Plastic plating is an plating process that has been widely used in electronics industry, defence research, household appliances and daily necessities. The application of plastic plating process has saved a large amount of metal materials, its processing process is simpler and its own weight is lighter compared to metal materials, so that the equipment produced by using plastic plating process is also reduced in weight, also making the appearance of plastic parts with higher mechanical strength, more beautiful and durable.
The quality of plastic plating is very important. There are many factors affecting the quality of plastic plating, including the plating process, the operation and the plastic process, which can have a significant impact on the quality of plastic plating.
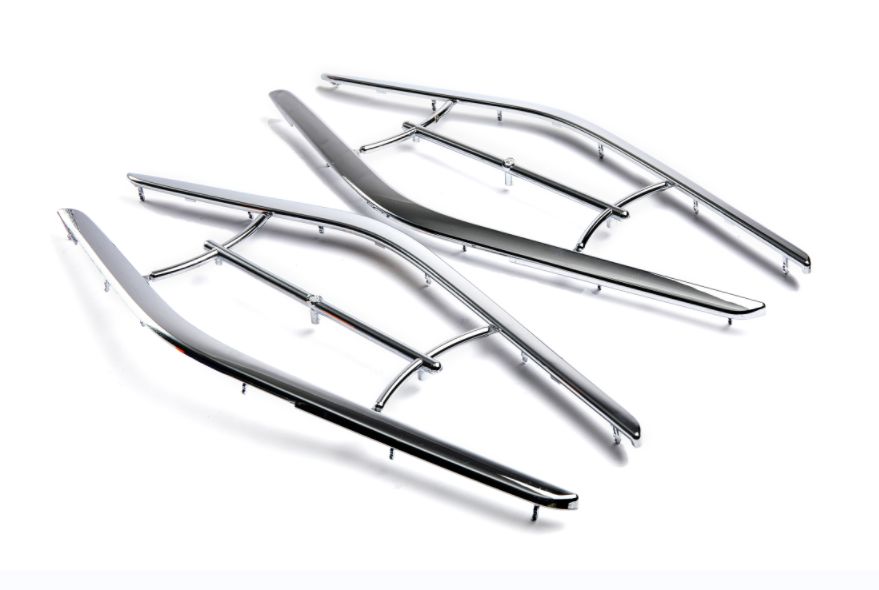
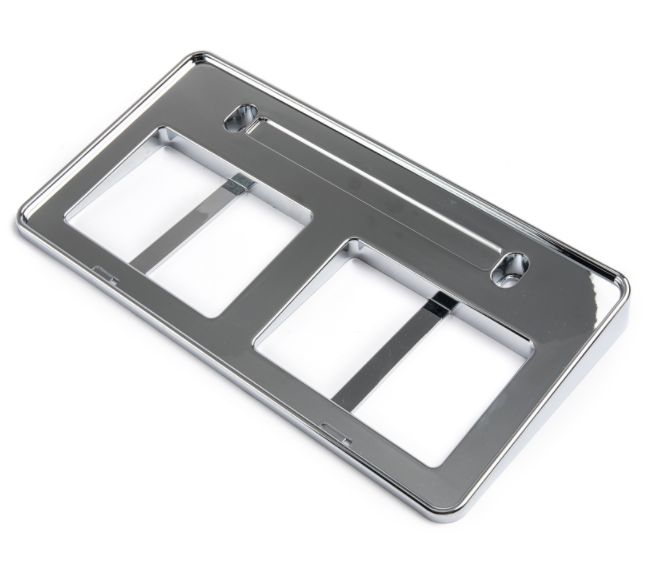
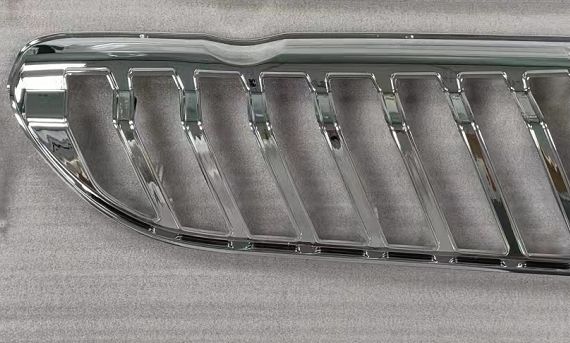
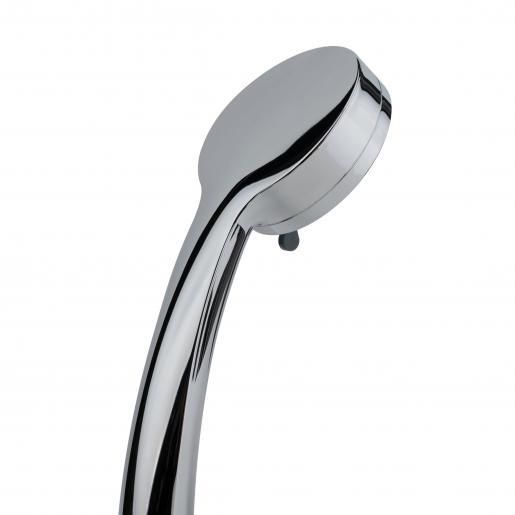
1. Raw material selection
There are many different types of plastics on the market, but not all can be plated, as each plastic has its own properties, and when plating it needs to consider the bond between the plastic and the metal layer and the similarity between the physical properties of the plastic and the metal coating. The plastics currently available for plating are ABS and PP.
2.Shape of parts
A). The thickness of the plastic part should be uniform to avoid unevenness causing shrinkage of the plastic part, when the plating is completed, its metallic lustre causes shrinkage more obviously at the same time.
