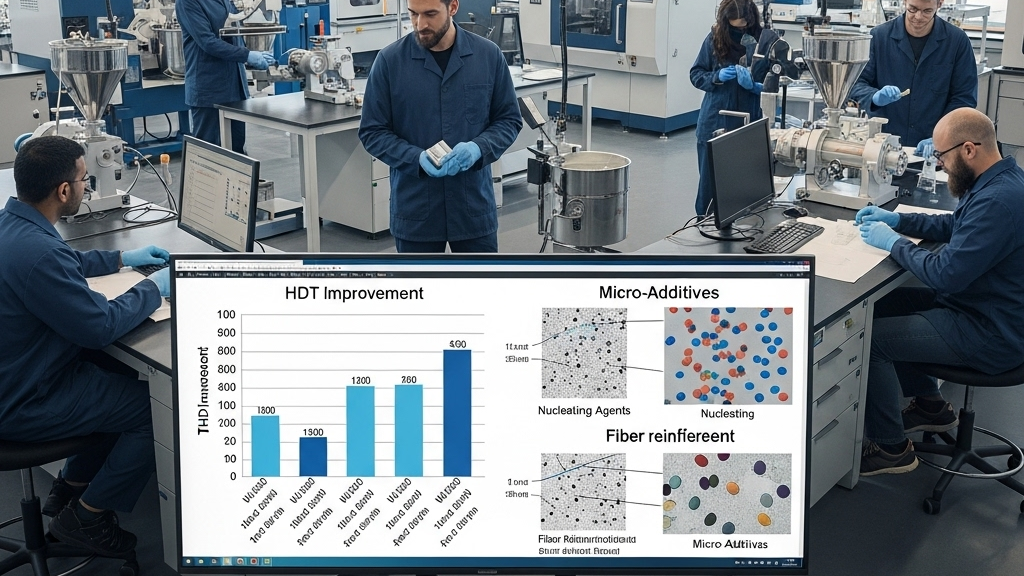
In high-temperature applications of injection-molded products, enhancing the HDT of crystalline plastics is essential to maintain stable performance. While base resin selection plays a role, the real game-changers are the micro-additives in the formula. Nucleating agents and reinforcement additives are the true “unsung heroes” behind high HDT.
These additives enhance the crystalline structure and density during processing, thereby improving both thermal and mechanical stability. Material modification is not only a technical process but also a path to cost and safety optimization. Proper use of these additives is vital for injection molding quality and efficiency.
Do nucleating agents really improve HDT?
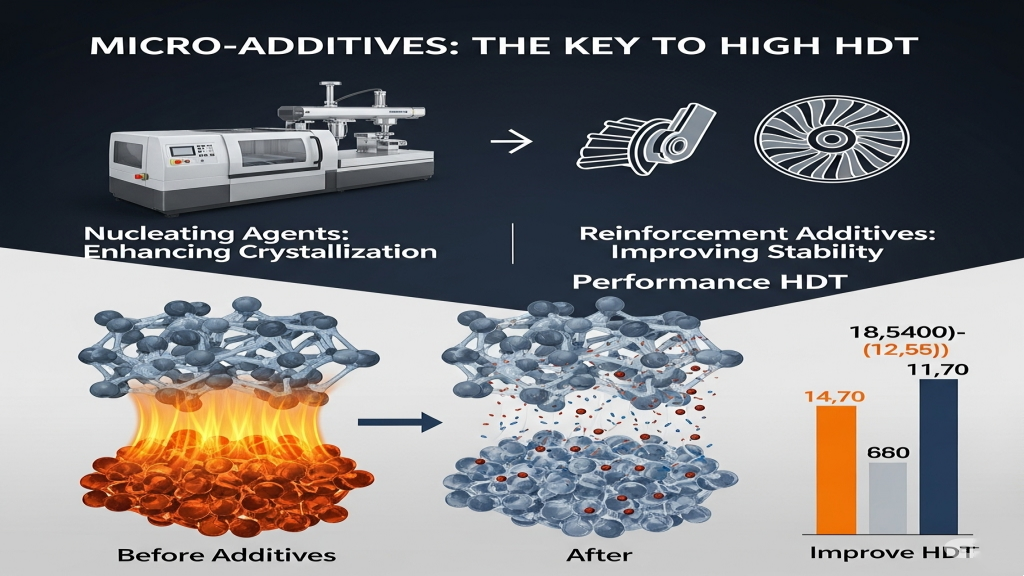
Nucleating agents accelerate and regulate the crystallization process during cooling, resulting in more compact molecular alignment. This tighter crystalline structure significantly enhances HDT. Such microstructural engineering is the key to high-performance plastic parts.
- Explore Polymer Nucleators: A full database of nucleating agents.
- HDT Improvement Cases: Practical case studies and analysis.
- Crystalline Density Boost: Improves thermal resistance significantly.
- Stress Relaxation: Reduces internal cracking under heat expansion.
Do different nucleating agents show performance gaps in real use?
