Due to the high transmittance of transparent plastic, there are strict requirements on the surface quality of plastic products, such as no spots, no patterns, porosity, whitish, edge lines, black spots, discoloration, uneven luster, etc. Therefore, in the whole injection molding process, there should be strict and special requirements for raw materials, equipment, molds and even product design.
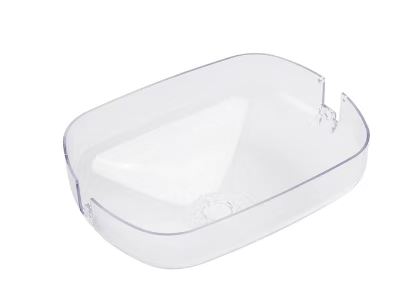
Since transparent plastics generally have a high melting point but poor flow ability, adjusting the machine temperature coefficient, injection pressure, and injection speed to ensure surface quality can fill the injection site while reducing the possibility of generating internal stress and causing deformation and cracking. Therefore, strict operations should be carried out in raw material preparation, equipment such as clear plastic molding kits and injection mold requirements, injection molding process and raw material handling of products. How to make a transparent plastic more clearly? Following are some aspects you should know:
1. Preparing and drying of raw materials
Since a little impurity in the plastic will affect the transparency of the product, the product should be properly sealed during storage, transportation and feeding to ensure the product is clean, especially the raw material is easy to deteriorate after heating. There is little moisture, so it should be dried in the sun. In addition, the hopper needs to be dried when feeding. Also, the incoming air should be filtered and dehumidified during the drying process to ensure that it does not contaminate the raw material.
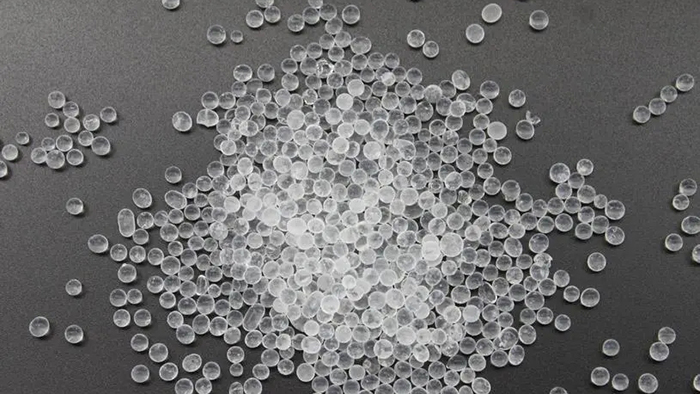
2.Cleaning of barrel, screw and other accessories
To prevent the contamination of raw materials and hidden residues or impurities in the recesses of accessories, especially resin with poor thermal stability, the plastic on the mold and the screw of the machine must be cleaned with cleaning agents to completely remove impurities, or in the absence of screw cleaning agents, use PE, PS and other resins to clean the screw. When suddenly shut down, in order to prevent the decomposition of raw materials at high temperatures for a long time, the temperature of the dryer and the barrel should be reduced, such as PC,PMMA barrel temperature should be below 160 degrees (hopper temperature should be reduced to below 100 degrees PC).
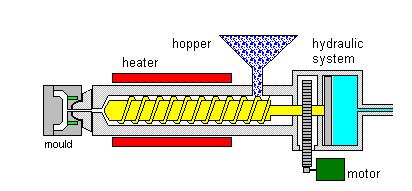
3.Injection mold design should pay attention to following points(including product design)
The following points should be noted when designing injection molds to prevent poor plastic molding, surface defects and deterioration caused by poor reflow or uneven cooling.
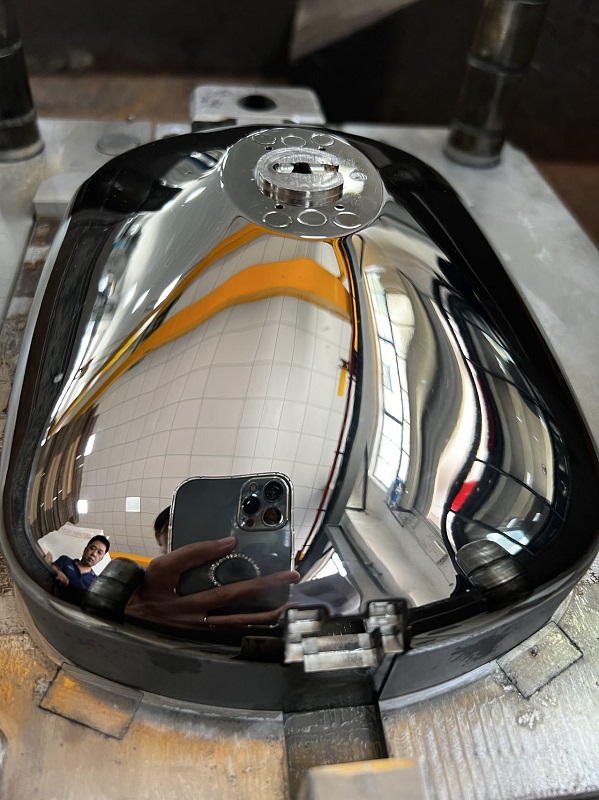
a) The wall thickness should be as constant as possible and the mold draft slope should be as large as possible.
b) The transition should be gentle and smooth to prevent sharp corners and sharp edges, especially for pc products, and there should be no gaps.
c) Gating: The runner should be as wide and short as possible, and the location of the gate should be according to the shrinkage process. Cold material well is needed if necessary.
d) Injection mold surface should be smooth with low roughness (max Ra0.8)
e)The number of venting holes and exhaust slots should be sufficient to discharge the air and gas from the melt.
f) The wall thickness should not be too thin except for PET material, generally not less than 1mm.
Talk to us about your new project ,free consultation and free DFM
Post time: Nov-01-2022