When customizing metal products, choosing the right processing method is critical to the quality, cost and delivery time of the product.There are various common methods for customizing metals. Here are several commonly used metal customization methods:
1.CNC Machining:
CNC (Computer Numerical Control) machining is a method of precise metal cutting and processing using computer-controlled machine tools. By utilizing pre-programmed instructions, CNC machining enables high-precision and efficient customization of metal parts, suitable for products with complex shapes and precise requirements.
Advantages:
High precision and accuracy
Wide range of compatible materials
Suitable for complex shapes and intricate designs
Efficient for both small and large production runs
Disadvantages:
Higher initial setup cost
Longer production time for complex designs
Limited to subtractive manufacturing (material removal)
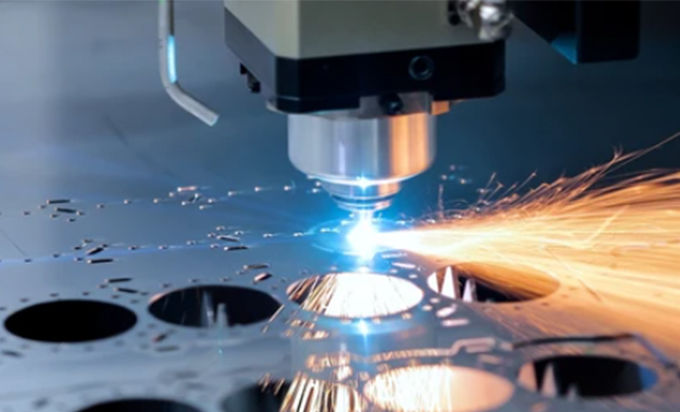
2.Milling and Turning:
Milling and turning involve cutting away metal material from workpieces using tools on machining equipment to achieve customized shapes and sizes. Milling is suitable for flat and complex surface machining, while turning is used for cylindrical workpieces.
Advantages:
Precise and accurate machining
Versatile for various shapes and sizes
Suitable for both prototypes and large-scale production
Wide range of compatible materials
Disadvantages:
Longer machining time for complex designs
Higher equipment and maintenance costs
Limited to rotational or symmetric parts in turning
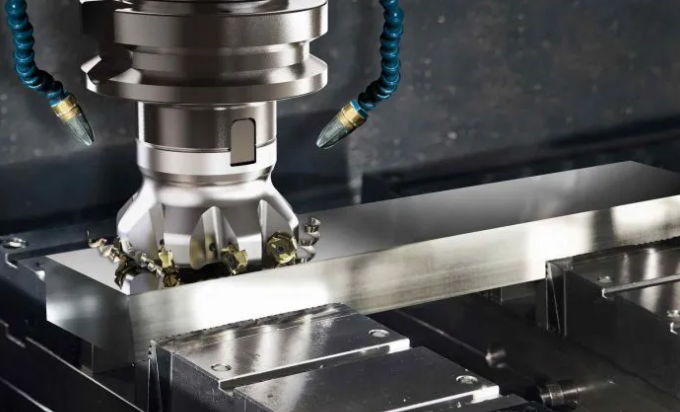
3.3D Printing:
3D printing technology enables the customization of metal parts by layer-by-layer deposition of materials. By melting or solidifying metal powders, complex-shaped metal parts can be directly printed, offering advantages of speed, flexibility, and customization.
Advantages:
Highly customizable and complex designs
Rapid prototyping and reduced lead time
Less material wastage compared to traditional methods
Suitable for low-volume production
Disadvantages:
Limited material options compared to traditional methods
Lower strength and durability compared to some traditional methods
Slower production speed for larger parts
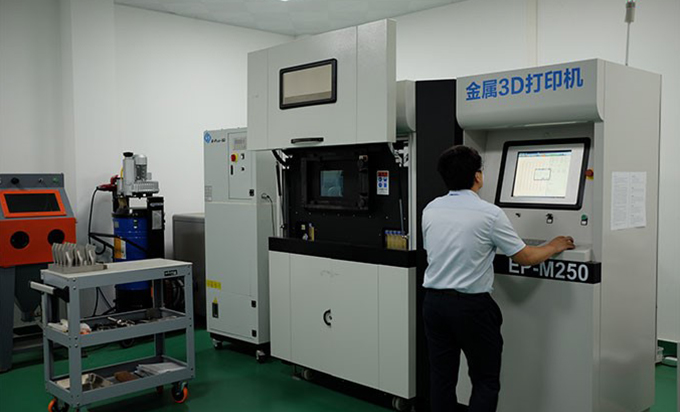
4.Laser Cutting:
Laser cutting is a method that employs a high-energy laser beam to melt, vaporize, or burn metal materials for cutting purposes. Laser cutting offers advantages such as high precision, speed, non-contact, and minimal deformation, making it suitable for customizing a wide range of metal parts and structures.