And the wall of the plastic part should not be too thin, otherwise it will be easily deformed during plating and the bonding of the plating will be poor, while the rigidity will be reduced and the plating will easily fall off during use.
B). Avoid blind holes, otherwise the residual treatment solution in the blind solenoid will not be easily cleaned and will cause pollution in the next process, thus affecting the plating quality.
C). If the plating is sharp-edged, the plating will be more difficult, as the sharp edges will not only cause power generation, but also cause the plating to bulge at the corners, so you should try to choose a rounded corner transition with a radius of at least 0.3mm.
When plating flat plastic parts, try to change the plane to a slightly rounded shape or make a matt surface for plating, because the flat shape will have an uneven plating with a thin centre and a thick edge when plating. Also, to increase the uniformity of the plating gloss, try to design plastic parts with a large plating surface area to have a slightly parabolic shape.
D). Minimise recesses and protrusions on plastic parts, as deep recesses tend to reveal plastic when plating and protrusions tend to scorch. The depth of the groove should not exceed 1/3 of the width of the groove, and the bottom should be rounded. When there is a grille, the width of the hole should be equal to the width of the beam and less than 1/2 of the thickness.
E). Sufficient mounting positions should be designed on the plated part and the contact surface with the hanging tool should be 2 to 3 times larger than that of the metal part.
F). Plastic parts need to be plated in the mould and demoulded after plating, so the design should ensure that the plastic parts are easy to demould so as not to manipulate the surface of the plated parts or affect the bonding of the plating by forcing it during demoulding.
G). When knurling is required, the knurling direction should be the same as the demoulding direction and in a straight line. The distance between the knurled stripes and the stripes should be as large as possible.
H). For plastic parts that require inlays, avoid using metal inlays as much as possible because of the corrosive nature of the treatment before plating.
I). If the surface of the plastic part is too smooth, it is not conducive to the formation of the plating layer, so the surface of the secondary plastic part should have a certain surface roughness.
3.Mould design and manufacturing
A). The mould material should not be made of beryllium bronze alloy, but high quality vacuum cast steel. The surface of the cavity should be polished to mirror brightness along the direction of the mould, with an unevenness of less than 0.21μm, and the surface should preferably be plated with hard chrome.
B). The surface of the plastic part reflects the surface of the mould cavity, so the mould cavity of the electroplated plastic part should be very clean, and the surface roughness of the mould cavity should be 12 grades higher than the surface roughness of the surface of the part.
C). The parting surface, fusion line and core inlay line should not be designed on the plated surface.
D). The gate should be designed at the thickest part of the part. To prevent the melt from cooling too quickly when filling the cavity, the gate should be as large as possible (about 10% larger than the normal injection mould), preferably with a round cross-section of the gate and sprue, and the length of the sprue should be shorter.
E). Exhaust holes should be provided to avoid defects such as air filaments and bubbles on the surface of the part.
F). The ejector mechanism should be selected in such a way as to ensure smooth release of the part from the mould.
4.Condition of injection molding process for plastic parts
Due to the characteristics of the injection moulding process, internal stresses are inevitable, but proper control of the process conditions will reduce the internal stresses to a minimum and ensure the normal use of the parts.
The following factors influence the internal stress of the process conditions.
A). Raw material drying
In the injection moulding process, if the raw material used for plating parts is not dry enough, the surface of the parts will easily produce air filaments and bubbles, which will have an impact on the appearance of the coating and the bonding force.
B). Mould temperature
The temperature of the mould has a direct influence on the bonding force of the plating layer. When the temperature of the mould is high, the resin will flow well and the residual stress of the part will be small, which is conducive to improving the bonding force of the plating layer. If the temperature of the mould is too low, it is easy to form two interlayers, so that the metal is not deposited when plating.
C). Processing temperature
If the processing temperature is too high, it will cause uneven shrinkage, thus increasing the volume temperature stress, and the sealing pressure will also rise, requiring extended cooling time for smooth demoulding. Therefore, the processing temperature should be neither too low nor too high. The nozzle temperature should be lower than the maximum temperature of the barrel to prevent the plastic from flowing. To prevent the cold material into the mould cavity, so as to avoid the production of lumps, stones and other defects and cause the combination of poor plating.
D). Injection speed, time and pressure
If these three are not well mastered, it will cause an increase in residual stress, so the injection speed should be slow, the injection time should be as short as possible, and the injection pressure should not be too high, which will effectively reduce residual stress.
E). Cooling time
The cooling time should be controlled so that the residual stress in the mould cavity is reduced to a very low level or close to zero before the mould is opened. If the cooling time is too short, forced demoulding will result in large internal stresses in the part. However, the cooling time should not be too long, otherwise not only will the production efficiency be low, but also the cooling shrinkage will cause tensile stresses between the inner and outer layers of the part. Both of these extremes will reduce the bonding of the plating on the plastic part.
F). The influence of release agents
It is best not to use release agents for plated plastic parts. Oil-based release agents are not permitted, as they may cause chemical changes to the surface layer of the plastic part and alter its chemical properties, resulting in poor bonding of the plating.
In cases where a release agent must be used, only talcum powder or soapy water should be used to release the mould.
Due to the different influencing factors in the plating process, the plastic parts are subjected to different degrees of internal stress, which leads to a reduction in the bonding of the plating and requires effective post-treatment to increase the bonding of the plating.
At present, the use of heat treatment and treatment with surface finishing agents has a very good effect on the elimination of internal stresses in plastic parts.
In addition, the plated parts need to be packed and inspected with extreme care, and special packaging should be carried out to avoid damaging the appearance of the plated parts.
Xiamen Ruicheng Industrial Design Co.,Ltd has rich experience on Plastic plating , feel free to reach us if you have any need!
Post time: Feb-22-2023