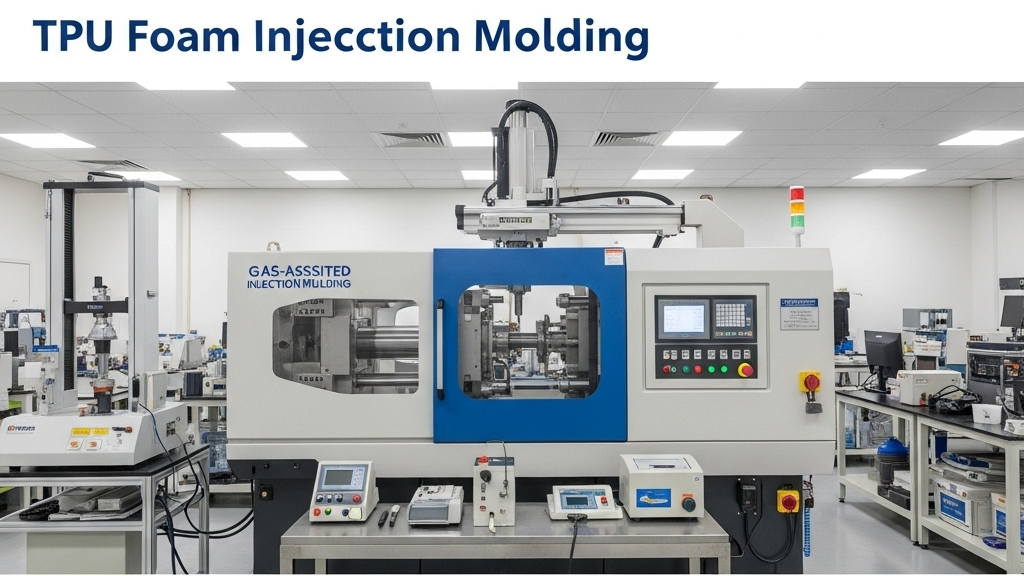
Lightweighting and high performance are important directions in modern materials manufacturing. Thermoplastic polyurethane elastomer (TPU) has attracted much attention due to its excellent properties. TPU foam injection molding technology reduces the density of products by introducing a foaming agent, demonstrating multiple advantages in performance, cost, and design. A deep understanding of these advantages is crucial for industrial upgrading.
It is evident that TPU foam injection molding has significant advantages in lightweighting, performance improvement, and cost optimization. However, fully leveraging these advantages requires mastering key elements such as process control, material selection, and mold design. Next, we will focus on the application value of TPU foam injection molding technology in various fields and its potential for product innovation and industrial upgrading.
How does foaming enhance TPU performance?
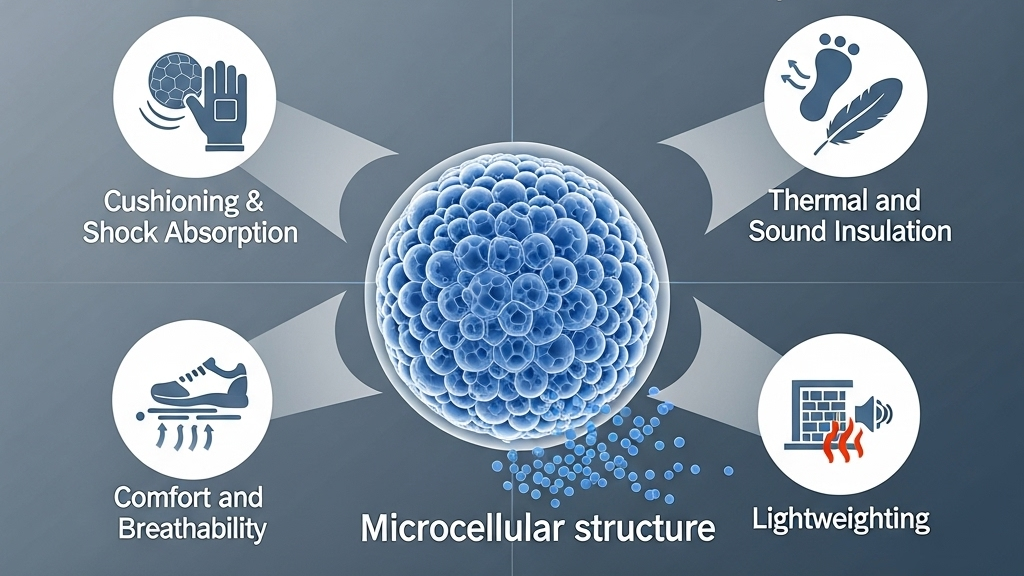
Compared with traditional processes, the application of foaming technology not only reduces the density of TPU products but also endows the material with new functional performances in terms of energy absorption characteristics, breathability, and tactile comfort.