Advantages:
High precision and fine detail
Fast cutting speed
Non-contact process, minimizing material distortion
Suitable for various metals and thicknesses
Disadvantages:
Limited to 2D cutting profiles
Higher equipment and maintenance costs
May require additional post-processing for smooth edges
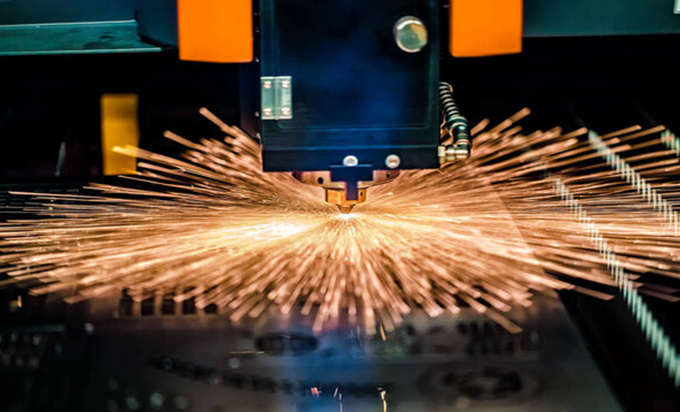
5.Stamping and Forming:
Stamping and forming involve applying pressure to metal materials to shape them into desired forms. Cold stamping or hot stamping processes can be used to achieve custom metal parts and components with complex shapes and high precision.
Advantages:
High production speed for large quantities
Cost-effective for repetitive designs
Suitable for complex shapes and tight tolerances
Enhanced material strength and durability
Disadvantages:
Higher initial tooling cost
Limited to specific shapes and sizes
Not ideal for prototypes or small production runs
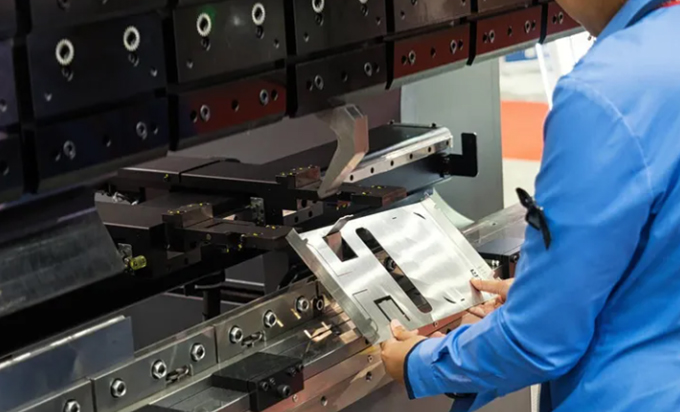
6.Die Casting:
Die Casting is a process in which molten metal is injected into a mold under high pressure to rapidly solidify and form the desired shape. The main steps include mold preparation, metal melting, injection, cooling, and demolding.
Advantages:
High Precision: Die Casting can produce parts with complex shapes, intricate details, and precise dimensions, ensuring consistency and high accuracy.
High Production Efficiency: Die Casting is suitable for mass production, with fast injection and rapid cooling, enabling high output rates.
Strength and Durability: Die-cast parts typically exhibit excellent mechanical properties, including high strength, rigidity, and corrosion resistance.
Disadvantages:
High Cost: Die Casting requires the production of dedicated metal molds, which can be expensive in terms of mold manufacturing and preparation costs.
Limited Material Selection: Die Casting is primarily applicable to low-melting-point metals such as aluminum alloys, zinc alloys, and magnesium alloys. It is less suitable for high-melting-point metals like steel or copper.
