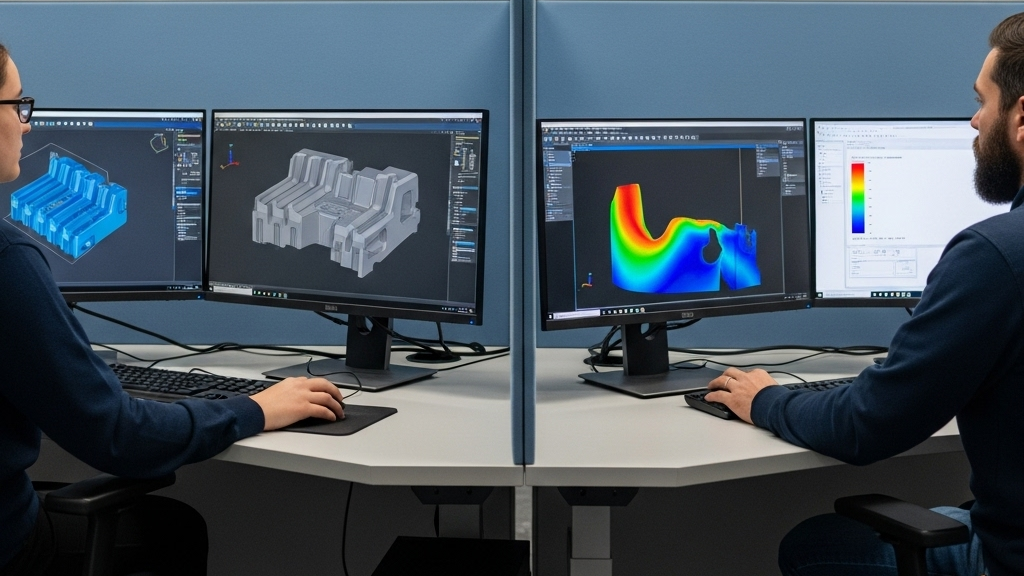
Optimizing rib layouts in injection-molded products not only strengthens the part structurally but also plays a key role in directing melt flow. Proper rib placement helps reduce short shots and fill imbalance defects.
In complex parts, the melt flow path is often influenced by internal structures, and ribs become essential guides in controlling that path. Scientific rib design enhances consistency and surface quality of molded parts.
How can ribs improve melt flow paths?
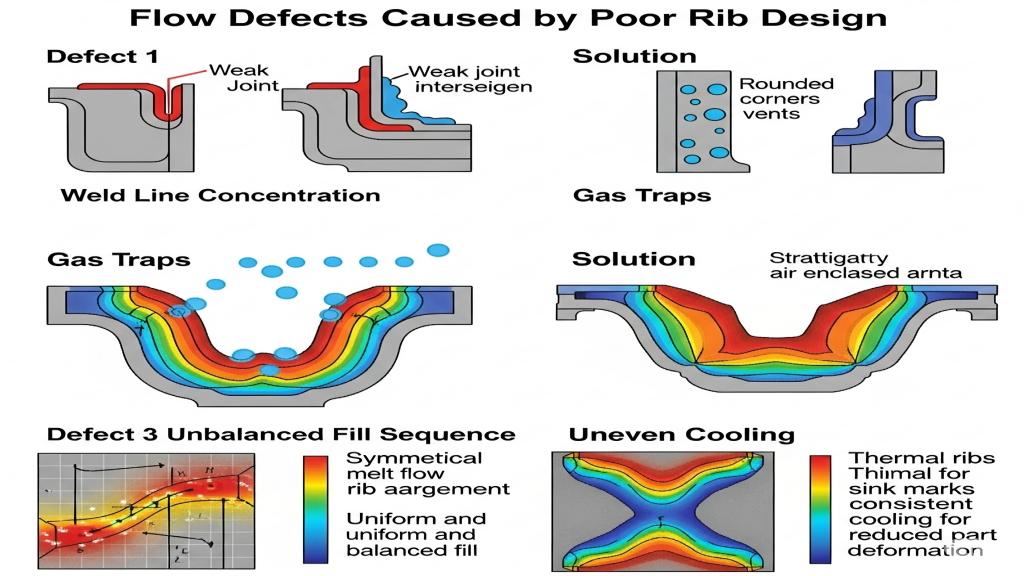
Ribs not only reinforce structure but act as “flow bridges” for the melt. The shape and position of ribs directly impact fill speed and internal pressure balance.
- Rib Width Optimization: Reducing width helps minimize local cooling delays.
- Height Ratio Control: Maintain rib height within 50–70% of wall thickness to avoid warpage.
- Symmetric Placement: Ensures balanced melt flow and avoids deviations.
- Radius Transitions: Smooth fillets prevent flow breakage and improve appearance.
What flow defects can rib layouts cause?