- Lightweighting: Foaming technology introduces a microcellular structure, which significantly reduces the density of TPU products, achieving lightweighting.
- Cushioning and Shock Absorption: The microcellular structure gives foamed TPU excellent energy absorption capabilities, providing superior cushioning and shock absorption performance.
- Comfort and Breathability: The pores formed by foaming improve the breathability of the material and bring a softer touch, enhancing comfort.
- Thermal and Sound Insulation: Internal microcells effectively hinder heat and sound wave transmission, enhancing the thermal and sound insulation performance of TPU products.
How does foaming optimize cost efficiency?
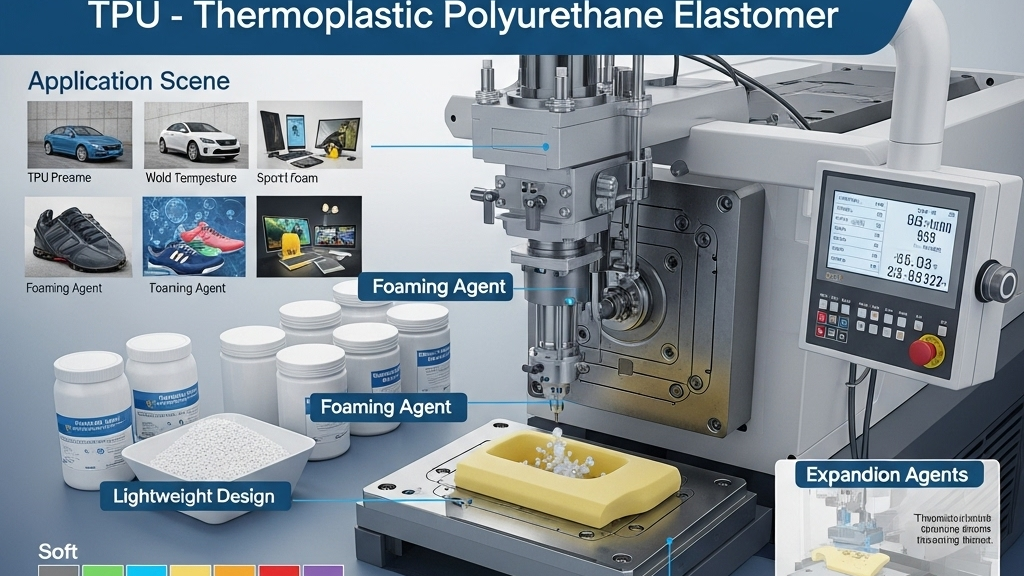
Through the foaming process, a larger volume of products can be manufactured from a unit weight of TPU resin. At the same time, a reasonable foaming process can also shorten the molding cycle to a certain extent, thereby achieving optimization in both material cost and production efficiency.
- Material Costs: Foaming technology effectively reduces raw material costs by reducing the amount of TPU resin used.
- Production Efficiency: A well-designed foaming process can, in some cases, shorten the molding cycle and increase production efficiency.
- Transportation Costs: Lightweight foamed products reduce transportation weight, thereby reducing transportation costs and energy consumption.
- Post-Processing: Some foaming processes can reduce secondary processing or assembly steps, lowering production costs.
How does foaming expand design flexibility?
