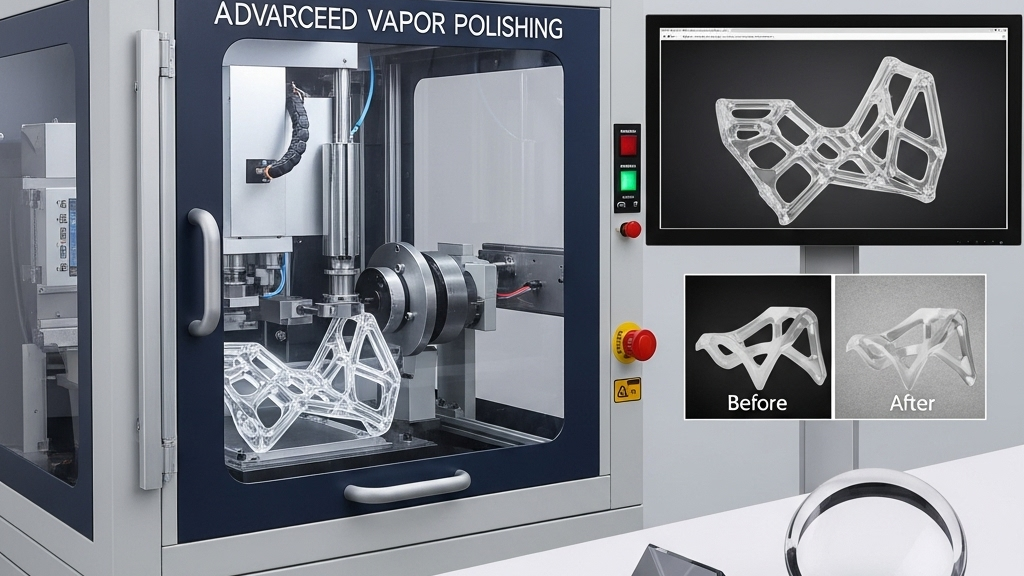
Vapor polishing uses heated chemical gases to microscopically reshape the surface of acrylic parts, achieving a mirror-like finish. This contactless process naturally protects fine edges and is especially suitable for optical components requiring high transparency and intricate shapes.In post-processing of precision injection-molded parts, vapor polishing is a highly competitive option.
With growing demand for high-end visual and functional clear components, traditional polishing and flame treatments struggle with certain complex geometries. Vapor polishing fills this technical gap, enabling high-quality finishes on hard-to-reach and irregular areas.Even complex curves and narrow structures can be evenly polished using vapor techniques.
Is polishing suitable for complex acrylic geometries?
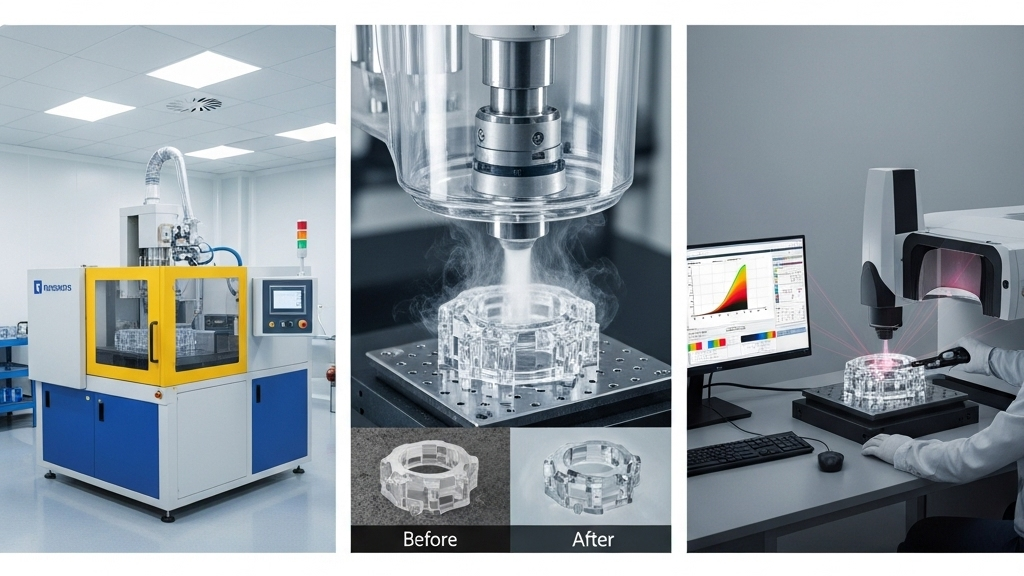
Common geometries in acrylic—such as sharp corners, recesses, and enclosed cavities—often challenge traditional polishing methods in preserving surface integrity. Vapor polishing, however, uses molecular diffusion to overcome physical contact limitations and adapts more flexibly.This makes it particularly effective for highly curved and intricate acrylic designs.
- Curved Surface Friendly: Handles bent, holed, or irregular parts.
- Edge Refinement: Corners remain intact without mechanical wear.
- Contact-Free Advantage: Suitable for deep cavities and narrow gaps.
- Residue Removal: Eliminates minor flash and scratches post-molding.
Does it affect optical performance of acrylic?
