Injection moulding surface finish as per SPI and VDI classification systems – Gloss, semi-gloss, matte and textured surface finish.
Contents covered in this article
What are Injection moulding surface finishes?
Injection moulding surface finish is critical to a successful part design and used for aesthetic and functional reasons in plastic injection molding parts for engineering products. The surface finish improves the look and the feel of a product as the perceived value and quality of the product increase with a suitable surface finish.
Plastic Case (Source :XR U.S.A Client )
Why use surface finishes in injection moulding?
To increase part aesthetics
Part designers may use textures for a variety of aesthetic purposes. A smooth or matte surface texture improves its appearance and gives it a polished aspect. It also covers faults generated by injection mouldings, such as tool machining marks, sink marks, weld lines, flow lines, and shadow markings. Parts with excellent surface quality appeal more to customers from a business standpoint.
To improve part functionality
Aside from the aesthetic considerations that go into selecting an injection moulding surface finish, there are also important practical considerations.
The design may necessitate a firm grip for optimal functioning. Textured plastic finishes improve grip quality. Hence injection moulding surface treatments are frequently used on slip-resistant products. A textured mould can also aid in the escape of trapped gases.
A smooth SPI surface finish may cause the paint to peel off. However, a rough surface can ensure that the paint adheres better to the moulded item. A textured SPI surface treatment also increases the part’s strength and safety.
Texture has several advantages, including:
- Plastic flow creases—These creases may be removed by adding textured thickness while increasing strength and non-slip properties.
- Improved grip—Adding texture to the component makes handling easier, increasing usefulness and safety in specific applications.
- Paint adhesion—Paint adheres firmly to a textured object during subsequent moulding.
- Making undercuts—If you have a portion that will not consistently come over to the moving half of a mould, texturing on any surface may provide the necessary pull.
Injection mould tool surface finish specifications
The most common way to specify injection moulding surfaces is by using PIA (or SPI), VDI and Mold-tech standards. Injection mould toolmakers, manufacturers and design engineers worldwide recognise these three standards and PIA standards are marginally more common and widely known as “SPI grades“.
Gloss finish – Grade A – Diamond finish
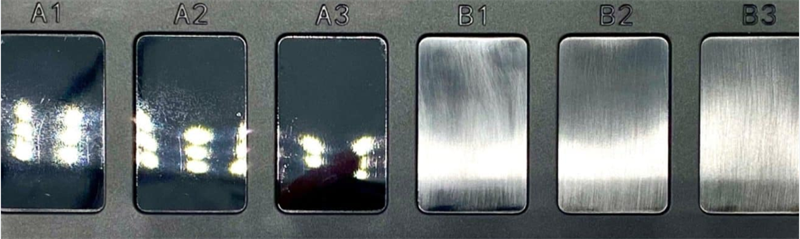
(SPI-A-B Injection-moulding surface finish)
These grade “A” finishes are smooth, glossy, and the most expensive. These grades would need hardened tool steel moulds, which are buffed using various grades of diamond buff. Because of the fine-grain buffing paste and random directional rotary polishing method, it will not have a clear texture and scatter light rays, giving a very glossy finish. These are also called “Diamond finish” or “buff finish” or “A finish”
Finish | SPI Standard | Finish Method | Surface Roughness(Ra Value) |
Very High Glossy Finish | A1 | 6000 Grit diamond buff | 0.012 to 0.025 |
High Glossy Finish | A2 | 3000 Grit diamond buff | 0.025 to 0.05 |
Normal Glossy Finish | A3 | 1200 Grit diamond buff | 0.05 to o.1 |
SPI gloss grades are suitable for products with a smooth surface finish for cosmetic and functional reasons. For example, A2 is the most common diamond finish used in the industry, resulting in good visually pleasing parts with a good release. In addition, grade “A” surface finishes are used on optical parts such as lenses, mirrors, and visors.
Semi-gloss finish – Grade B
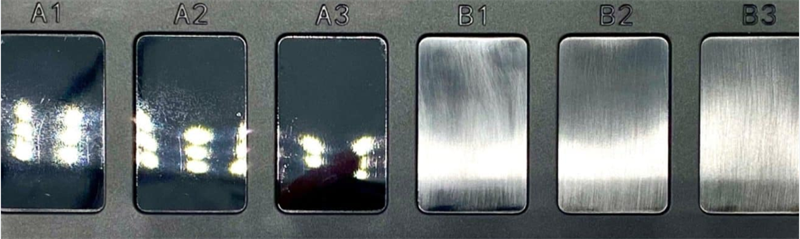
( figure 2.SPI-A-B Injection-moulding surface finish)
These semi-gloss finishes are great for removing machining, moulding, and tooling marks with a reasonable tooling cost. These surface finishes are produced using different grades of sandpapers applied with linear motion, giving a linear pattern as shown in figure 2.