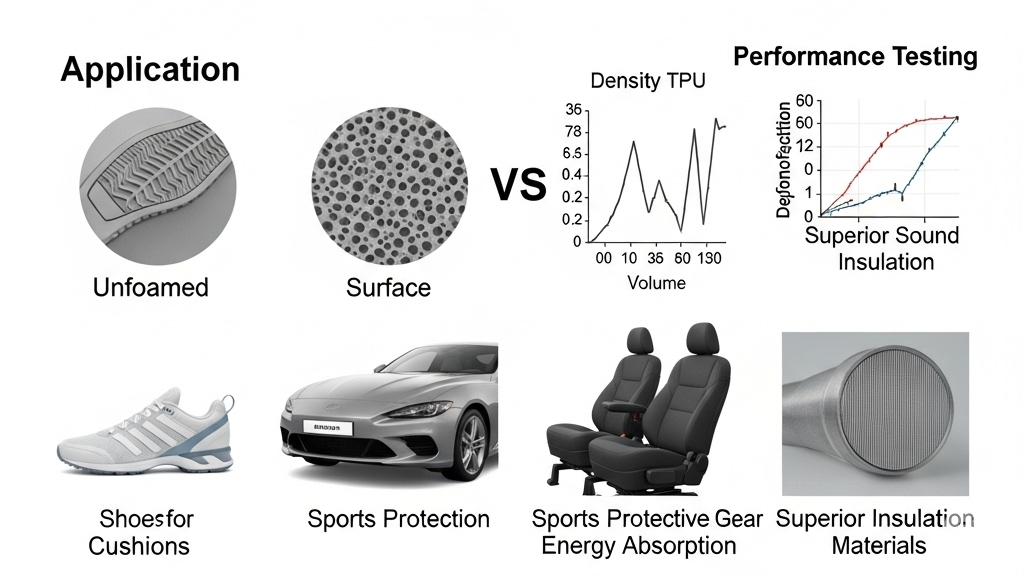
By precisely controlling the foaming process, designers are able to create complex internal structures and multiple functional attributes in a single TPU component that were previously difficult to achieve, thereby improving product performance and application range.
- Complex Shapes: The foaming process enhances the flowability of TPU, enabling the design of more complex geometric shapes.
- Functional Customization: By controlling local foaming, different densities and hardnesses can be achieved in the same product, integrating multiple functions.
- Material Integration: Foamed TPU can be combined with other materials or components to achieve more complex functional integration.
- Lightweight Optimization: By optimizing the foaming structure and combining structural design, a balance between lightweighting and structural performance can be achieved.
Cost and efficiency
Advantage Category |
Specific Manifestation |
Potential Benefits |
Material Cost | Reduced Resin Usage: Microcellular structure allows more volume per unit weight of TPU | Direct reduction in raw material procurement costs |
Lightweight Design: Lower product weight reduces transportation costs and energy consumption | Lower logistics expenses, aligns with environmental trends | |
Production Efficiency | Shorter Molding Cycle (in some applications): Improved melt flow, faster mold filling | Increased single-machine output, shorter lead times |
Reduced Post-Processing: One-step molding of complex structures or functional parts | Lower labor costs and equipment investment, simplified production flow | |
Overall Benefits | Improved Resource Utilization: More efficient use of TPU material, less waste | Reduced overall cost per product, enhanced business competitiveness |
Optimized Inventory Management: Lighter products may require less storage space | Lower warehousing costs, improved operational efficiency |
Environmental Significance of Foaming
From the perspective of environmental protection and sustainable development, the introduction of TPU foam injection molding technology demonstrates multiple positive implications. By optimizing material usage and simplifying production processes, this technology helps reduce resource consumption and environmental load.
1.Resource Conservation: Foaming technology reduces the amount of raw materials used, lowering the consumption of finite resources.
2.Reduced Energy Consumption: Lightweight foamed products contribute to reducing energy consumption and carbon emissions in application fields.
3.Pollution Reduction: Simplifying production processes reduces energy consumption and potential pollutant emissions.
4.Facilitates Recycling: Foamed TPU made from a single material is theoretically more conducive to future recycling and reuse.
Conclusion
TPU foam injection molding technology offers significant advantages. Lightweighting reduces energy consumption and enhances properties such as cushioning. Cost optimization and increased efficiency bring economic benefits, while design flexibility promotes innovation. This technology helps conserve resources, reduce pollution, and facilitates material recycling. TPU foam injection molding is a crucial technology for driving industrial upgrading and sustainable development.
For expert assistance in implementing for your production needs, visit our resource center or contact us. Let’s help you scale up your manufacturing with precision and efficiency!
Post time: May-20-2025