Designing injection-molded parts with maximum strength and durability requires attention to material selection, part geometry, and processing parameters. To achieve optimal strength, focus on using appropriate materials, optimizing wall thickness, and ensuring uniform filling during the molding process. These strategies will help you create parts that can withstand mechanical stress and environmental conditions, ensuring long-term reliability.
Let’s explore the key design considerations to achieve the strongest and most durable molded parts.
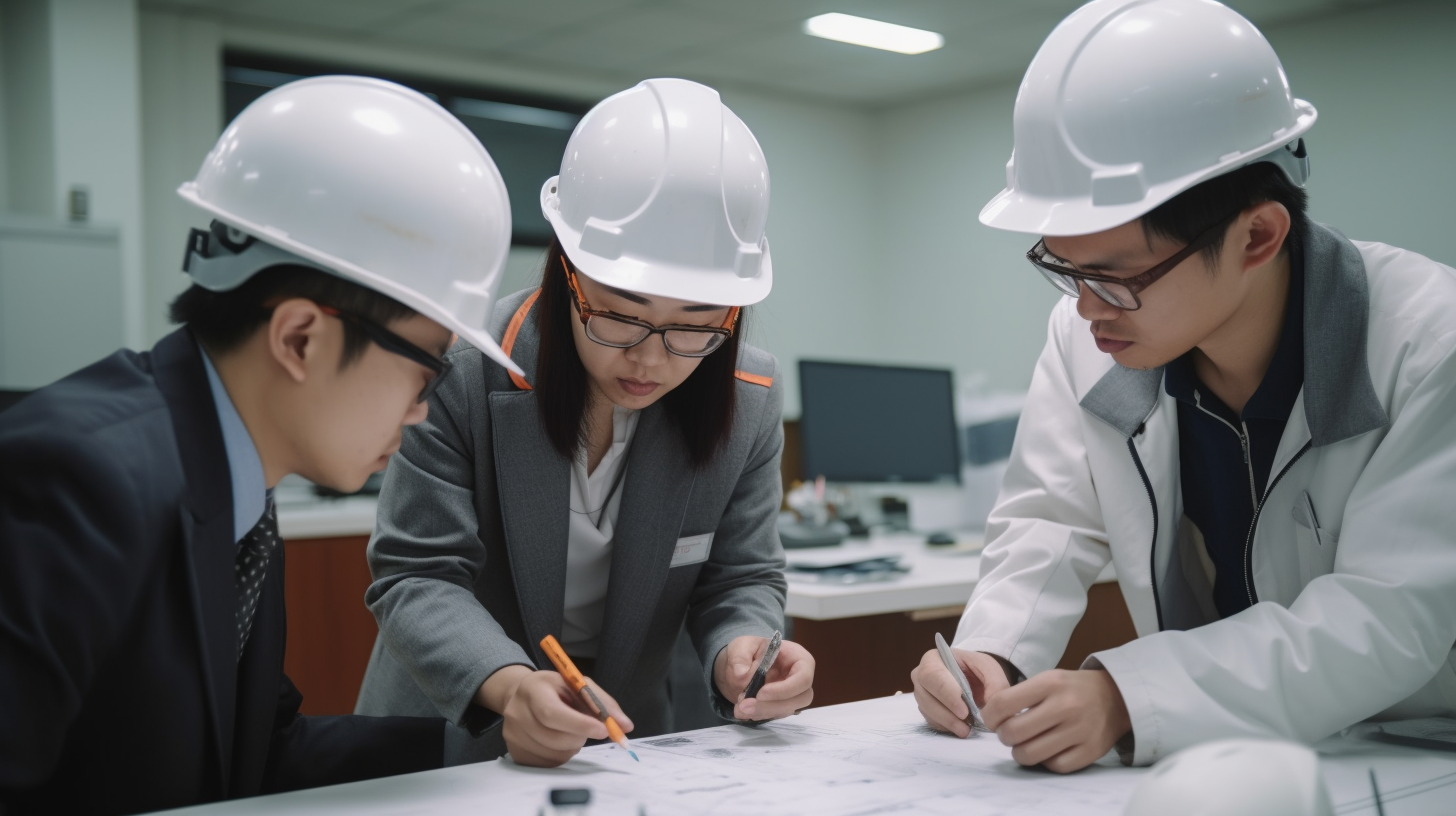
Why is Material Selection Crucial for Strength?