Finish | SPI Standard | Finish Method | Surface Roughness(Ra Value) |
Fine Semi Glossy Finish | B1 | 600 Grit Paper | 0.05 to 0.1 |
Medium Semi Glossy Finish | B2 | 400 Grit Paper | 0.1 to 0.15 |
Normal emi Glossy Finish | B3 | 320 Grit Paper | 0.28 to o.32 |
SPI(B 1-3) semi-gloss surface finishes would give a good visual appearance and remove mould tool marks. These are often used in parts that aren’t a decorative or visual important part of the product.
Matte finish – Grade C
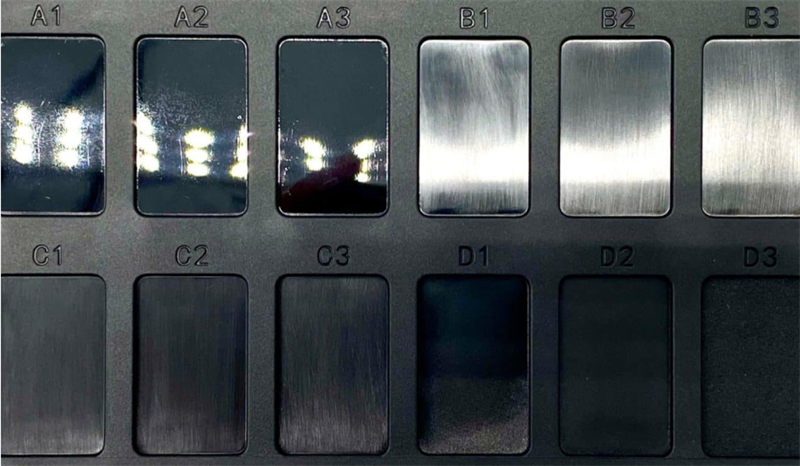
These are the most economical and popular surface finishes, polished using fine stone powder. Sometimes called stone finish, it provides good release and helps hide machining marks. Grade C is also the first step of grades A and B surface finishes.
Finish | SPI Standard | Finish Method | Surface Roughness(Ra Value) |
Medium Matte Finish | C1 | 600 Grit Stone | 0.35 to 0.4 |
Medium Matte Finish | C2 | 400 Grit Paper | 0.45 to 0.55 |
Normal Matte Finish | C3 | 320 Grit Paper | 0.63 to 0.70 |
Textured finish – Grade D
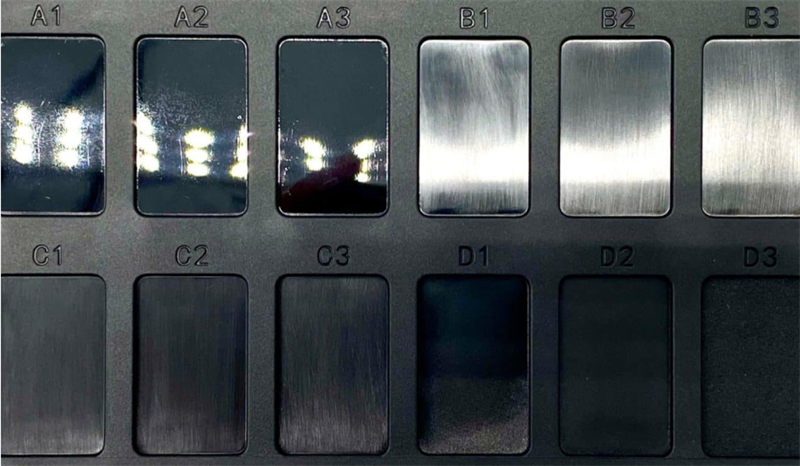
It gives the part a reasonable aesthetic visual appearance and is widely used in industrial parts and consumer goods. These are suitable for parts with no specific visual requirements.
Finish | SPI Standard | Finish Method | Surface Roughness(Ra Value) |
Satin Texture Finish | D1 | 600 stone prior to dry blast glass bead#11 | 0.8 to 1.0 |
Dry Texture Finish | D2 | 400 stone prior to dry blast glass #240 oxide | 1.0 to 2.8 |
Rough Texture Finish | D3 | 320 stone prior to dry blast #24 oxide | 3.2 to 18.0 |
No one ever said that designing and manufacturing molded parts was easy. Our goal is to get you through it quickly and with quality parts.