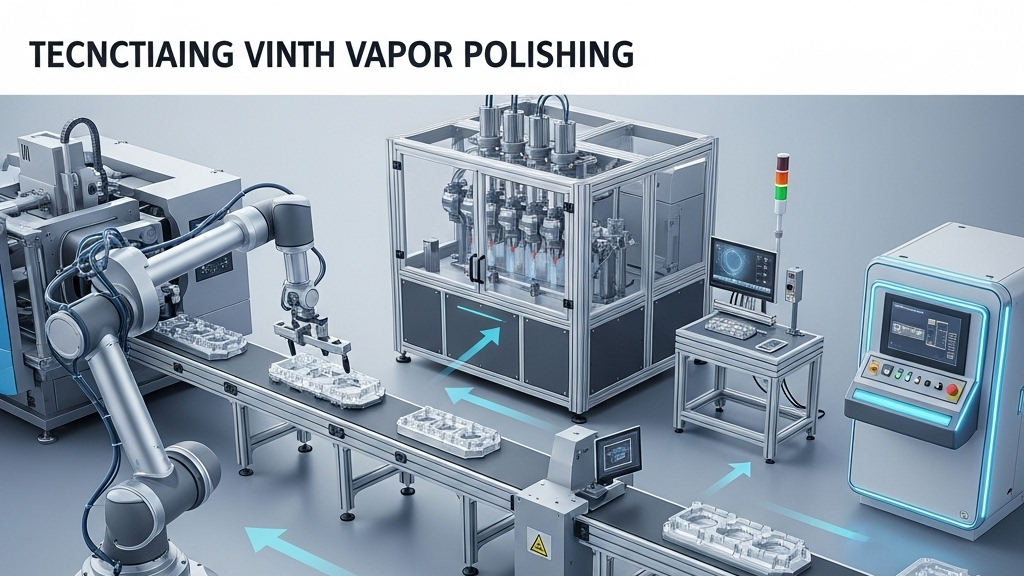
Vapor polishing thermally reflows the surface of acrylic through gas exposure, which not only maintains optical clarity but enhances smoothness and light transmission. It prevents distortion caused by micro-scratches or swirls.Uniform surface refraction is key to achieving ultra-clear results.
- Glossy Transparency: Enhances clarity and reduces diffraction.
- Micro-Defect Elimination: Clears small abrasions and dust residue.
- Color Stability: Doesn’t affect original acrylic tone.
- Improved Cleanliness: Treated surfaces resist dust and particles.
How does vapor polishing affect the injection molding workflow?
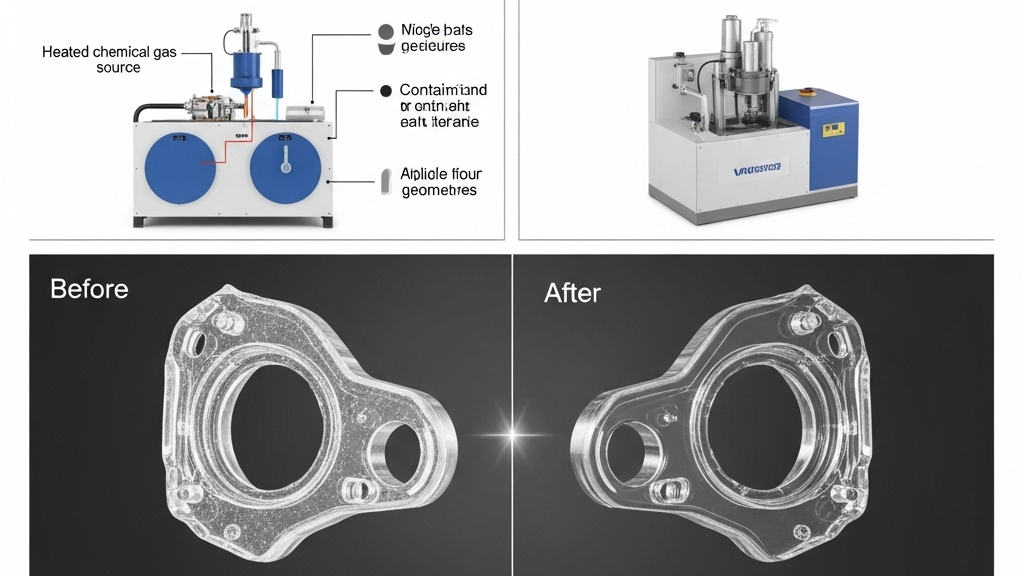
Integrating vapor polishing into the injection molding process significantly enhances visual quality, especially for products that require showroom-grade appearance before delivery. It also improves yield and reduces rework.It enables batch consistency in producing high-precision molded parts.
- Higher Yield: Fewer rejections due to surface flaws.
- Workflow Integration: Compatible with automated clamping and batch lines.
- Faster Turnaround: More efficient than manual polishing.
- Flexible Application: Used in medical, lighting, and consumer electronics.
Performance Comparison Table: Vapor vs Other Finishes
Feature/Method |
Mechanical |
Flame |
Vapor |
Ultrasonic |
Complex Geometry | Low | Medium | High | Medium |
Gloss Level | Medium | High | High | Low |
Edge Damage Risk | High | Medium | Low | None |
Process Efficiency | Medium | High | High | Medium |
Advantages of Vapor Polishing for Complex Acrylic Parts
Vapor polishing is not just for standard shapes—it brings significant benefits to customized, highly precise, transparent injection parts. Its compatibility spans across lighting, auto light guides, smart panels, and more.In the demanding clear parts market, vapor polishing has become a top-tier solution.
1.Wide Applications: Used in smart homes, automotive interiors, and medical displays.
2.Visual Enhancement: Delivers consistent, mirror-like finishes for complex shapes.
3.Easy Customization: Adapts to various sizes, thicknesses, and mold specs.
4.Eco-Compatible: Uses environmentally friendly gas formulas, supporting green production.
Conclusion
Vapor polishing proves to be highly adaptable and efficient for complex acrylic injection-molded products, addressing areas unreachable by traditional methods. It not only boosts surface quality but also supports scalable, repeatable production.Its balance of performance and quality makes it a preferred solution in high-end manufacturing.
For expert assistance in implementing for your production needs, visit our resource center or contact us. Let’s help you scale up your manufacturing with precision and efficiency!
Post time: Jul-07-2025