and optimization of injection molded products, shorten the development cycle, and reduce costs.
The advantages of SLS technology in the rapid iteration of injection molded products. To effectively utilize SLS, a deep understanding of its application in different design stages is required. Next, we will focus on the specific applications and technical considerations of SLS in concept verification, functional prototypes, mold optimization, and small batch production. We will explore how to combine the flexibility of SLS with the scale advantages of injection molding to achieve efficient and economical product development.
How does SLS accelerate key steps in injection molding design iteration?
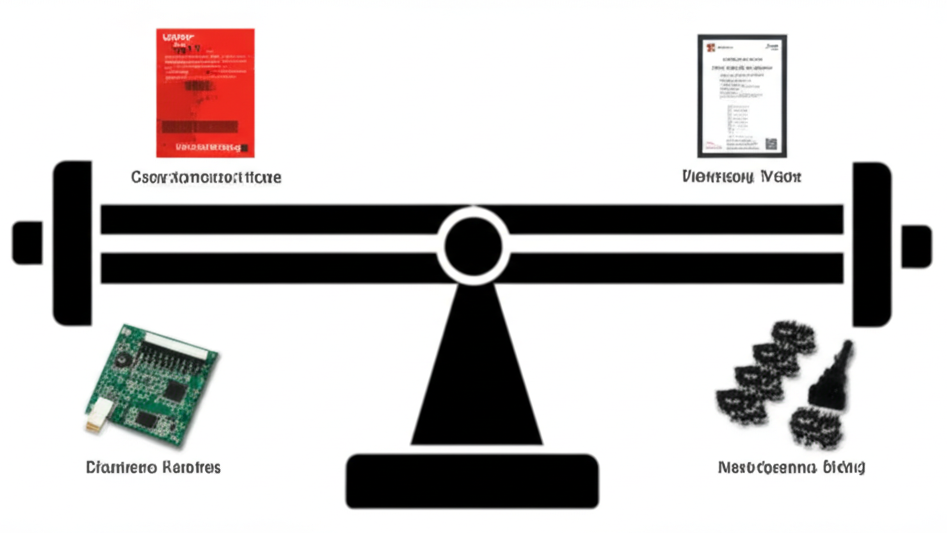
Selective Laser Sintering (SLS) technology is increasingly becoming an important driver for accelerating the design iteration of injection molded products. By cleverly deploying SLS in the key stages of the design process, the development cycle can be significantly shortened and the cost of trial and error reduced, opening up new paths for product innovation.
- Concept Verification: SLS quickly creates early models, visually assesses designs, and accelerates adjustments.
- Functional Prototyping: SLS manufactures functional prototypes, quickly tests performance, and guides design optimization.
- Mold Optimization: SLS produces mold components or verifies runners, optimizes design, and reduces mold risk.
- Small Batch Trial Production: SLS enables small batch production for market validation and final product optimization.
How do SLS prototypes guide injection mold design?
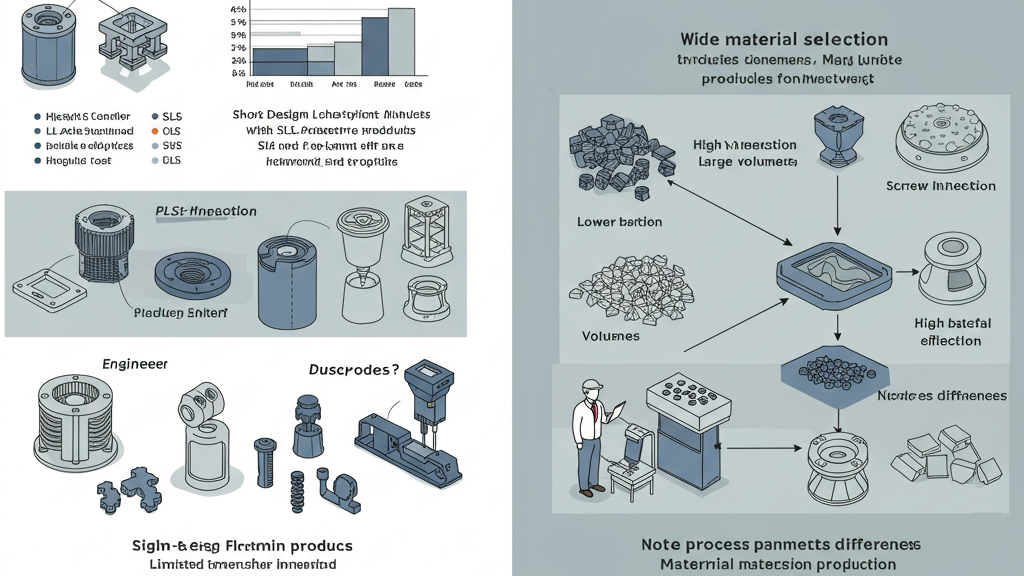
Components manufactured using SLS technology, as an important tool for design iteration, can provide early and direct feedback on product functionality, dimensional accuracy, and material suitability. This valuable data and experience gained through SLS prototypes provides a solid foundation and clear direction for the subsequent design of injection molds.
- Functional Verification: SLS prototypes directly test functionality, identify design flaws, and guide structural optimization.
- Accuracy Evaluation: Measuring the dimensions of SLS prototypes, assessing the rationality of the design, and guiding tolerance settings.
- Material Evaluation: SLS prototypes provide a preliminary assessment of material suitability, providing direction for material selection in injection molding.
- Structural Verification: SLS prototypes showcase complex structures, assess injection molding feasibility, and optimize mold design.
SLS small batch production vs. traditional mold trade-offs?
