Stamping is a manufacturing process used to shape or form metal sheets or strips by applying force through a die or a series of dies. It involves the use of a press, which applies pressure to the metal material, causing it to deform and take on the shape of the die.
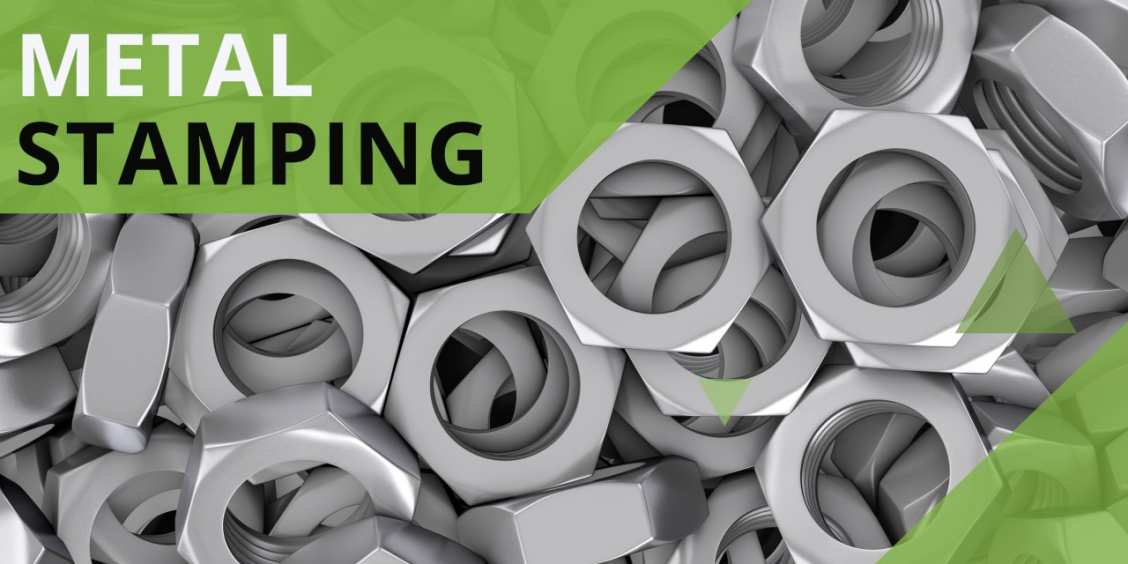

What are the process steps of stamping?
①Design and Engineering: The process begins with the design and engineering of the stamped part. This involves creating the part geometry, determining the material specifications, and designing the die and tooling required for the stamping process.
②Material Preparation: The metal sheets or strips, known as stock or blanks, are prepared for the stamping process. This may involve cutting the stock into the appropriate size and shape to fit the dies and removing any surface contaminants or imperfections.
③Die Setup: The dies, which consist of a punch and a die cavity, are installed in a stamping press. The dies are precisely aligned and securely clamped in place to ensure accurate and consistent stamping.
④Feeding: The stock material is fed into the stamping press, either manually or automatically. The feeding mechanism ensures that the stock is properly positioned under the dies for each stamping cycle.
⑤Stamping Operation: The stamping press applies a significant amount of force to the stock material, causing it to deform and take on the shape of the die cavity. This step typically involves one or more operations, such as blanking (cutting out the desired shape), bending (forming angles or curves), drawing (stretching the material into a deeper shape), or forming (creating specific features or patterns).
⑥Part Removal: After the stamping operation is complete, the stamped part is removed from the die. This can be done manually or with the help of automation, such as robotic arms or conveyor systems.
⑦Secondary Operations: Depending on the specific requirements of the part, additional secondary operations may be performed. These can include deburring (removing sharp edges or burrs), surface finishing (such as polishing or coating), assembly, or quality inspection.
⑧Quality Inspection: The stamped parts undergo a thorough inspection to ensure they meet the specified quality standards. This can involve dimensional measurements, visual inspection, material testing, or other quality control procedures.