Material selection is the first step in designing strong, durable parts. High-strength materials like glass-filled nylon, polycarbonate, and high-performance thermoplastics such as PEEK offer excellent mechanical properties. Materials should be chosen based on the part’s expected load, environmental conditions, and required impact resistance.
Glass-filled nylon is a great choice for parts that need to handle heavy mechanical loads, while polycarbonate is ideal for applications that require both strength and transparency. High-performance materials like PEEK and PPS are suited for extreme conditions, offering unparalleled strength and heat resistance.

How Does Wall Thickness Impact Strength?
Uniform wall thickness is key to ensuring consistent strength across the part. Uneven wall thickness can lead to stress concentrations, causing warping or cracking under load. For maximum strength, the walls of your part should be as uniform as possible, especially in areas where the part will experience stress.
While thicker walls can provide added strength, they also increase cooling time and material usage. Therefore, optimizing wall thickness to balance strength and efficiency is crucial. For structural parts, aim for walls that are thick enough to provide durability but not so thick that they affect cycle times or part weight.
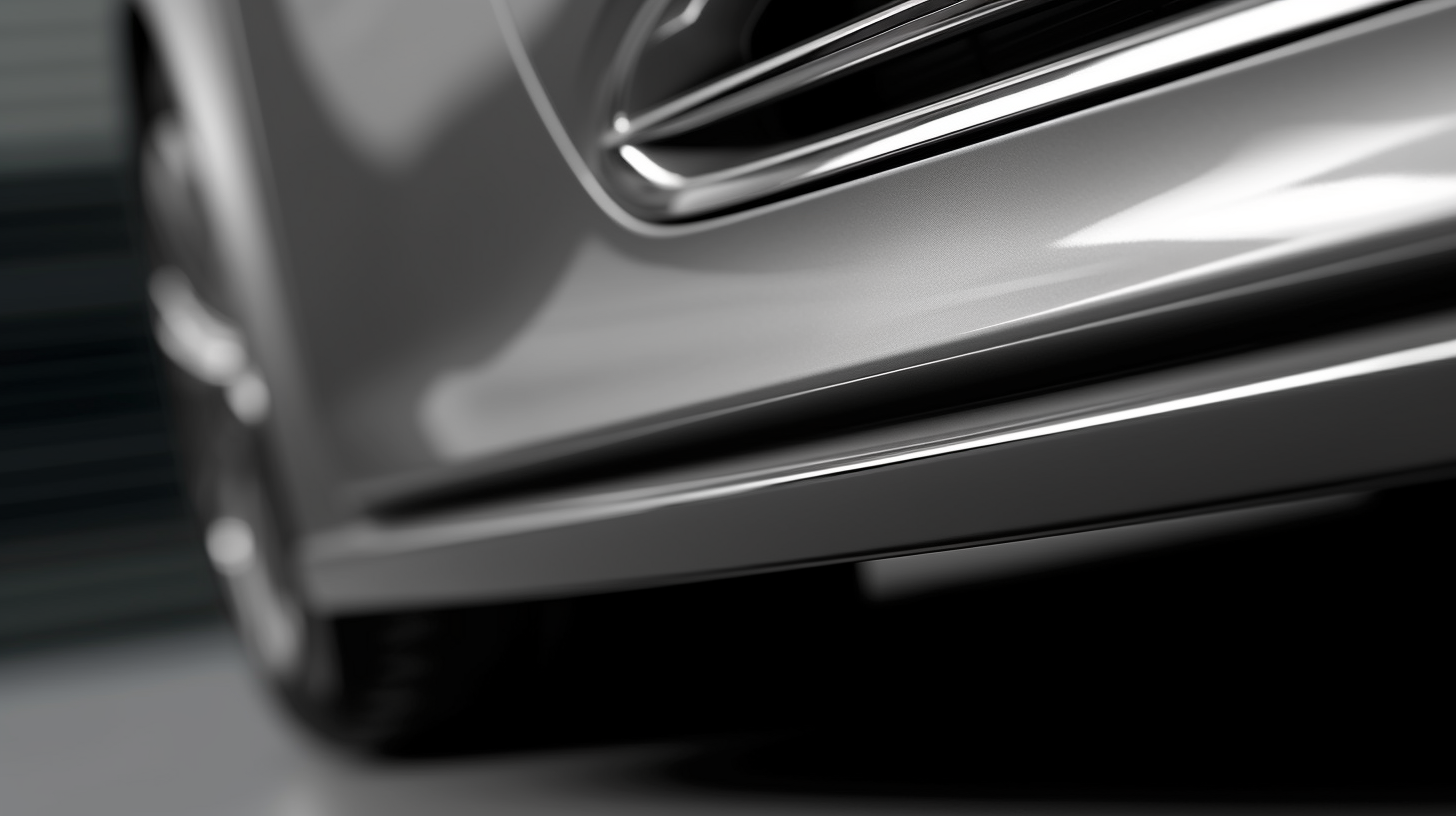
Why Are Ribs and Bosses Important for Strength?