VDI Injection moulding surface finish
VDI 3400 Surface Finish (commonly known as VDI surface finish) refers to the mould texture standard set by Verein Deutscher Ingenieure (VDI), the Society of German Engineers. The VDI 3400 surface finish is mainly processed by Electrical Discharge Machining (EDM) when mold machining. It could also be done by the traditional texturing method (like in SPI). Although the standards are set by the society of German Engineers it is commonly used among tool makers all over, including North America, Europe, and Asia.
VDI values are based on the surface roughness. From the image, we see different textures of the surface finish with varying values of surface roughness.
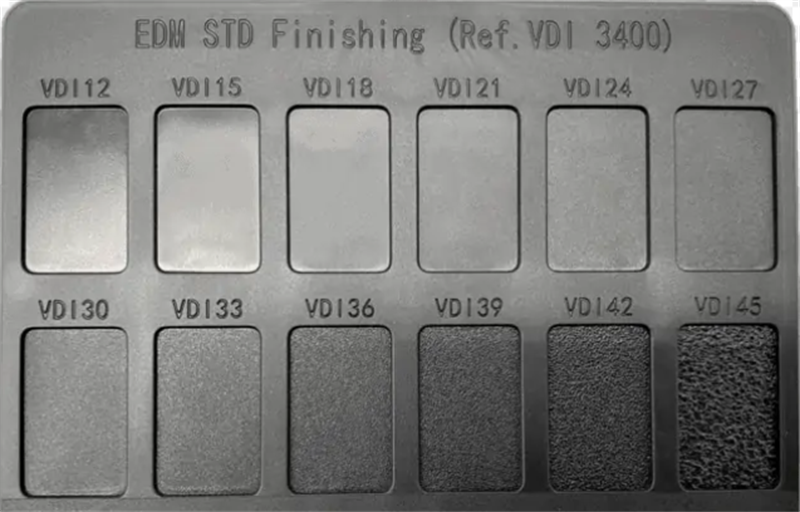
VDI Value | Description | Applications | Surface roughness (Ra µm) |
12 | 600 Stone | Low polish parts | 0.40 |
15 | 400 Stone | Low polish parts | 0.56 |
18 | Dry Blast Glass Bead | Satin finish | 0.80 |
21 | Dry Blast # 240 Oxide | Dull finish | 1.12 |
24 | Dry Blast # 240 Oxide | Dull finish | 1.60 |
27 | Dry Blast # 240 Oxide | Dull finish | 2.24 |
30 | Dry Blast # 24 Oxide | Dull finish | 3.15 |
33 | Dry Blast # 24 Oxide | Dull finish | 4.50 |
36 | Dry Blast # 24 Oxide | Dull finish | 6.30 |
39 | Dry Blast # 24 Oxide | Dull finish | 9.00 |
42 | Dry Blast # 24 Oxide | Dull finish | 12.50 |
45 | Dry Blast # 24 Oxide | Dull finish | 18.00 |
Conclusion
Out of the two categories of injection moulding surface finishes, SPI grade A and B are considered the smoothest with very low surface roughness and are more expensive. Whereas, from a surface roughness point of view, VDI 12, the highest quality VDI, equals SPI C grade.
No one ever said that designing and manufacturing molded parts was easy. Our goal is to get you through it quickly and with quality parts.
How to choose a suitable injection moulding surface finish?
Choose injection moulding surface finishes by considering part function, the material used, and visual requirements. Most of the typical plastic injection moulded material can have a variety of surface finishes.
The surface finish selection must be established in the early embodiment design stage of the product design because the surface dictates material selection and the draft angle, influencing the tooling cost. For example, a course or textured finish needs a more significant draft angle so that the part can be ejected from the mould.
So what are the prime factors to consider when choosing the surface finish for injection moulding plastics?