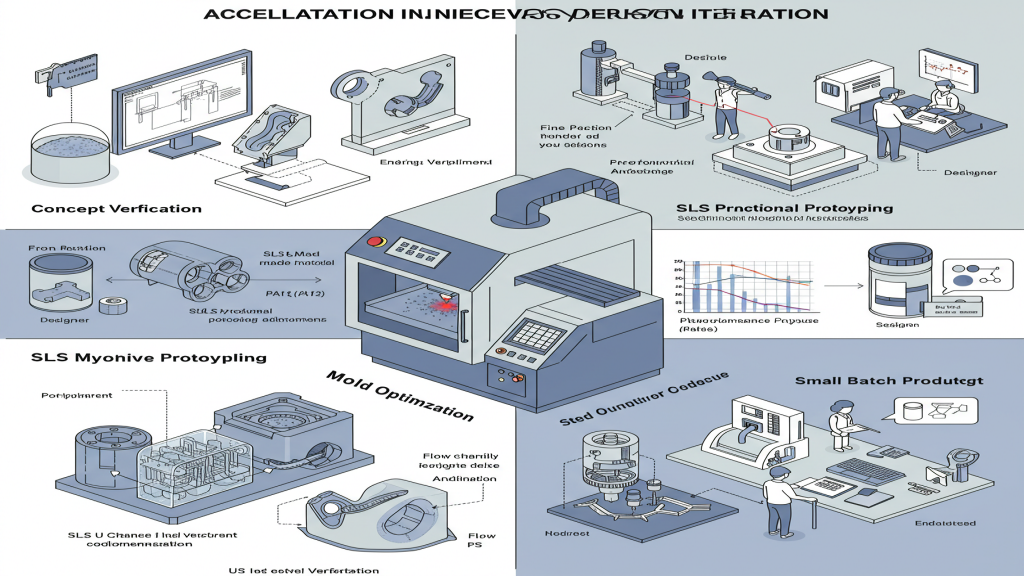
Applying SLS technology to the small batch trial production of injection molded products provides companies with a flexible and economical alternative before fully investing in expensive traditional mold manufacturing. By directly forming the required quantity of final or near-final products, SLS offers a stark contrast to traditional mold production methods in terms of time and cost-effectiveness, especially in the early stages of product development and market exploration.
- Mold Cost vs. Unit Cost: SLS saves mold costs but unit costs are high; traditional molds are more economical for mass production.
- Production Cycle vs. Batch Effect: SLS shortens production preparation cycle, but lacks the batch efficiency of traditional injection molding.
- Design Flexibility vs. Material Limitations: SLS excels in complex structures, but material selection and performance may be limited.
- Trial and Error Cost vs. Mass Production Transition: SLS reduces trial and error risk, but attention must be paid to the differences with the final injection molding process.
Rapid iterative development of mold
Key Stage |
SLS Technology Application |
Traditional Methods |
Acceleration Effect of SLS in Mold Development |
Conceptual Design Visualization & Communication | Quickly create product prototypes to intuitively display design intent, facilitating communication with mold designers | Rely on 2D drawings and verbal descriptions, leading to lower communication efficiency and potential ambiguities | Improve communication efficiency, reduce design understanding deviations, and establish a clear foundation for mold design |
Complex Structure & Parting Line Verification | Verify the feasibility of complex geometries through SLS prototypes, aiding in determining the optimal parting line position | Rely on experience-based judgment and simulation analysis, making it difficult to intuitively verify the demoldability of complex structures | Intuitively verify the feasibility of complex structures, optimize parting line design, and reduce mold manufacturing risks |
Rapid Prototyping & Testing of Mold Inserts | Quickly create prototypes of mold inserts (e.g., cooling inserts, sliders) for assembly and functional testing | Traditional machining methods for mold inserts have long cycles and high costs | Quickly verify mold structure and function, promptly identify and resolve potential issues, and shorten mold debugging time |
Cooling & Gating System Optimization Verification | Utilize SLS to create flow channel models or mold parts for rapid testing of different cooling and gating schemes | Rely on simulation analysis, making it difficult to intuitively verify the effectiveness of flow channel designs | Quickly verify the efficiency of cooling and gating schemes, optimize mold flow channel design, and improve injection molding quality and efficiency |
Early Detection & Repair Guidance of Mold Defects | SLS prototypes may reveal product design defects, allowing for avoidance or early consideration of repair solutions during mold design | Discover product design defects only after mold manufacturing is complete, leading to high mold modification costs and long cycles | Identify the impact of product design on the mold early, guide mold design to avoid defects or reserve repair solutions |
Key to Iterating Injection Molding Design with SLS
To fully realize the potential of Selective Laser Sintering (SLS) technology in accelerating the design iteration of injection molded products, design teams need to not only have a deep understanding of the principles and characteristics of SLS technology, but also master the key technical knowledge and optimization strategies to efficiently integrate it into existing design processes.
1.SLS Design and Material Understanding: Develop a deep understanding of SLS design constraints and material properties to guide prototype design.
2.SLS and Injection Molding Collaborative Process: Establish a collaborative design process that integrates SLS prototyping with injection molding production.
3.SLS Post-processing and Accuracy Calibration: Master SLS prototype post-processing and accuracy calibration to ensure validation effectiveness.
4.Efficient SLS Service Docking and Feedback: Build an efficient SLS service docking and rapid feedback mechanism to accelerate iteration.
Conclusion
Selective Laser Sintering (SLS) technology significantly accelerates the design iteration of injection molded products. Through its application in key areas such as design verification, prototyping, and mold optimization, SLS effectively shortens development cycles and reduces costs.
For expert assistance in implementing for your production needs, visit our resource center or contact us. Let’s help you scale up your manufacturing with precision and efficiency!
Post time: May-15-2025