⑨Packaging and Shipping: Once the stamped parts pass the quality inspection, they are packaged according to the specific requirements and prepared for shipping or further processing.
It is important to note that the exact process steps may vary depending on the complexity of the part, the chosen stamping method, and other factors specific to the manufacturing setup.

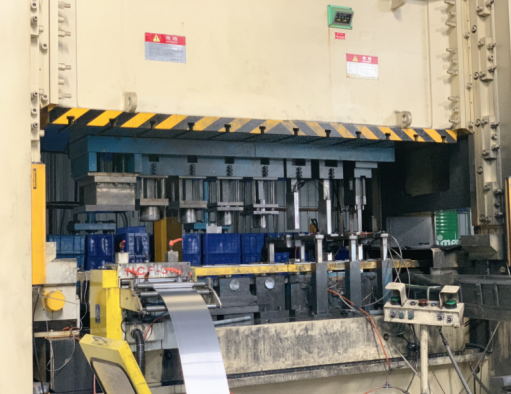
See What Makes stamping So Popular
Cost-effective: Stamping offers cost advantages due to its high production efficiency. The process allows for rapid and automated production of large quantities of parts, reducing labor costs and increasing overall cost-effectiveness.
Material Compatibility: Stamping can be applied to various materials, including metals (such as steel, aluminum, and copper) and some plastics. This flexibility allows manufacturers to select the most suitable material for their specific application requirements, considering factors like strength, durability, and conductivity.
High Precision: Stamping processes can achieve high levels of dimensional accuracy and repeatability. By employing advanced tooling and die technology, precise and consistent parts can be produced, meeting tight tolerances and quality standards.
Speed and Efficiency: Stamping operations are typically fast and efficient. With automated feeding and press systems, stamping can achieve high production rates, reducing lead times and increasing overall productivity.
Strength and Durability: Stamped parts often exhibit excellent mechanical properties, including strength, rigidity, and durability. The deformation and work hardening that occur during the stamping process enhance the structural integrity of the parts, making them suitable for demanding applications.
Scalability: Stamping can accommodate both low and high-volume production requirements. It is well-suited for mass production due to its high-speed, automated processes. At the same time, it can also be adapted for smaller production runs or prototyping, offering flexibility in meeting different manufacturing needs.
Integration with Other Processes: Stamping can be easily integrated with other manufacturing processes such as welding, assembly, and surface finishing. This allows for streamlined production workflows and the creation of complex assemblies or finished products.
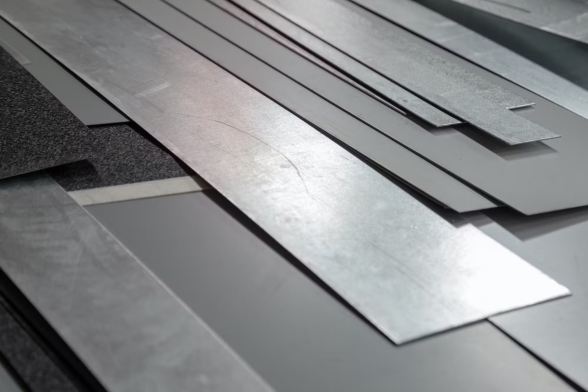
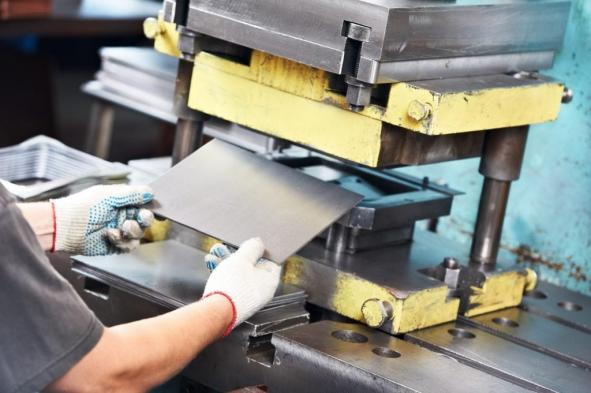
When choosing the stamping process according to the actual situation, several factors should be considered:
Material: Identify the type of metal or alloy to be stamped. Different metals have different characteristics and properties, such as strength, ductility, and thickness. Consider the specific requirements of the part or product and choose a stamping process that is suitable for the selected material.
