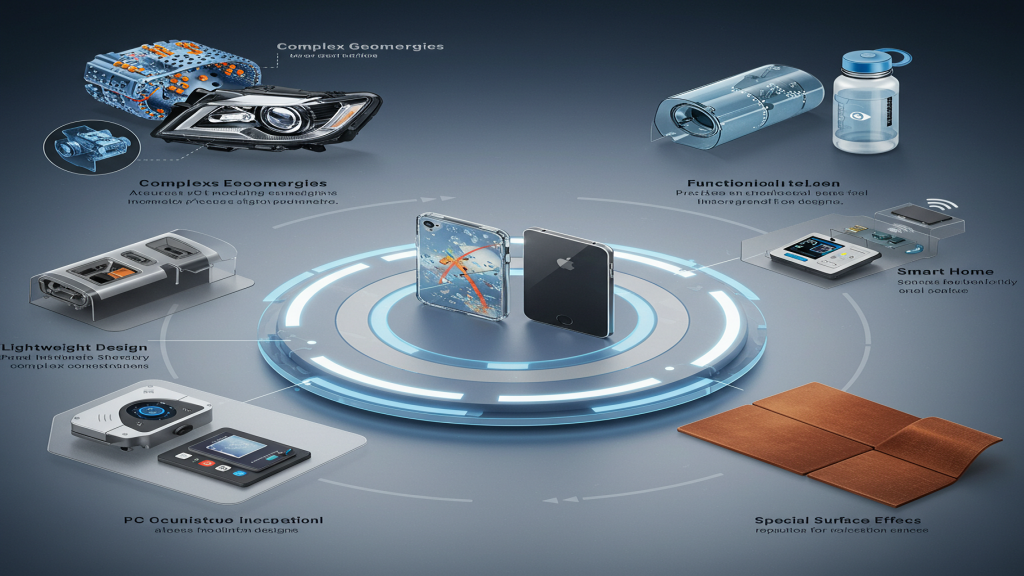
Polycarbonate is widely used for its excellent performance. However, its rheological properties—flow and deformation characteristics—are becoming crucial for commercial value. Understanding and controlling the rheological properties of polycarbonate can optimize processing, improve efficiency, and drive product innovation. This article will analyze its commercial potential and practical application value from a professional perspective.
Polycarbonate’s excellent rheological properties lay the foundation for efficient processing. Rheological parameters such as melt viscosity and shear sensitivity directly affect the quality of processes like injection molding and extrusion. Next, we will explore the specific role of rheological properties in different processing stages and how controlling rheological behavior can reduce costs, increase efficiency, and gain a commercial advantage.
How does rheology affect the processing and efficiency of polycarbonate?
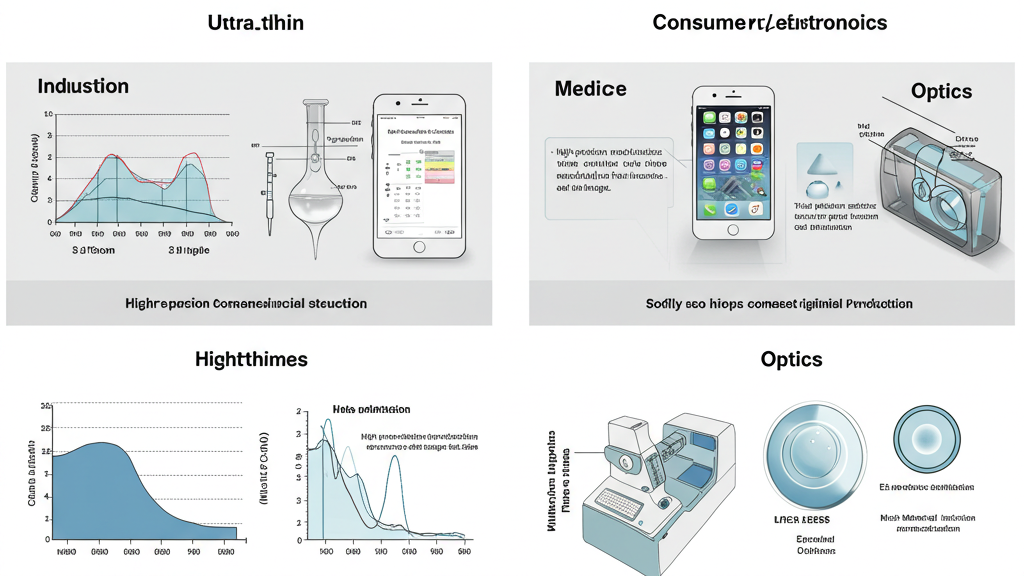
The successful application of polycarbonate largely depends on its flow behavior in the molten state. Key rheological characteristics such as melt viscosity and shear thinning directly determine the polymer’s ability to fill the mold, the required injection pressure, and the appearance quality of the final product.
