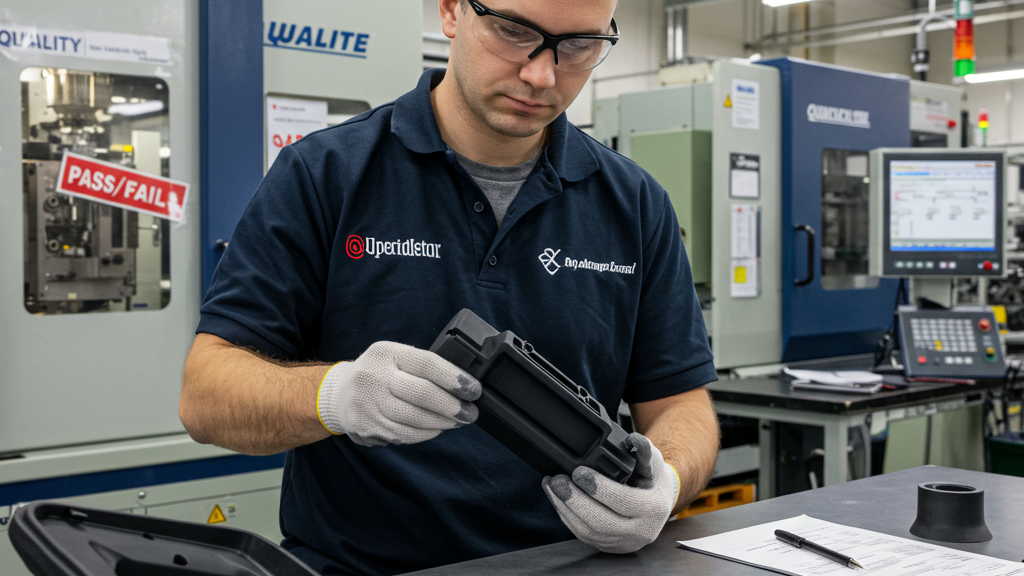
Overmolding is a key process to enhance product value, and material selection is critical. For black polypropylene (PP), not all types are suitable for overmolding. This article will focus on which black PPs can be used in overmolding and analyze its technical considerations and commercial value. Provide professional reference for your product innovation.
Overmolding has special requirements for the performance of black PP, such as adhesion and durability with the overmolding material. Differently modified black PPs, such as reinforced or filled PP, have different performance characteristics. Which special materials can balance coloring and injection molding performance? Next, we will analyze the characteristics and application advantages of different black PPs to help you choose the best material and enhance the market competitiveness of your products.
Why are not all black PPs suitable for overmolding?
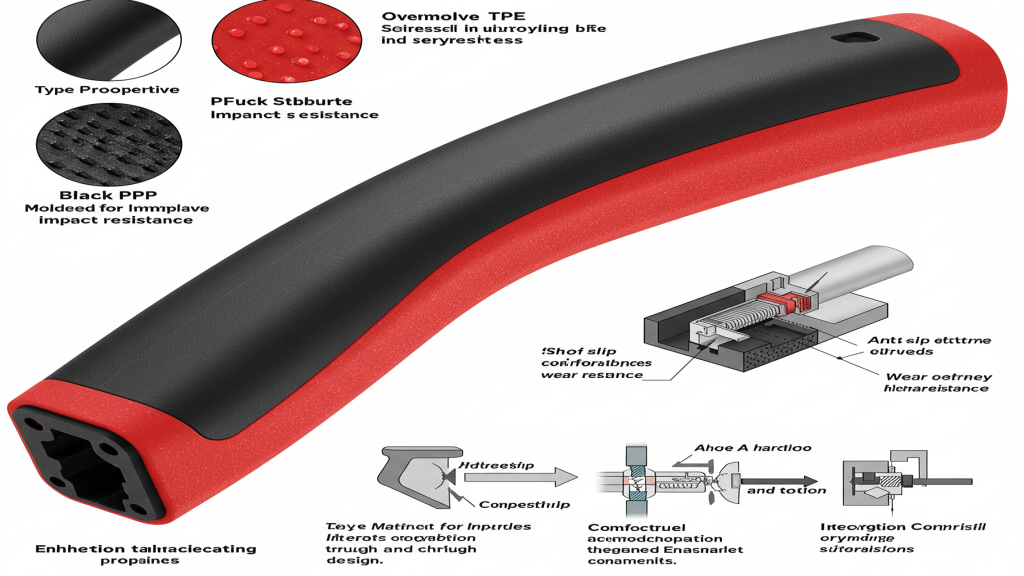
The overmolding process has strict requirements for the performance of the substrate, and not all types of black polypropylene (PP) can meet these conditions. Factors such as material compatibility, melting characteristics, and the bond strength of the final product determine whether a specific black PP can be successfully used in overmolding.