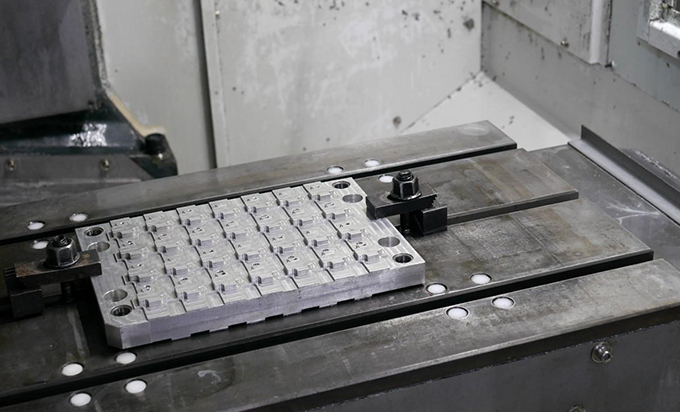
7.Extrusion:
Extrusion is a process in which heated metal is forced through a die using an extrusion machine to form continuous cross-sectional shapes. The main steps include preheating the metal billet, extrusion, cooling, and cutting.
Advantages:
Efficient Production: Extrusion is suitable for continuous production, enabling fast and efficient manufacturing of long lengths and large quantities of parts.
Versatile Shapes: Extrusion can be used to produce various cross-sectional shapes, such as solid, hollow, and complex profiles, offering high adaptability.
Material Savings: Through control of the extrusion die shape and dimensions, material waste can be minimized.
Disadvantages:
Limited Precision: Compared to Die Casting, Extrusion has lower precision and higher surface roughness.
Material Limitations: Extrusion is primarily suitable for malleable metals like aluminum and copper. It becomes more challenging for harder metals.
Mold Manufacturing: The production and maintenance of extrusion dies require specialized skills and incur higher costs.
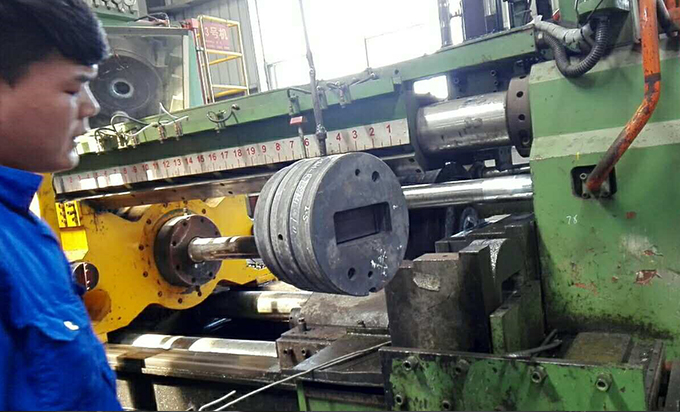
How to choose the right custom metal processing method
Product design and requirements: Understand the design requirements of the product, including shape, dimensions, material, and surface requirements. Different metal processing methods are suitable for different product designs and requirements.
Material selection: Choose the appropriate metal material based on the product's characteristics and requirements. Different metal materials are suitable for different processing methods. For example, aluminum alloys are suitable for extrusion and die casting, while stainless steel is suitable for CNC machining and casting.
Processing precision: Select the suitable processing method based on the product's precision requirements. Some methods, such as CNC machining and grinding, can provide higher precision and surface quality, which are suitable for products that require high accuracy.
Production volume and efficiency: Consider the production volume and efficiency requirements of the product. For large-scale production, high-efficiency processing methods such as stamping, extrusion, and die casting may be more suitable. For small-batch production or customized products, methods like CNC machining and 3D printing offer flexibility.
Cost considerations: Take into account the cost factors of the processing method, including equipment investment, process flow, and material costs. Different processing methods have different cost structures, so cost-effectiveness should be considered.
Our team of professional engineers is well-versed in a wide range of metal processing methods and can provide you with valuable insights and recommendations. We have in-depth knowledge of the latest advancements in the industry and can help you navigate through the complexities of selecting the most suitable method for your specific project.
Whether you need assistance with precision machining, forging, casting, or any other metal processing technique, our engineers can offer guidance tailored to your requirements. We will take into account factors such as material properties, desired tolerances, production volume, and cost considerations to help you make an informed decision.
Additionally, our engineers can provide support in optimizing the design of your metal components for manufacturability, ensuring that they can be efficiently produced using the selected processing method. We can offer suggestions for design modifications that can improve the overall quality, functionality, and cost-effectiveness of your products.
Please feel free to contact me and we are ready to help you achieve the best results in your metalworking.
Post time: Dec-18-2023