Complexity of the Part: Evaluate the complexity of the part or product design. Determine if it has intricate shapes, bends, or features such as embossing or piercing. Different stamping processes, such as blanking, bending, or deep drawing, are suitable for different types of part geometries.
Production Volume: Consider the required production volume. Stamping processes can be adapted for both low-volume and high-volume production. For high-volume production, progressive die stamping or transfer stamping may be appropriate, while for low-volume or prototype production, single-stage or compound die stamping can be used.
Tolerance and Precision: Evaluate the required dimensional accuracy and tolerances of the stamped part. Some stamping processes, such as fine blanking or precision stamping, can achieve tighter tolerances and higher precision compared to standard stamping processes. Consider the level of precision required for the specific part or product.
Surface Finish: Assess the desired surface finish of the stamped part. Certain stamping processes may leave marks or require additional finishing steps to achieve the desired surface quality. Consider if secondary operations such as deburring or polishing are required.
Tooling and Equipment: Evaluate the availability and cost of tooling and equipment required for the stamping process. Different stamping processes may require specific dies, punches, or press equipment. Consider the lead time and cost of tooling, as well as the feasibility of acquiring or modifying the necessary equipment.
Cost and Efficiency: Evaluate the overall cost-effectiveness and efficiency of the stamping process. Consider factors such as material costs, tooling expenses, production cycle time, energy consumption, and labor requirements. Compare the advantages and limitations of different stamping processes to determine the most cost-effective option for the specific production requirements.
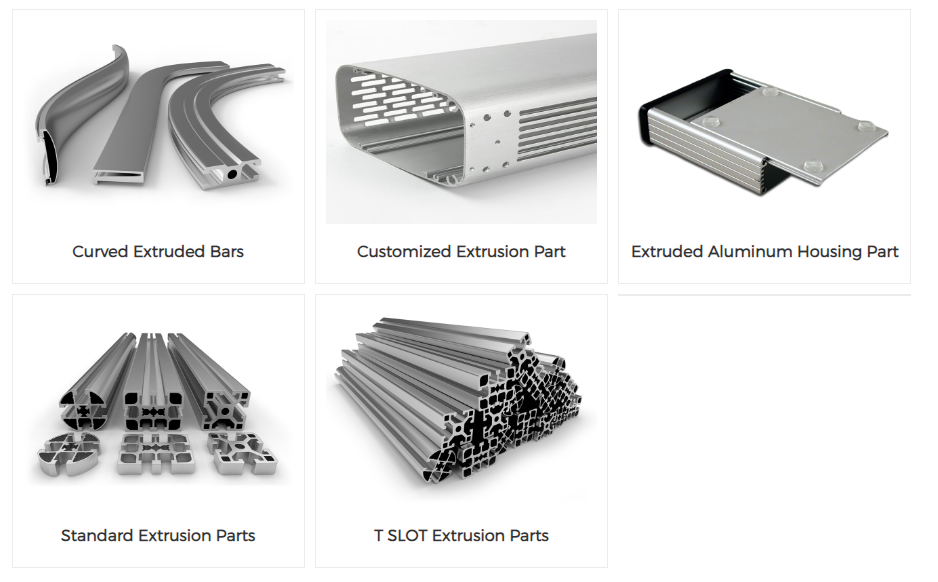
By carefully considering these factors and consulting with experts in the field of stamping, such as xiamenruicheng,you can make an informed decision and select the most appropriate stamping process for your specific situation.
Post time: Feb-21-2024