- Material Compatibility: Differences in the molecular structure and surface energy between different black PPs and overmolding materials lead to poor adhesion.
- Melting Characteristics: The melting temperature and flowability of black PP vary, making it difficult to synchronize with the overmolding material for high-quality molding.
- Pigments and Additives: Pigments and additives in black PP may migrate or react, weakening the bond with the secondary injection molding material.
- Surface Treatment Adaptability: Not all black PPs are suitable or can be effectively surface pre-treated to enhance adhesion.
What characteristics determine the overmoldability of black PP?
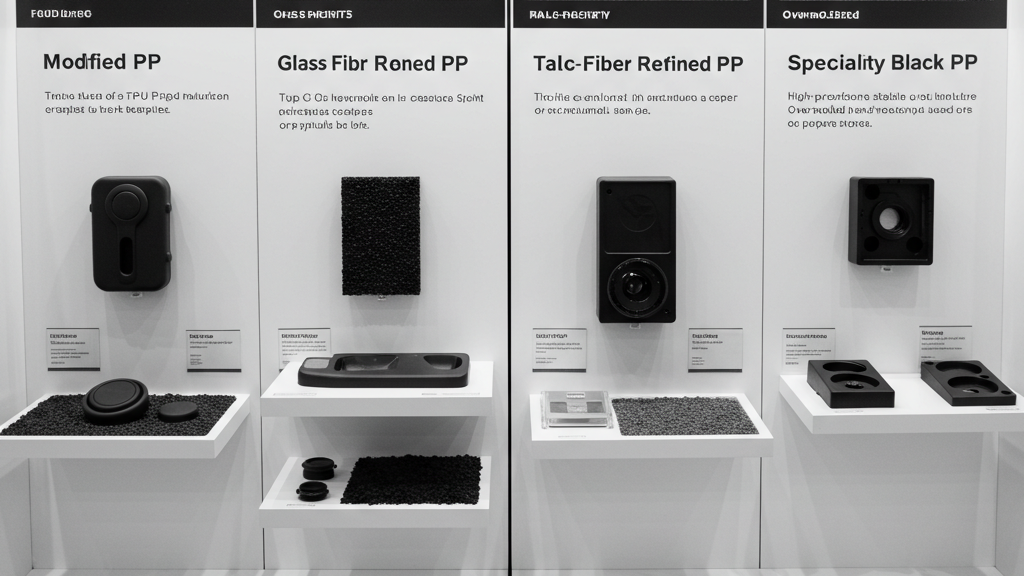
The successful application of black polypropylene in overmolding largely depends on its own key material characteristics. These characteristics directly affect the bonding effect with the second material and the overall performance of the final product.
- Melt Flow Index: A matching melt flow index ensures good fusion and interfacial bonding between the black PP and the secondary injection molding material.
- Surface Energy: Appropriate surface energy promotes wetting and effective adhesion between the black PP and the secondary injection molding material.
- Chemical Compatibility: A similar or interactive chemical structure is key to the strong bonding of black PP and secondary injection molding materials.
- Thermal Stability: Sufficient heat resistance ensures that the black PP does not warp or deform during the overmolding process, maintaining the quality of the bond.
Which types of black PP can be used for overmolding?
