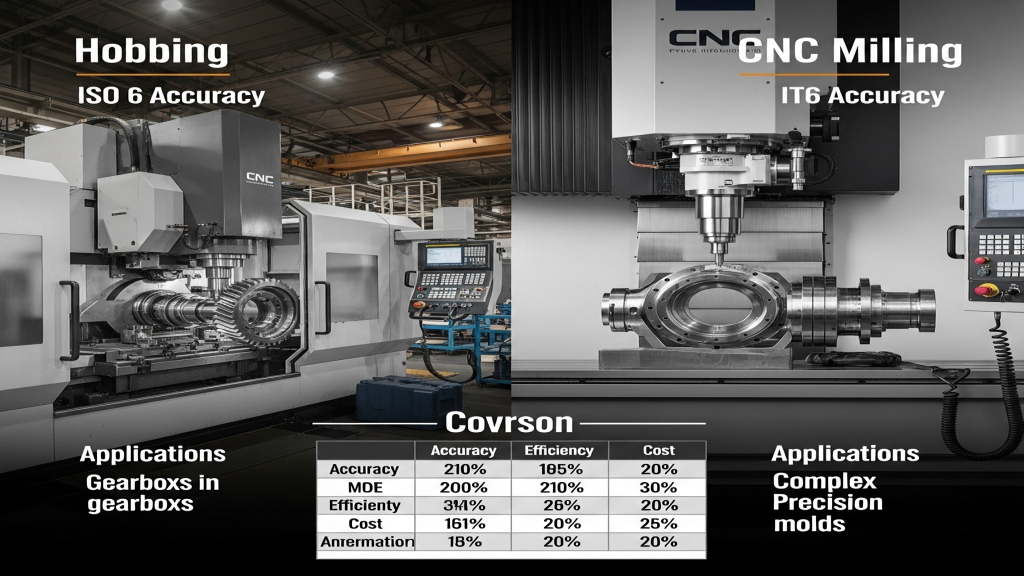
Hobbing and CNC milling are two common processing methods in modern manufacturing. These two processes differ in terms of precision, production efficiency, and application scope. As technology continues to develop, the scope of application for these two processes has gradually expanded and they play different roles in various manufacturing environments.
What are the main differences between hobbing and CNC milling?
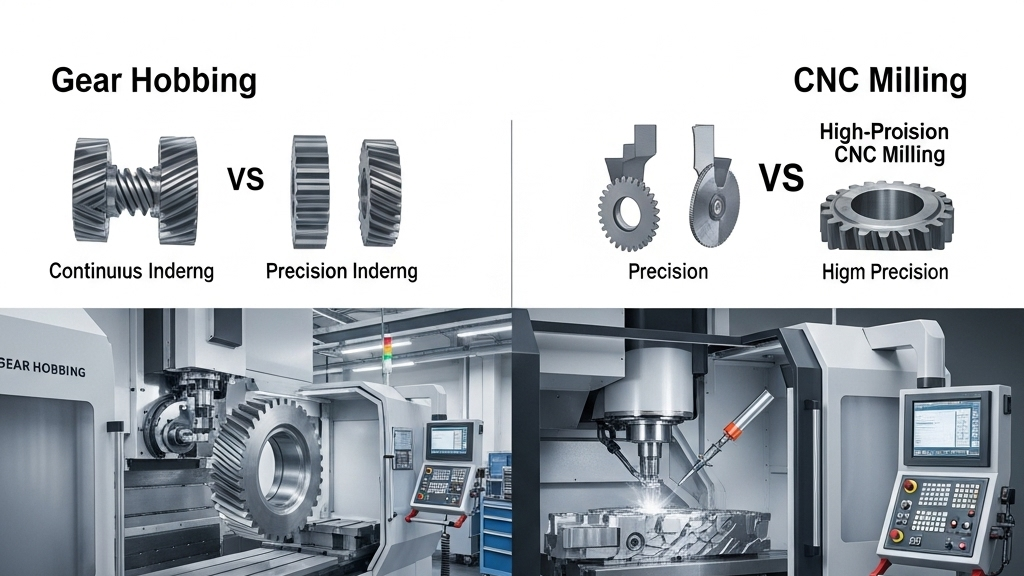
Hobbing and CNC milling have significant differences in terms of manufacturing precision, surface quality, and processing speed. Hobbing is more suitable for mass production of gears, while CNC milling is used for high-precision and complex parts manufacturing. The main difference between the two lies in the processing methods and the types of products they are suitable for.
- Efficiency advantage of hobbing: Hobbing significantly improves production efficiency, especially suitable for mass production.
- Precision advantage of CNC milling: CNC milling is better suited for parts requiring high precision and complex geometries.
- Application range of hobbing: Application range of hobbing is mainly focused on gears and mechanical parts.
- Application range of CNC milling: Advantages of CNC milling lie in its ability to process complex surfaces and intricate details.
How do the cost advantages of these two processes differ?