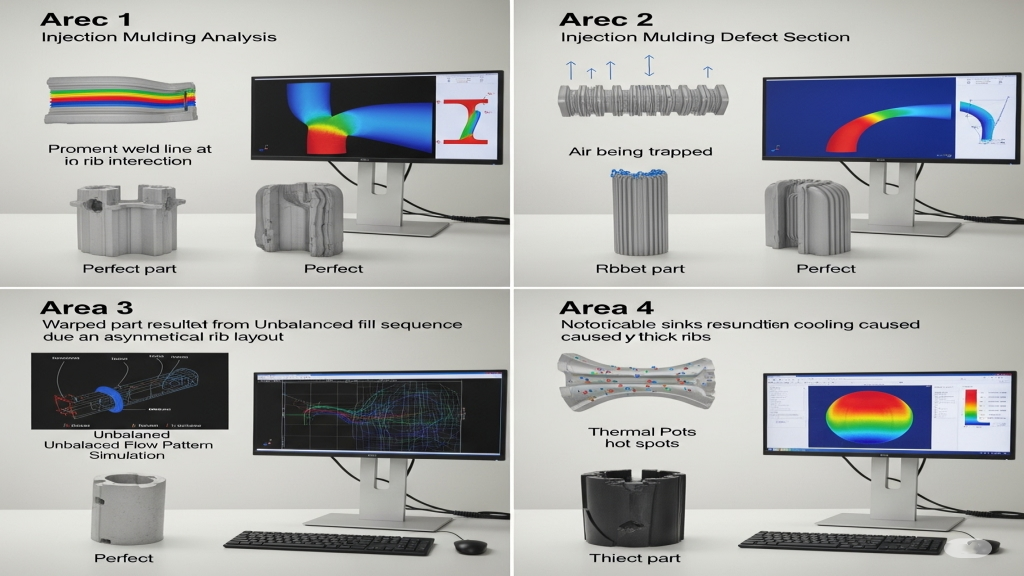
Overdesigned or poorly placed ribs can trap melt or cause shear at corners. Obstructed flow paths can lead to short shots, waviness, or splay.
- Weld Line Concentration: Common at rib intersections.
- Gas Traps: Closed rib areas need proper venting.
- Unbalanced Fill Sequence: Asymmetric ribs distort flow front.
- Uneven Cooling: Thick ribs cool slowly, causing sink marks.
How to optimize ribs without compromising strength?

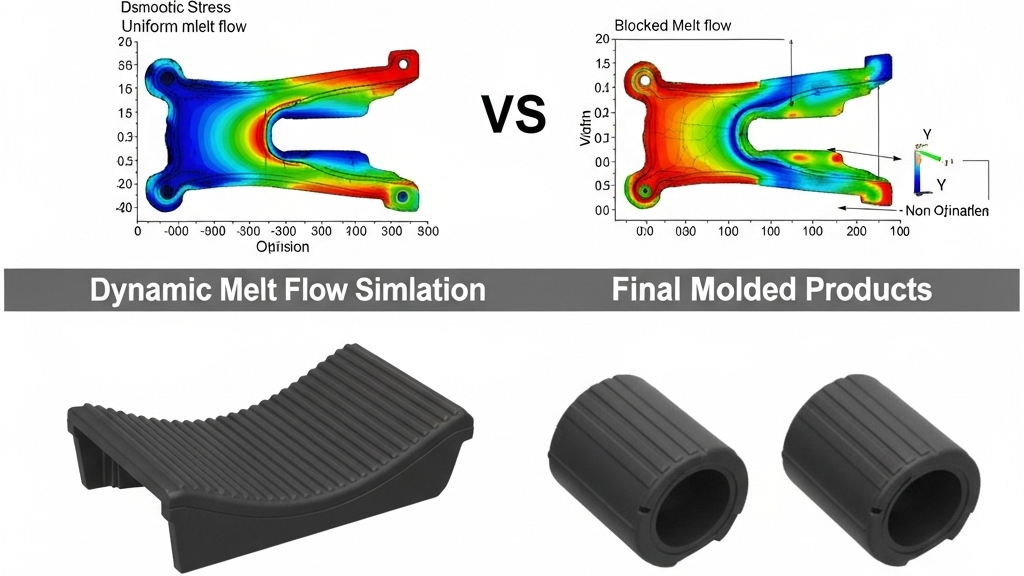
The goal is to maintain structural benefits while allowing smooth melt passage. Finding the right balance between mechanics and flow is critical.
- Functional Rib Placement: Align ribs with stress zones for dual purpose.
- Spacing Uniformity: Even rib distances enhance synchronous filling.
- Wall Transition Control: Prevent abrupt thickness changes.
- Cooling Coordination: Match ribs with mold cooling system.
Rib Designs vs Molding Performance
Rib Type |
Flow Efficiency |
Sink Risk |
Weld Line Visibility |
Warpage |
Cycle Time |
Surface Quality |
Structural Strength |
Symmetrical Ribs | High | Low | Low | Low | Short | Excellent | High |
Centralized Ribs | Medium | Medium | High | High | Medium | Fair | High |
Asymmetrical Ribs | Low | High | Medium | High | Long | Poor | Medium |
Oversized Ribs | Low | High | High | Medium | Long | Poor | Over-designed |
Does rib optimization sacrifice structural integrity?
Optimizing rib layout seeks a win-win for structure and processing. With proper simulation and design rules, strength compromise is avoidable.
1.Structural Focus Areas: Rib placement enhances key load zones.
2.Stiffness-Flow Balance: Proper thickness/height ratios maintain both.
3.Improved Process Stability: Smoother flow reduces internal stresses.
4.Visual Quality Gains: Smart rib design reduces cosmetic issues.
Conclusion
Ribs are not only structural enhancers but hidden flow directors in injection-molded parts. By optimizing rib layout, manufacturers can increase quality consistency and reduce molding defects. Well-designed ribs are the bridge between mechanical integrity and processing efficiency.
For expert assistance in implementing for your production needs, visit our resource center or contact us. Let’s help you scale up your manufacturing with precision and efficiency!
Post time: Jul-10-2025