Ribs and bosses provide additional structural support without significantly increasing the part’s weight or material consumption. Ribs should be added in areas where the part experiences bending or torsional forces, helping to reinforce the structure without compromising the molding process.
Bosses, on the other hand, help with fastening components to the part. They should be designed with enough thickness to support screws or other fastening mechanisms, but not so thick that they cause material flow issues during injection.
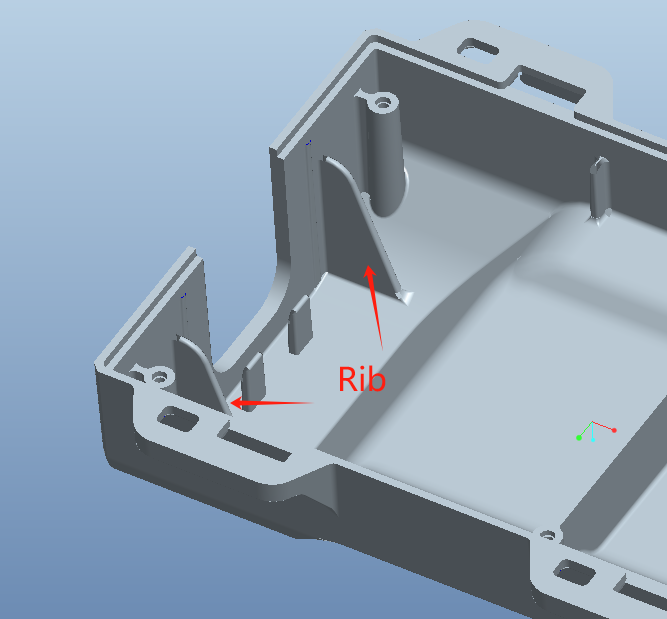
How Does the Molding Process Affect Strength?
The molding process also plays a significant role in the strength of the part. Optimizing injection speed, pressure, and temperature ensures that the material fills the mold cavity uniformly and solidifies in a way that maximizes part strength. A well-designed cooling system and appropriate packing pressure ensure that the part cools evenly, preventing warping or shrinkage.
Using simulation tools, like Moldflow analysis, can help predict how the material will behave during the molding process and allow you to make adjustments to improve strength.

Comparison of Design Features for Strength
Design Feature | Benefit for Strength | Best Practices |
Material Selection | Ensures optimal mechanical properties | Choose high-strength materials like glass-filled nylon or PEEK |
Wall Thickness | Prevents stress concentrations | Maintain uniform wall thickness |
Ribs and Bosses | Adds structural support without excess weight | Design ribs for bending forces and bosses for fastening |
Molding Process | Ensures uniform filling and cooling | Optimize injection pressure and cooling time |
Key Tips for Maximizing Strength in Injection-Molded Parts
Optimize Material Choice: Select materials that meet your specific strength, impact, and environmental resistance needs.
Maintain Uniform Wall Thickness: Avoid variations in wall thickness to prevent warping and uneven cooling.
Incorporate Ribs and Bosses: Add structural support without compromising the part’s weight or moldability.
Monitor the Molding Process: Adjust injection speed, pressure, and cooling time to ensure uniform material flow and prevent defects.
Conclusion
Designing injection-molded parts for maximum strength and durability requires a combination of proper material selection, optimized part geometry, and fine-tuned molding processes. By focusing on these factors, you can create parts that not only withstand mechanical stress but also perform reliably in challenging environments.
For expert advice on designing strong, durable injection-molded parts, visit our resource center or contact us. Let’s help you bring your next project to life with precision and durability!
Post time: Jan-20-2025