- Melt Viscosity: Melt viscosity directly determines the flow resistance of polycarbonate, affecting injection pressure and filling speed.
- Shear Thinning: Shear thinning enables polycarbonate to flow more easily and fill the mold during processing.
- Elasticity: The elasticity of the melt affects the behavior of polycarbonate after it leaves the mold and the surface quality of the final product.
- Temperature Sensitivity: The viscosity of polycarbonate changes significantly with temperature, making precise temperature control crucial for processing.
How to Reduce Processing Costs and Shorten Cycle Times?
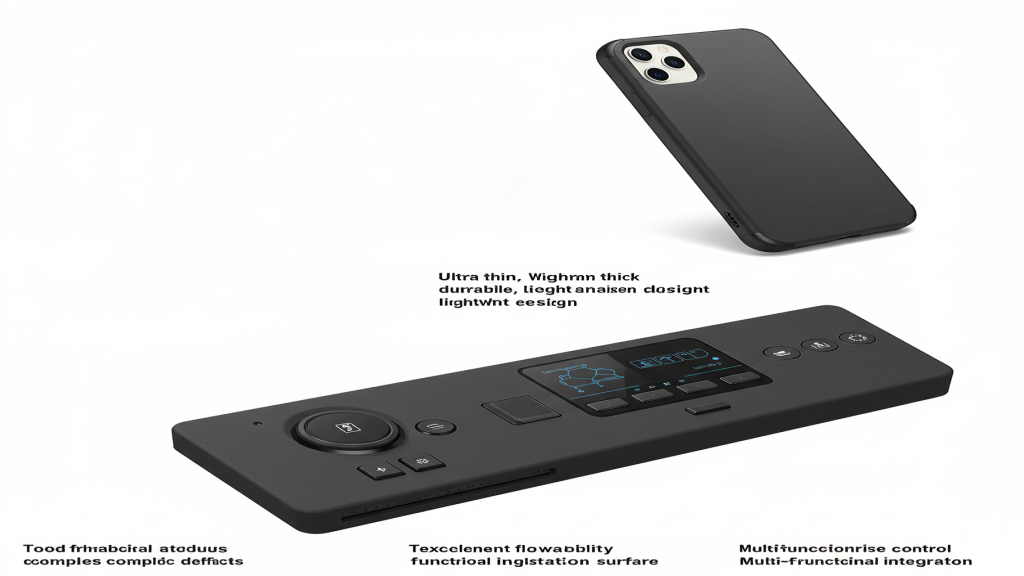
By precisely controlling the rheological behavior of polycarbonate, production processes can be significantly optimized in molding processes such as injection molding and extrusion. Properly adjusting properties such as melt viscosity and shear thinning can effectively reduce energy consumption, minimize material waste, and significantly shorten the solidification and cooling times of products.
- Reduce Injection/Extrusion Pressure and Energy Consumption: Optimizing rheological properties can reduce the pressure required for processing, thereby reducing energy consumption.
- Shorten Filling and Cooling Times and Increase Production Efficiency: Improving flowability can accelerate filling and cooling, increasing production efficiency.
- Reduce Flash and Overflow and Decrease Material Loss: Precisely controlling rheological properties helps reduce waste and improve material utilization.
- Optimize Mold Design and Reduce Trial Molding and Adjustment Times: A deep understanding of rheological characteristics can optimize mold design and shorten development time.
How does rheology drive product innovation in polycarbonate?