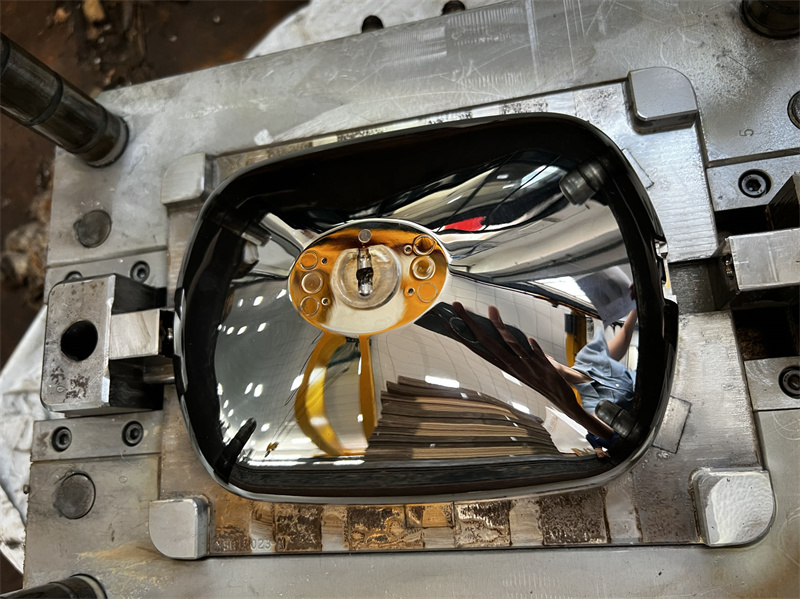
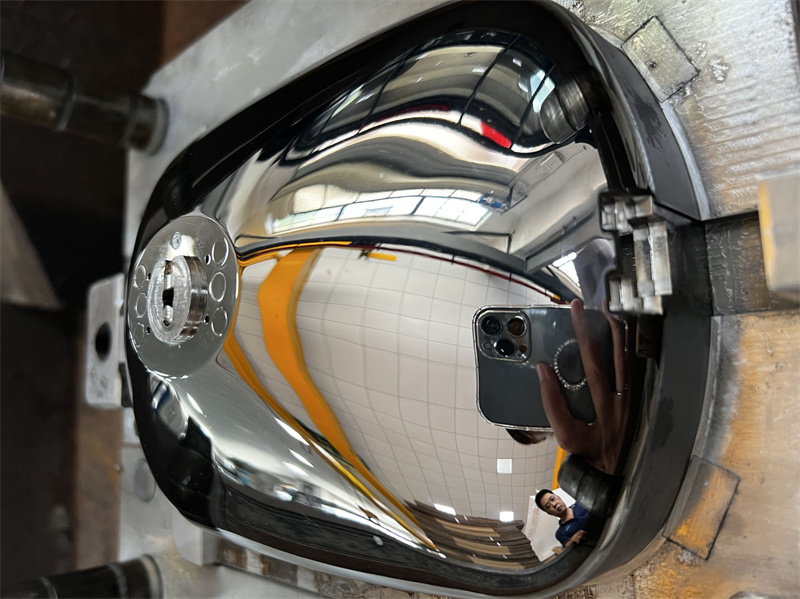
Gloss finish Grade A (Source: XR U.S.A Client)
Tooling cost
Surface finish and the material significantly influence the tool design and cost, so consider and evaluate the functionality in terms of surface early on the embodiment design. If the surface finish is critical to its functionality, consider the surface finish at the conceptual stages of the product design.
Many parts of the injection moulding process have been automated, but polishing is an exception. It is only the simplest of shapes that can be automatically polished. Polishers now have better equipment and materials to work with, but the process remains labour-intensive.
Draft angle
Most Parts Require a Draft Angle of 1½ to 2 Degrees
This is a rule of thumb that applies to molded parts with depths of up to 2 inches. With this size, a draft of about 1½ degrees is enough for easy release of parts from the mold. This helps to prevent damages to the parts when the thermoplastic material shrinks.
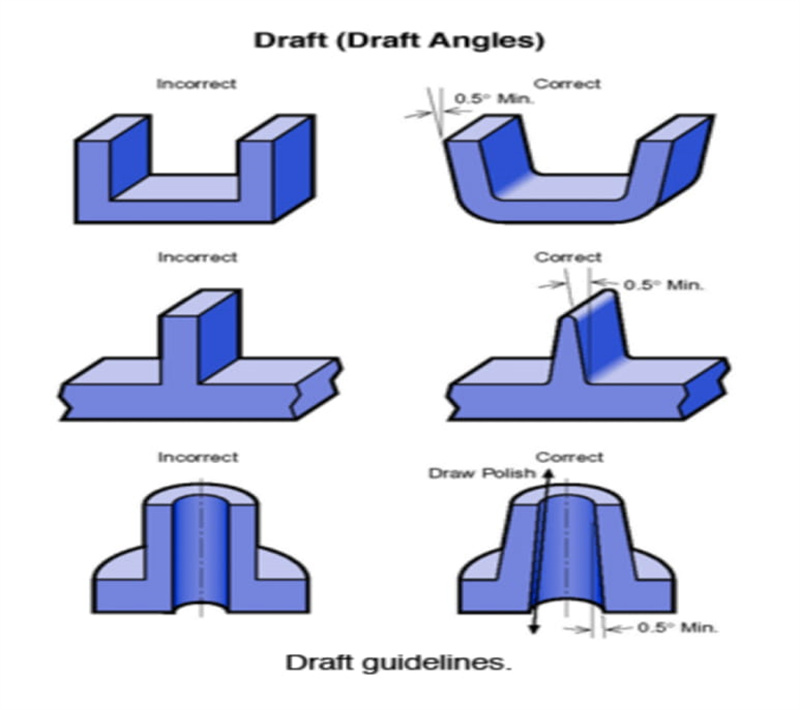
Mould tool material
The mould tool greatly influences the surface smoothness of the injection moulding. A mould may be made from various metals, although steel and aluminium are the most popular. The effects of these two metals on moulded plastic components are vastly different.