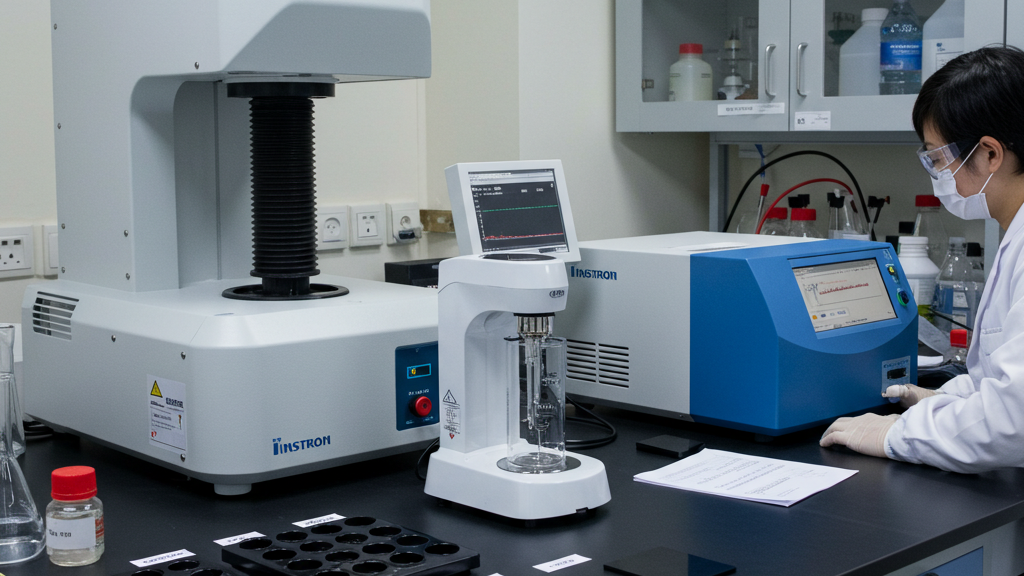
There are several modified black polypropylene (PP) types on the market that can be used in overmolding processes. Understanding the properties of these different types of black PP and their advantages and limitations in overmolding is crucial for selecting the right material.
- Modified PP: Improves adhesion to polar materials through chemical modification, but is more expensive and has limited effect on non-polar materials.
- Glass Fiber Reinforced PP: Enhances rigidity, strength, and heat resistance, but may reduce flowability and affect surface bonding uniformity.
- Talc-Filled PP: Improves stiffness and dimensional stability at a lower cost, but has limited improvement in chemical bonding.
- Specialty Black PP: Formulated specifically for overmolding, optimizes bonding performance, but may be more expensive and have a narrow selection range.
Application performance of black PP
Black PP Type |
Main Advantages |
Main Limitations |
Typical Application Scenarios |
Secondary Injection Bonding Performance Assessment |
Modified PP (PP-g-MAH) | Strong adhesion to polar materials, good chemical resistance, good temperature resistance | Higher cost, limited effect on non-polar materials, high requirements for modification control | Automotive interior parts (with TPU overmolding), electronic product housings (with PA overmolding), medical devices, etc. | Excellent |
Glass Fiber Reinforced PP | High rigidity, good strength, good heat resistance, good dimensional stability | Potentially poor flowability, exposed glass fibers may affect surface bonding, potentially poor adhesion to flexible materials | Automotive structural parts, appliance housings, power tool housings, etc. | Good to Fair |
Talc Filled PP | Lower cost, improved rigidity and dimensional stability, somewhat improved surface roughness | Potentially poor flowability, mainly relies on mechanical interlocking, high filling may reduce toughness | Low-end automotive interior parts, daily necessities, some appliance components, etc. | Fair |
Dedicated Secondary Injection Black PP | High specificity, excellent bonding performance with specific overmolding materials, stable performance | Potentially higher cost, narrow selection range, may need to be used with specific overmolding materials | Electronic products with high bonding requirements, medical devices, high-end consumer goods, etc. | Excellent |
Key Considerations for Overmolding
When selecting a suitable black PP for overmolding in practical applications, it is necessary to carefully evaluate the compatibility of the black PP with the overmolding material, ensuring that they are well-matched in terms of melting temperature, flowability, and chemical properties to achieve a stable and durable bond.
1.Adhesion Performance: It is essential to ensure good compatibility and strong adhesion between the black PP and the overmolding material to guarantee product quality.
2.Performance Requirements: The selected black PP must meet the specific functional and durability performance indicators of the final product.
3.Process and Cost: Consider the processing adaptability and cost-effectiveness of the black PP to optimize production and enhance commercial value.
4.Appearance Consistency: The black PP should provide stable and uniform color and be visually consistent with the overmolding material.
Conclusion
Choosing a black PP suitable for overmolding is not a simple material replacement, but a complex decision-making process that requires a comprehensive consideration of many factors. From material compatibility, melting characteristics, and the influence of pigments and additives, to the final product’s performance requirements, the adaptability of the production process, cost-effectiveness, and the consistency of appearance and color, every aspect is crucial.
For expert assistance in implementing for your production needs, visit our resource center or contact us. Let’s help you scale up your manufacturing with precision and efficiency!
Post time: Apr-28-2025