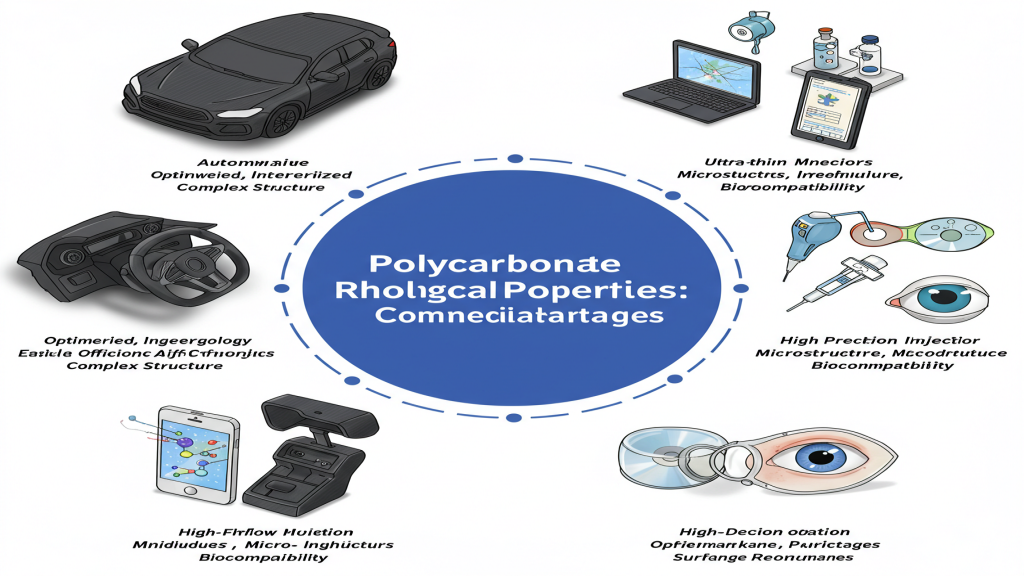
The excellent rheological characteristics of polycarbonate bring unprecedented flexibility to product design. By precisely controlling its flow behavior in the molten state, engineers can overcome the limitations of traditional manufacturing, creating innovative parts with more complex structures, thinner walls, and even integrated special functionalities.
- Complex Geometries and Microstructures: Good flowability enables polycarbonate to form complex and intricate structures.
- Thinner Walls and Lightweight Design: Excellent flowability helps manufacture thinner and lighter polycarbonate components.
- Integration of Multiple Functions into One: Precise control of rheological properties enables multifunctional integrated product designs.
- Special Surface Textures and Optical Effects: Rheology affects surface replication ability, enabling special appearance effects.
Rheological characteristics of polycarbonate
Rheological Property |
Description |
Main Influencing Factors |
Impact on Processing |
Melt Viscosity | The ability of molten polycarbonate to resist flow, usually measured at a specific temperature and shear rate. | Temperature, Molecular Weight, Shear Rate, Additives | Affects injection/extrusion pressure, filling speed, flowability, energy consumption |
Shear Thinning | The extent to which melt viscosity decreases with increasing shear rate. | Molecular Weight Distribution, Long-Chain Branching | Affects mold filling capability, part surface quality, ability to fill complex structures |
Elasticity (First Normal Stress Difference) | The elastic stress generated by the melt during shear flow, reflecting the tendency of the melt to recover its original shape after deformation. | Molecular Weight, Molecular Weight Distribution, Long-Chain Branching, Temperature | Affects die swell, melt fracture, part dimensional stability |
Temperature Sensitivity | The extent to which melt viscosity changes with temperature. | Polymer Structure | Affects processing window, flow control, stability of part quality |
Creep and Stress Relaxation | Deformation over time under constant stress (creep) and decrease in stress over time under constant deformation (stress relaxation). | Molecular Weight, Crosslinking Degree, Temperature | Affects long-term dimensional stability, internal stress, post-shrinkage |
Orientation and Anisotropy | The alignment direction of molecular chains during melt flow and the resulting property differences. | Flow Field, Cooling Rate | Affects part mechanical strength, optical properties, anisotropy of shrinkage |
Commercial benefits of rheological properties of polycarbonate
The commercial benefits of polycarbonate rheology are clearly demonstrated in several industries. High-flow polycarbonate can precisely replicate the mold surface, producing high-definition lenses and optical discs, thereby enhancing product performance. These examples fully demonstrate the significant commercial value of polycarbonate rheology in improving product performance, optimizing production efficiency, and driving innovation.
1.Automotive Industry: Optimized rheology of polycarbonate helps manufacture lightweight, integrated, and complex automotive interior components.
2.Consumer Electronics: High-flow polycarbonate enables efficient and precise production of ultra-thin and lightweight electronic device housings.
3.Medical Devices: Good flowability enables polycarbonate to manufacture high-precision micro-medical device structures.
4.Optics: Excellent flowability and replication ability make polycarbonate suitable for the manufacture of high-precision optical components.
Conclusion
For expert assistance in implementing for your production needs, visit our resource center or contact us. Let’s help you scale up your manufacturing with precision and efficiency!
The rheology of polycarbonate is key to translating into commercial benefits. Precise control of its rheological properties enables cost reduction, efficiency improvement, and cycle time reduction in processing. More importantly, rheology empowers product innovation, enabling the manufacture of more complex, thinner, and multifunctional components. Examples in industries such as automotive, electronics, medical, and optics clearly demonstrate its value in improving performance, optimizing production, and driving innovation.
Post time: Apr-29-2025