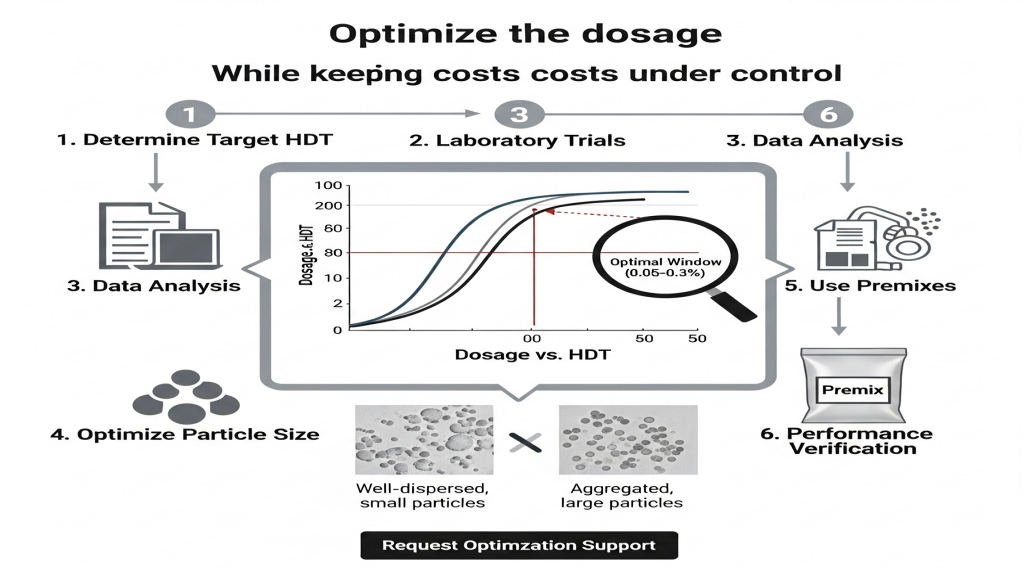
Common nucleating agents include organic salts, phosphates, metal oxides, and silicates, each reacting differently depending on the base polymer. A mismatched nucleator can even degrade overall properties instead of improving them.
- Types of Nucleating Agents: Deep dive into chemistry and compatibility.
- Target-Specific Design: Choose based on polymer type.
- Even Dispersion Is Key: Influences crystallinity and structure.
- Co-formulation Strategy: Works better when used with other enhancers.
How to optimize nucleating agent dosage without increasing cost?
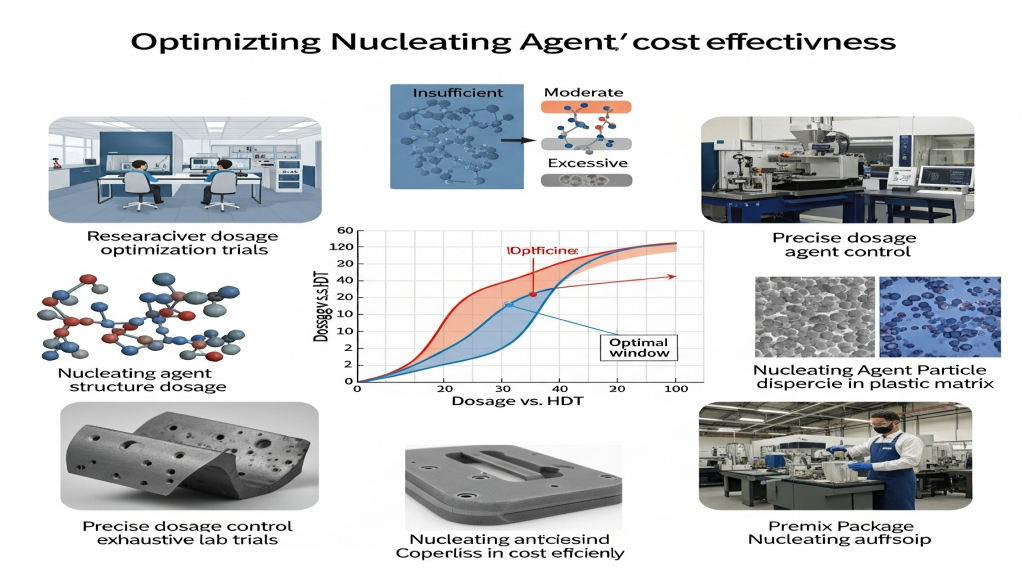
Despite their tiny proportion, nucleating agents can drastically improve HDT. Controlling dosage precisely ensures peak performance and avoids processing problems like over-crystallization. Dosage optimization through lab trials is a must in formulation design.
- Request Optimization Support: Get formulation advice.
- Optimal Window: Typically 0.05–0.3% for best effect.
- Consider Particle Size: Affects dispersion and performance.
- Premix Packages: Improve batch consistency and integration.
Performance of Four Common Nucleators on HDT
Nucleator Type |
Compatible Resins |
Recommended Dosage (%) |
HDT Gain |
Thermal Stability |
Processing Ease |
Cost Level |
Organic Phosphates | PBT, PET | 0.1–0.3 | ★★★★☆ | High | Medium | Medium |
Organic Carboxylates | PA66, POM | 0.05–0.2 | ★★★★ | Medium | High | Medium-Low |
Metal Oxides | PP, PEa | 0.1–0.3 | ★★★★★ | High | Medium | Medium |
Silico-Aluminate | PPS, LCP | 0.05–0.1 | ★★★★☆ | Very High | Low | High |
How to build your own HDT-enhancement formulation model
Through formulation validation, simulation modeling, and small-batch trials, manufacturers can identify the best nucleator type and dosage for their process. Maintaining a material database with these parameters is critical for reproducibility and quality control.
1.Crystalline Simulation: Compare effects of different agents on structure.
2.Formula Control: Maintain additive ratios across batches.
3.Thermal Field Mapping: Evaluate temperature distribution and cooling.
4.Real Product Testing: Use actual HDT testing for validation.
Conclusion
Enhancing HDT in crystalline plastics is less about the resin itself and more about the fine-tuned control of microstructure through additives. The right choice and proportion of these “unsung heroes” such as nucleators and enhancers ultimately determine thermal resistance. Only through precise additive control can performance and cost be truly balanced.
For expert assistance in implementing for your production needs, visit our resource center or contact us. Let’s help you scale up your manufacturing with precision and efficiency!
Post time: Jun-27-2025