In general, hardened tool steel can produce smooth plastic finishes compared to aluminium alloy tools. Hence consider steel moulds if the pieces have an aesthetic function that requires a low level of surface roughness.
Moulding material
A wide range of injection moulding plastics is available to cover all sorts of parts and functions. However, not all plastics can achieve the same injection moulding surface finish. Some polymers are better suited to smooth finishes, while others are better suited to roughening up for a more textured surface.
Chemical and physical qualities differ between injection moulding materials. Melting temperature, for example, is a crucial factor in a material’s capacity to give a certain surface quality. Additives also have an impact on the outcome of a completed product. As a result, it is critical to evaluate the various materials before deciding on a surface texture.
Furthermore, material additives like filler and pigments might impact the surface finish of a moulded object. The tables in the next section illustrate the applicability of several injection moulding materials for various SPI finish designations.
Material suitability for Grade SPI-A surface finish
Material |
A-1 |
A-2 |
A-3 |
ABS |
Average |
Average |
Good |
Polypropylene (PP) |
Not recommended |
Average |
Average |
Polystyrene (PS) |
Average |
Average |
Good |
HDPE |
Not recommended |
Average |
Average |
Nylon |
Average |
Average |
Good |
Polycarbonate (PC) |
Average |
Good |
Excellent |
Polyurethane (TPU) |
Not recommended |
Not recommended |
Not recommended |
Acrylic |
Excellent |
Excellent |
Excellent |
Material suitability for Grade SPI-B surface finish
Material |
B-1 |
B-2 |
B-3 |
ABS |
Good |
Good |
Excellent |
Polypropylene (PP) |
Good |
Good |
Excellent |
Polystyrene (PS) |
Excellent |
Excellent |
Excellent |
HDPE |
Good |
Good |
Excellent |
Nylon |
Good |
Excellent |
Excellent |
Polycarbonate (PC) |
Good |
Good |
Average |
Polyurethane (TPU) |
Not recommended |
Average |
Average |
Acrylic |
Good |
Good |
Good |
Material suitability for Grade SPI-C surface finish
Material |
C-1 |
C-2 |
C-3 |
ABS |
Excellent |
Excellent |
Excellent |
Polypropylene (PP) |
Excellent |
Excellent |
Excellent |
Polystyrene (PS) |
Excellent |
Excellent |
Excellent |
HDPE |
Excellent |
Excellent |
Excellent |
Nylon |
Excellent |
Excellent |
Excellent |
Polycarbonate (PC) |
Average |
Not recommended |
Not recommended |
Polyurethane (TPU) |
Good |
Good |
Good |
Acrylic |
Good |
Good |
Good |
Material suitability for Grade SPI-D surface finish
Material |
D-1 |
D-2 |
D-3 |
ABS |
Excellent |
Excellent |
Good |
Polypropylene (PP) |
Excellent |
Excellent |
Excellent |
Polystyrene (PS) |
Excellent |
Excellent |
Good |
HDPE |
Excellent |
Excellent |
Excellent |
Nylon |
Excellent |
Excellent |
Good |
Polycarbonate (PC) |
Excellent |
Not recommended |
Not recommended |
Polyurethane (TPU) |
Excellent |
Excellent |
Good |
Acrylic |
Average |
Average |
Average |
Moulding parameters
Injection speed and temperature affect surface finish for a few reasons. When you combine fast injection speeds with higher melt or mold temperatures, the outcome will be enhanced gloss or smoothness of the part’s surface. In actuality, a fast injection speed improves overall gloss and smoothness. Additionally, quick filling of a mold cavity can produce less visible weld lines and a strong aesthetic quality for your part.
Deciding a part’s surface finish is an integral consideration in the overall product development and should be thought out during the design process to achieve the desired results. Have you considered the end use of your injection molded part?
Let Xiamen Ruicheng help you decide on a surface finish that improves the aesthetics and functionality of your part.
Post time: May-22-2023