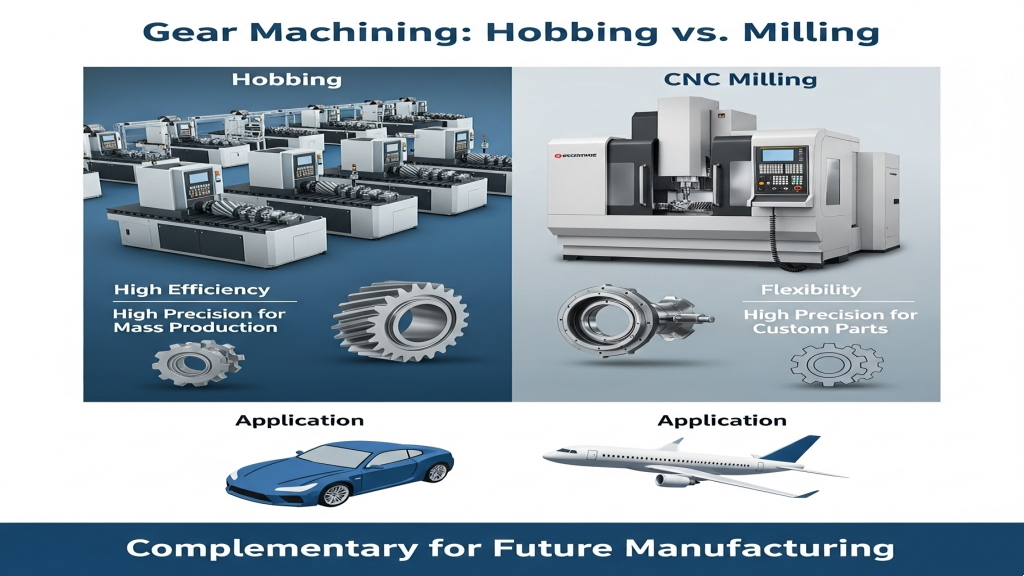
Hobbing typically has a lower unit production cost than CNC milling, especially in large-scale production. However, the flexibility and precision of CNC milling usually mean higher costs. When choosing the process, production quantity and precision requirements are key factors in determining the cost.
- Cost benefits of hobbing: Hobbing has a lower unit cost and is suitable for mass production.
- High-cost benefits of CNC milling: Although CNC milling is more expensive per unit, it is suitable for small batch high-precision processing.
- How to choose the appropriate processing method: Choosing the right processing method involves considering the complexity of the part and production scale.
- Impact of production scale: Choosing the right processing method based on the production scale can effectively reduce overall costs.
How can the efficiency of these two processes be improved through optimization?
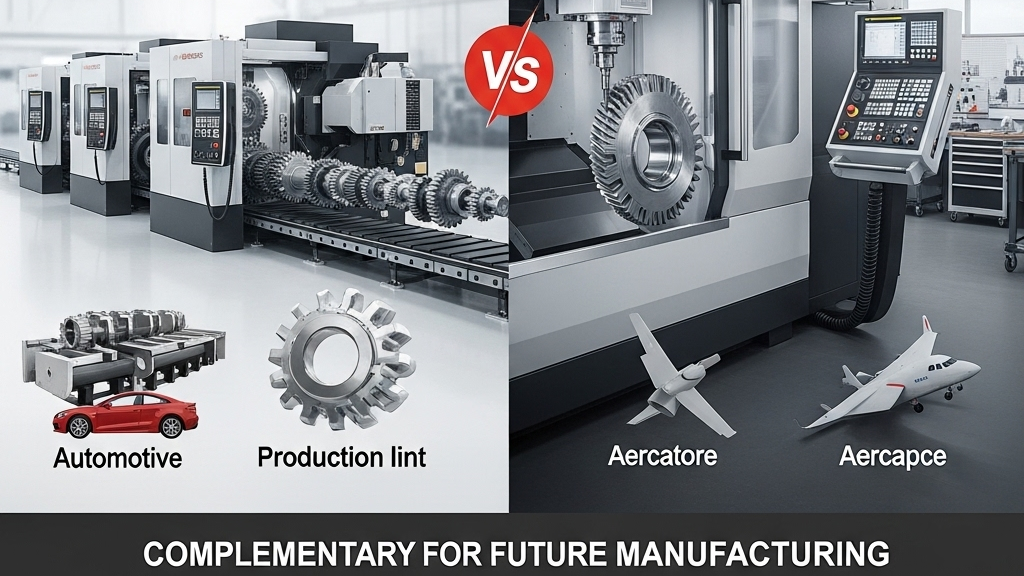
Improving production efficiency typically relies on process optimization and proper equipment selection. By properly planning production flows and optimizing process parameters, the effectiveness of both hobbing and CNC milling can be maximized, thereby improving overall production efficiency.
- Optimization of hobbing: Improving tool quality and enhancing automation levels can increase the efficiency of hobbing.
- Efficiency improvements in CNC milling: Using multi-axis CNC machines and advanced cutting techniques can boost CNC milling production efficiency.
- Key factors in optimizing production processes: Optimizing production processes can reduce costs while enhancing efficiency.
- Impact of automation on efficiency: Automation in equipment reduces human intervention, speeding up production and improving precision.
Comparison of Hobbing and CNC Milling Processes
Comparison Item |
Hobbing |
CNC Milling |
Application Range |
Production Efficiency |
Precision | Lower | Higher | Gears, mechanical parts | Lower |
Processing Speed | Faster | Slower | Complex parts | Higher |
Cost | Lower | Higher | Mass production | Higher |
Flexibility | Lower | Higher | Precision processing | Lower |
Advantages and Disadvantages of Hobbing
Hobbing is a traditional gear processing method with high production efficiency, but it has limitations in precision and flexibility. Despite this, it remains an irreplaceable process in mass production.
1.Efficient production mode: Hobbing can produce large quantities of identical parts in a short period.
2.Challenges in precision: Hobbing is suitable for mass production, but not for parts with high precision requirements.
3.Impact of the production environment: Hobbing is primarily used in automated production environments and is suitable for large-scale factories.
4.Market demand guidance: As the industry evolves, the application scenarios for hobbing continue to expand.
Conclusion
Both hobbing and CNC milling have their respective advantages, and selecting the appropriate process based on specific production needs is crucial. By optimizing the production processes of both, production efficiency can be significantly improved while reducing costs.
For expert assistance in implementing for your production needs, visit our resource center or contact us. Let’s help you scale up your manufacturing with precision and efficiency!
Post time: Jul-09-2025